Imagine a giant gigafactory floor where every move must be perfect. A slip or shake ruins a battery cell. Now picture a system so smooth and reliable, it makes thousands of exact moves every hour, building the batteries that will power tomorrow’s electric cars. This isn't magic—it’s the power of servo cylinders at work.
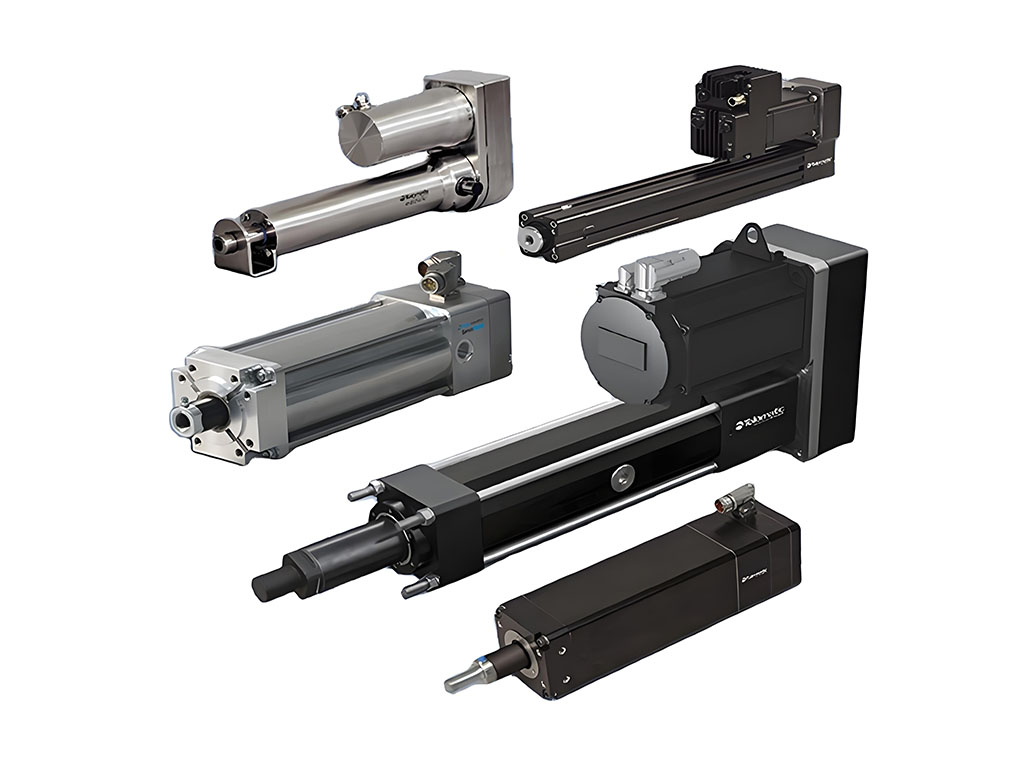
The Core Challenge: Meeting the Demands of EV Battery Manufacturing
Building an EV battery is like building a skyscraper, but on a tiny scale. Inside every battery pack, you find layers—anodes, cathodes, separators—stacked and pressed together with care. If even one layer is out of place by a hair, the battery weakens or fails.
That’s why cell stacking and module assembly call for:
- Micron-level precision (imagine cutting a hair into hundred pieces and stacking them!)
- Delicate handling (soft foils, thin separators)
- A clean, dust-free place (think of an ISO Class 7 cleanroom)
- Fast but repeatable motion (no hiccups or stutters)
- Careful tracking, because a lost step means wasted parts
Mistakes here are more than costly—they hurt battery life, safety, and your bottom line.
What Are Servo Cylinders and How Do They Work?
Servo cylinders are not just fancy metal tubes. They’re electromechanical heroes, turning the spin of a servo motor into a push or pull motion—moving straight with incredible accuracy.
Here’s what’s inside a servo cylinder:
- A servo motor at its heart—smart and strong
- A ballscrew or planetary roller screw—this transforms spinning motion into straight motion
- Linear guides—smooth out every move
- A feedback encoder—like eyes and ears, checking position every millisecond
This system works in a closed loop. That means it checks itself—detecting and fixing tiny errors on the fly. Unlike old-school pneumatic or hydraulic cylinders, which only know two speeds (on or off), servo cylinders listen and adapt, creating controlled, programmable movement.
The Unmatched Advantages: Why Servo Cylinders Dominate EV Battery Production
Pinpoint Precision and Repeatability: The Foundation of Quality
Imagine trying to stack playing cards blindfolded. That’s how tough battery building would be without precision. Servo cylinders nail positioning within ±10 microns—that’s smaller than a red blood cell. Over months of production, they repeat the same move, again and again, never drifting.
- High-speed lines need this reliability to keep quality up and waste down
- Even small errors can cause a battery to lose power or become dangerous
Dynamic Control: Force, Speed, and Position on Demand
One size doesn’t fit all in battery making. Sometimes you need a gentle press, other times a stronger force. Servo cylinders let you adjust force, speed, and position with the push of a button or a tweak in the code.
This matters most during:
- Electrode pressing—apply just enough pressure, no more
- Material dispensing—no splatters or drips
Change the recipe? Just program a new motion. There’s no need to swap parts or adjust bolts by hand.
Energy Efficiency: A Greener and Leaner Operation
Here’s a money-saver. Pneumatic cylinders gobble up air all day, and hydraulics need pumps humming. Servo cylinders use power only when moving. According to Parker Hannifin, you can save up to 80% energy compared to pneumatics for these stop/run tasks. Over a year, that’s a big dent in your energy bill, making your line greener too.
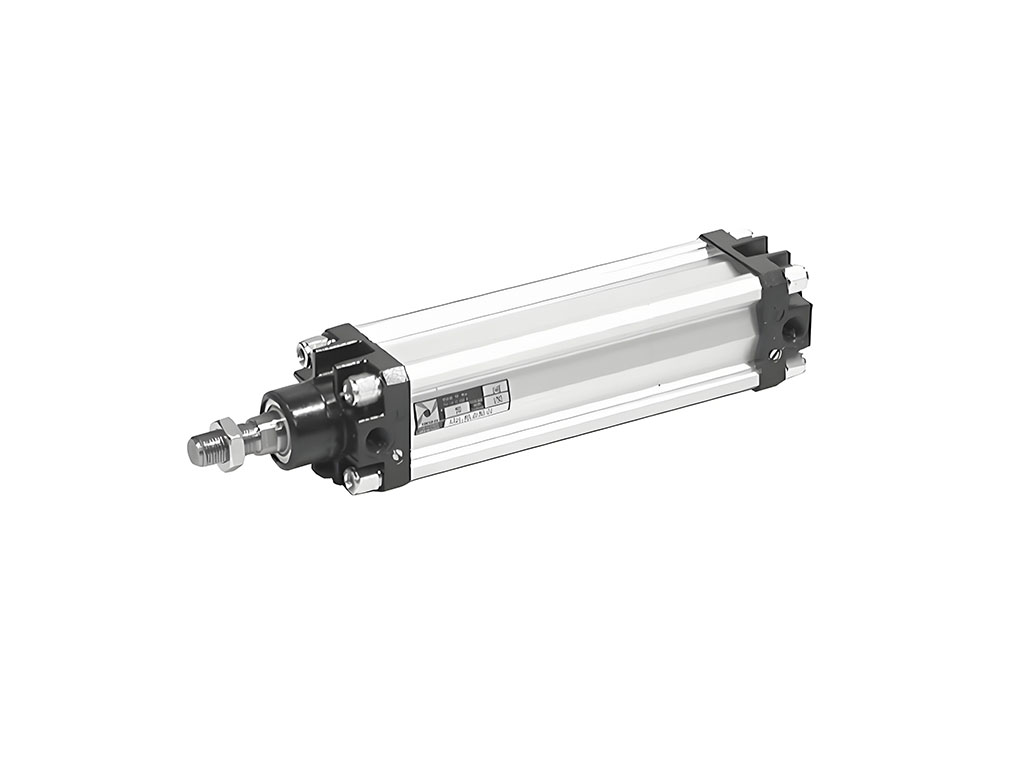
Clean, Quiet, and Data-Rich Operation
Servo cylinders run without messy oil or blasts of air. There's no risk of leaks or dust—perfect for cleanrooms. They’re so quiet you might forget they’re there (your team won’t miss the hiss of pneumatics).
Just as important, their smart sensors track every move, sending real-time data for predictive maintenance. If something’s off, you’ll know before anything breaks—reducing downtime.
Reduced Maintenance & Longer Lifespan
Servo cylinders need less fuss. They have fewer parts to wear out than hydraulic or pneumatic systems. With robust designs, they handle 24/7 work and keep going strong. That means less time fixing things and more time building batteries.
Key Applications of Servo Cylinders in EV Battery Production Lines
Electrode Stacking and Alignment
Each cell in your battery needs layers of electrode and separator—lined up tight. Servo cylinders keep placement spot-on. This prevents shorts and ensures every bit of energy fits inside the cell.
Cell Pressing and Compaction
Making the battery cell snug matters for durability and output. Servo cylinders apply just the right force, compacting parts without squashing them. Achieving this balance means longer-lasting, safer batteries.
Module and Pack Assembly
Now, cells get packed and joined. Precise positioning matters for welding, gluing, and connecting tabs. Servo cylinders put every cell right where it belongs, leading to tight, safe modules.
Quality Control and Inspection
Consistency is king. Servo cylinders move probes, cameras, and test sensors with exact control. Quality checks catch defects before modules leave the line, keeping end-users happy and safe.
Servo vs. The Rest: Why Alternatives Fall Short
Servo vs. Pneumatic Cylinders
Pneumatic cylinders are cheap to buy but expensive to run. They:
- Can't match the fine control of servos
- Waste a lot of air and energy
- Can blow dust, risking contamination
- Struggle with speed and repeatability
Servo vs. Hydraulic Cylinders
Hydraulics are strong, but they have big downsides:
- Oil leaks mean big cleanup and risk to battery quality
- Complex controls make them hard to program for small, detailed moves
- Energy waste is high, pumps must run all the time
Key Data Insights from EV Battery Production Automation
- Precision: Getting stacking accuracy below ±10 microns matters for safety and battery life (Journal of Battery Manufacturing, 2022).
- Energy savings: Servo cylinders use up to 80% less energy than pneumatics (Parker Hannifin White Paper).
- Throughput and yield: A major EV battery maker saw a 15% boost in speed and 5% less scrap after swapping to servo-driven cylinders (Automotive Manufacturing Solutions, 2023).
- Cleanroom fit: Without oil or dusty air bursts, servos fit right into high-standard rooms (Cleanroom Technology Magazine).
- Long-term savings: High startup cost pays off past three years—thanks to less energy waste and less fixing (Bosch Rexroth TCO Analysis).
- Repeatability: Even in fast lines, servo cylinders hit repeatability within ±5 microns (Festo Automation Whitepaper).
Want even more technical specs or to explore electric and servo actuator options? Dive into our servo linear actuator factory or see detailed options on electric linear actuators.
FAQ
What is a servo cylinder and how does it work?
A servo cylinder is a smart device. It uses a servo motor to create a straight push. It knows its position all the time, moving with precision and control, perfect for tasks demanding accuracy.
What is the difference between a pneumatic cylinder and a servo cylinder?
A pneumatic cylinder uses air and can’t change force or speed with precision. Servo cylinders are electric. They can adjust motion at any moment and provide data feedback for advanced controls.
Why is precision so critical in EV battery manufacturing?
Every small error in battery making lowers safety and performance. High precision builds better, longer-lasting, and safer batteries, which is why it’s non-negotiable.
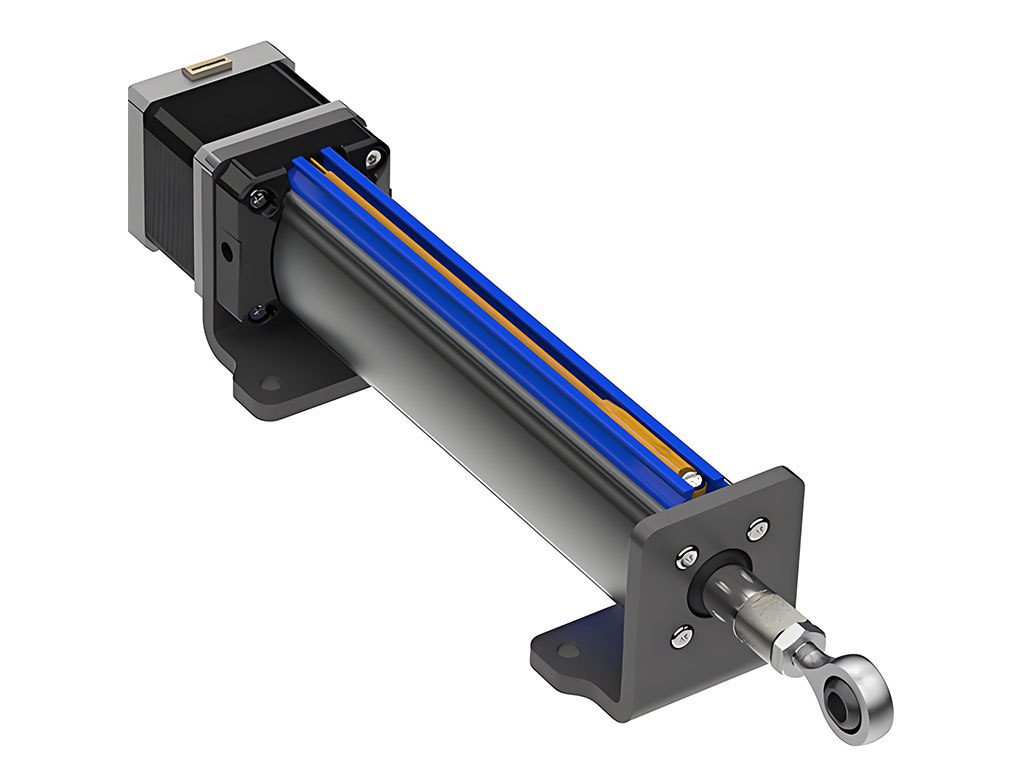
How do servo cylinders improve battery cell quality?
Their accurate, repeatable motion means every cell is built the same way. That tightens quality, reduces mistakes, and supports better battery life.
Are servo cylinders more energy efficient than hydraulic or pneumatic?
Yes—far more. They use power only while moving. Pneumatics and hydraulics waste energy, as their systems run constantly.
What are the main applications of servo cylinders in EV production lines?
They’re key for stacking, pressing, module assembly, joining, and automated inspection—wherever a perfect, repeatable move is crucial.
What is the cost implication of using servo cylinders in automation?
Startup cost is higher, but they save you money on energy, maintenance, and waste. Over 3–5 years, they are often the lowest-cost option.
Conclusion & Next Steps
Servo cylinders bring unbeatable precision, adaptable control, energy savings, and smart data to EV battery production. When you want top-quality batteries, faster output, and lower costs, servo technology stands out from the crowd.
At Jimi Technology, we don’t just sell components. We help you design smarter lines and solve tough problems. Drawing on deep industry know-how, we make high-quality servo cylinders that fit your needs. Browse our industrial automation actuators, check out electric cylinders, or connect with us as your trusted China linear actuator manufacturer.
Ready for better EV battery output, with less waste and stress? Talk with our experts today. See how servo cylinder solutions from Jimi can power your electric revolution.