Have you ever watched a machine just stop working—and workers stand around, unsure what to do next? A servo cylinder might be the silent hero or the root of the problem. These small but mighty components keep many industries moving every single day. Skip their care, and you risk an expensive, stressful breakdown. Let's make sure this never happens to you.
Why Servo Cylinder Maintenance is Non-Negotiable
Picture this. In a busy factory, a press machine needs to hit the same spot every time, and it relies on a servo cylinder to do the job. If the cylinder stops working or drifts, every part comes out wrong, the line grinds to a halt, and bosses start asking questions you don't want to answer.
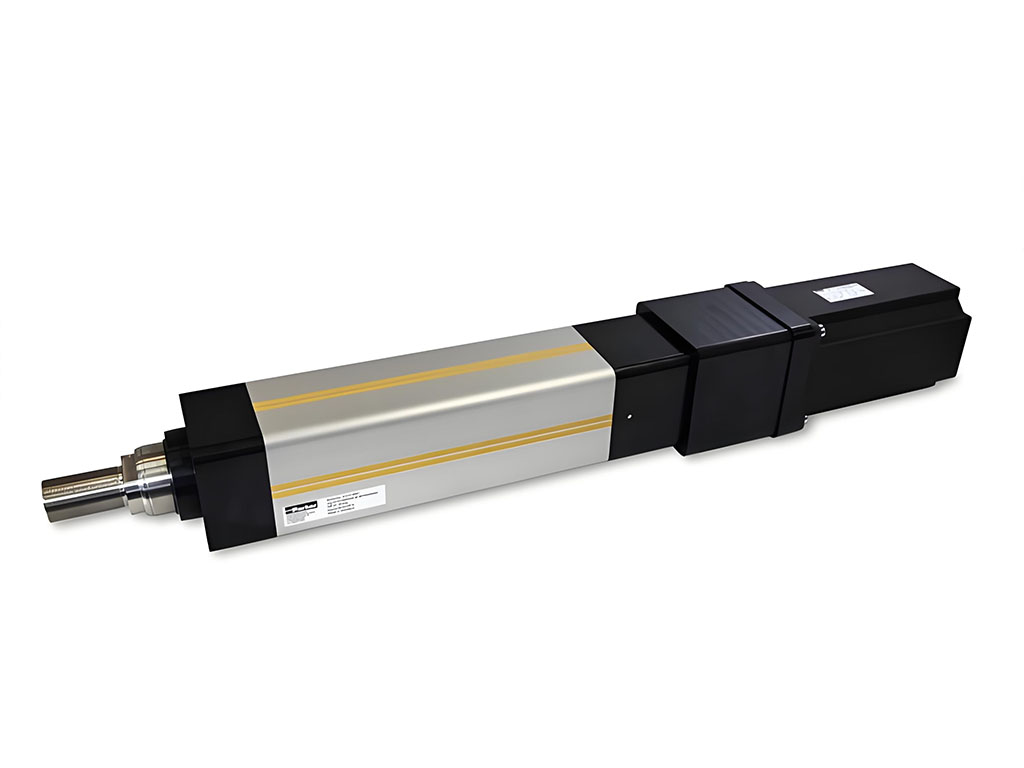
Servo cylinders are the engine behind precision. They use hydraulic power and smart feedback to move things smoothly, quickly, and with pinpoint accuracy. We at Jimi Technology know these cylinders drive everything from robots, to presses, to conveyors.
You can't cut corners here. Maintenance is your guardrail. The cost of neglect? Missed deadlines, huge repair bills, safety hazards, and unhappy customers. Even one breakdown can slash profits or damage your reputation.
Understanding Servo Cylinder Operation & Failure Modes
Servo cylinders work with a simple promise: push, pull, or press—smoothly and exactly every time. They're powered by fluid and guided by electronics like linear encoders, sensors, and a servo valve. If anything in this system slips, the effects ripple through your whole operation.
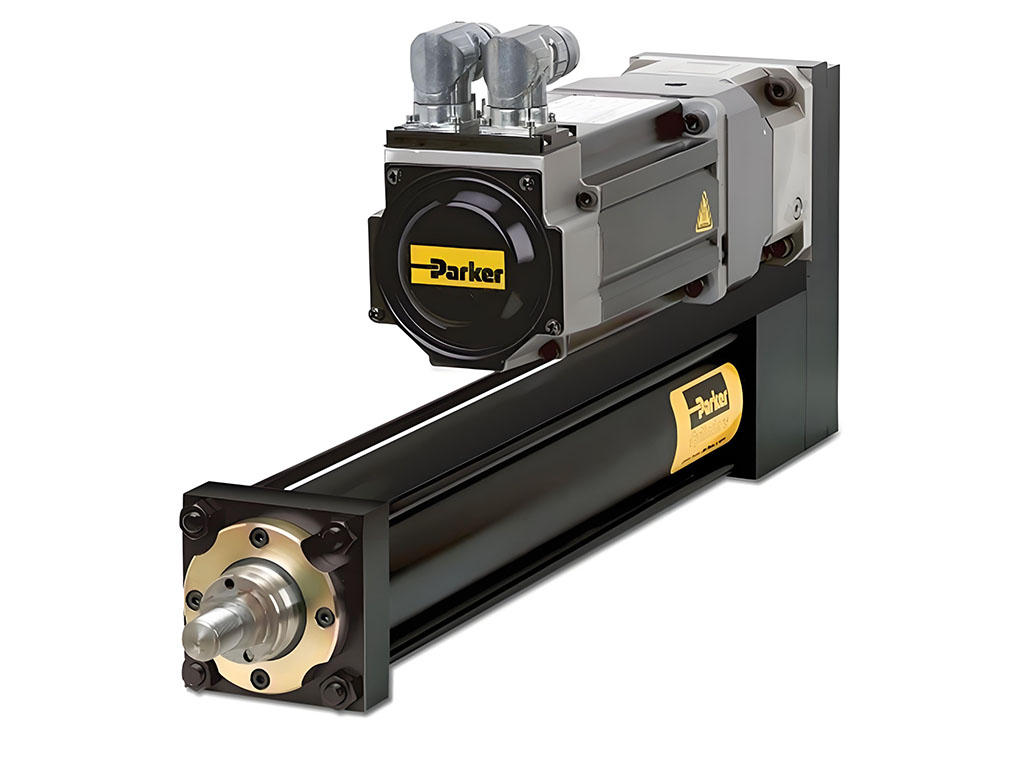
The most common reasons servo cylinders fail are:
- Seal degradation (like piston, rod, and wiper seals) lets fluid leak and dust get in.
- Fluid contamination kills performance. Oil mixed with water, air, or dirt causes massive wear.
- Sensor drift or signal loss leads to inaccurate positioning.
- Mechanical wear—especially scratches on the chrome rod—can seize up the whole cylinder.
Just one weak link—like a frayed hose or a dirty filter—can send downtime, costs, and headaches soaring.
Core Benefits of a Robust Maintenance Program
Why does preventive maintenance pay off? The numbers don't lie:
- Extend component lifespan: Up to 2-5x longer life for servo cylinders and pumps.
- Reduce downtime: Planned checkups cut unplanned shop floor stops by 25-30%, sometimes even more.
- Save money: Shifting from reactive to proactive slashes maintenance costs 15-40%. Emergency repairs cost 3-5 times more than planned fixes!
- Keep your process precise: Preventing drift and slow movement keeps your production and product quality safe.
- Protect safety: Fewer leaks and breakdowns keep people and the environment safer.
An example from an auto parts plant: They faced $50,000+ a year in breakdowns. By starting monthly fluid checks and quarterly valve tune-ups, their downtime fell 40%. Component life doubled. Quality jumped. And so did worker and customer satisfaction.
Pre-Maintenance Safety & Preparation: Your First Priority
Before anyone touches a cylinder, think safety.
- Lockout/Tagout (LOTO): Always shut down power and lock systems before you start work. Don’t take risks.
- Wear the right PPE: Gloves, goggles, and sturdy clothes keep you safe.
- Use proper tools: A torque wrench, fluid analysis kit, multimeter, and the latest logbook are musts for safe, accurate work.
- Get the paperwork: Keep the manufacturer’s manual, maintenance logs, and safety data sheets handy.
- Keep it clean: Lay down spill pads and have waste containers ready. Dirt is the enemy of moving parts.
We Jimi always suggest you pause and double-check every safety step—even if you’re in a hurry. One slip can cost you much more time and money later.
The Comprehensive Periodic Maintenance Checklist for Servo Cylinders
A great checklist acts as your roadmap. It makes sure you don’t forget the little things, which are often the most important.
Daily / Shiftly Checks (Visual & Operational)
- Look for leaks: Check the whole cylinder, including the body, rod seals, hoses, and fittings.
- Inspect the chrome rod: Are there scratches, dents, rusty spots, or nicks? Fix right away.
- Check mounting and connections: Tighten loose bolts, listen for odd sounds or extra vibration.
- Smooth motion test: Watch for jerking, sticking, or moves that "don’t feel right."
- Check fluid levels: Peek in the HPU reservoir. Top up if needed with the correct hydraulic fluid.
Weekly / Bi-Weekly Checks
- System pressure and temperature: Check your HPU gauges. Compare to the specifications.
- Fluid quality: Good oil should look clear—not milky or dirty. Suspended particles spell trouble.
- Filter condition: Are the filter indicators or gauges showing high pressure? Time to change.
- Bearings and bushings: Any extra play or rough spots? Grease or replace as necessary.
- Hose/tubing health: Look for cracks, bulges, or wear.
- Electrical connections: Gently tug sensor and servo valve wires, ensuring a snug fit.
Monthly / Quarterly Checks
- Hydraulic fluid analysis: Sample fluid and test for water, dirt, and viscosity.
- Servo valve inspection: Look for leaks and clean dust from surfaces.
- Adjust cushioning: Test the cylinder’s cushion—does it reach the end without banging?
- Check accumulator charge: For systems with an accumulator, test the pre-charge gas pressure.
- Sensor calibration: Check your LVDT or encoder for drift; adjust if needed.
- Lubricate: Hit all oil points listed in your manual.
Annually / Bi-Annually Checks
- Deep fluid analysis: Send oil for chemical and particle checks.
- Change hydraulic filters: Don’t wait for a problem. Swap filters (pressure, return, suction) on schedule.
- Check/replace seals: Worn seal kits let dirt in and fluid out—don’t delay.
- Test servo valve: Specialized checks for speed, response, and accuracy; call a pro if you need to.
- Inspect internals: For very busy cylinders or those showing wear, inspect the bore, piston, and internal seals.
- Swap worn bearings: Better safe than sorry.
- Flush system if needed: If oil is very dirty.
- Check cables: Look for cuts, frays, or kinks. Route them safely.
- Check grounding: Use a multimeter to confirm proper connection.
Key Indicators You Might Be Overlooking
Catch these signs early, and you’ll sidestep big repairs:
- Slower cycles or less force
- Position errors or drift
- Whining, knocking, or odd noises
- More heat than usual from the system
- Higher power bills
- Shaky or bouncy movement
- Filters needing constant change
Spot these? Act at once. Don’t wait for disaster.
Documentation and Record-Keeping: The Backbone of Effective Maintenance
If you don’t write it down, it didn’t happen.
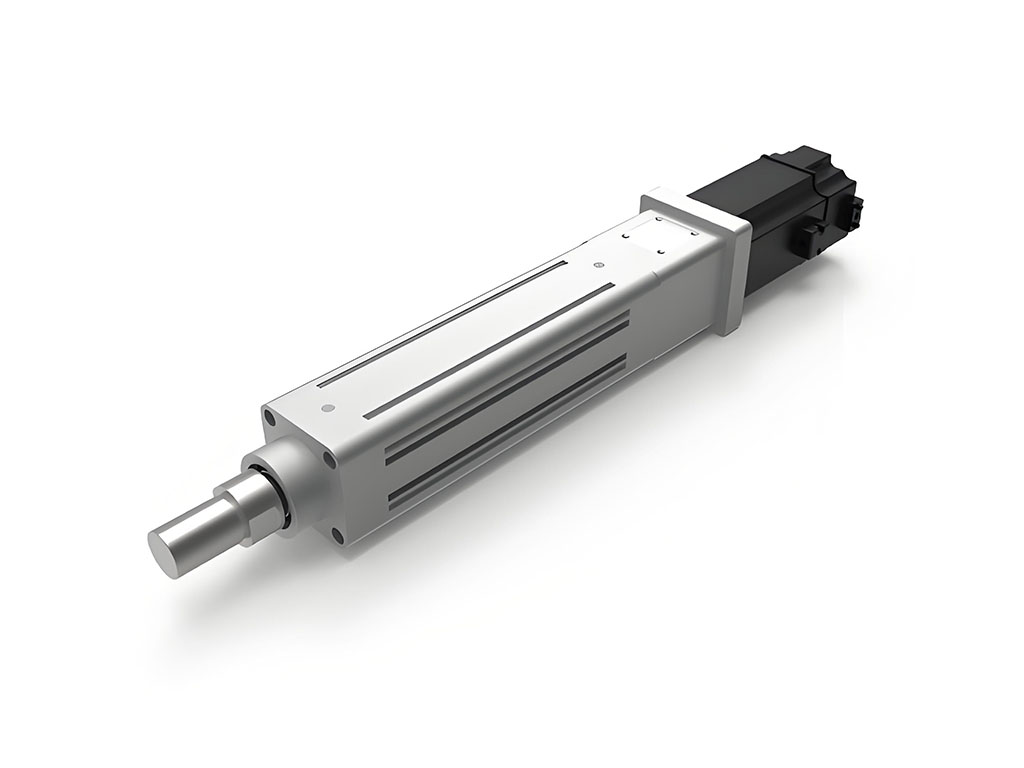
Keep a simple logbook or use a CMMS. Note every check, issue, and repair by date, what you saw, and what you did about it. Attach receipts for parts. This way, you can spot patterns, keep your warranty safe, and train new people easily. Good records can save your job when someone upstairs asks, “What happened and when?”
Expert Tips for Extending Servo Cylinder Life
- Keep it clean: Eight out of ten failures come from dirty or old oil.
- Right sizing: Don’t overload your cylinder or push it too hard.
- Fix leaks right away: Even tiny drips can be a giant problem tomorrow.
- Use only quality parts: Cheap spares don’t last and can void your warranty.
- Train your team regularly: Maintenance is a skill. Keep learning.
- Try condition monitoring: Sensors and IoT can catch brewing problems before you can even hear them.
If you’re ready for best-in-class performance, look into our Electric Linear Actuators, Servo Motor Actuators or check out advanced options for Actuators with Position Feedback. We Jimi keep quality, precision, and innovation front and center in every product.
Why Choose Jimi Technology?
We at Jimi Technology have spent years in the trenches with servo cylinders, from the smallest Light-Duty / Miniature Actuators to the most rugged Heavy-Duty Linear Actuators. We don’t just sell a product—we partner in your success. Our manufacturing is strong, and our expertise runs deep. From the first sketch to real-world operation, Jimi stands with you.
Need help designing the right solution or setting up a perfect maintenance plan? Our technical team is your go-to resource. We’re not happy unless your line is running smoothly.
Conclusion: Proactive Maintenance as a Strategic Asset
Don’t let your servo cylinders become the weakest link. Systematic, step-by-step care pays for itself in uptime, safety, and peace of mind.
Ready to take your plant or lab to the next level? Start with this checklist, trust in Jimi’s expertise, and look forward to fewer surprises and flawless results. Find your perfect cylinder or ask for guidance at China Electric Cylinder Factory or explore our full industrial automation solutions.
Make good maintenance your competitive edge—the best runs always start with preparation.