The Imperative for Precision & Power in Car Body Welding
Picture an automotive assembly line. Sparks fly. Robots reach in, pressing metal panels, shaping each car with quick, precise movements. At the heart of these lines, welding joins the steel together, holding the future of every car. If the force of each weld shifts, the car's body weakens. If the process moves too slowly, production backs up. With more electric vehicles and stronger, lighter materials coming, you need spot-on accuracy and speed — every single time.
Traditional pneumatic and hydraulic cylinder systems once carried the load. They struggle, though, with changing force, wasted energy, leaks, and high upkeep. Plant managers know these problems. Maybe you’re fighting air leaks or wrestling with messy oil today. Precision and uptime are more critical than ever. That's why manufacturers worldwide need a new solution — fast, clean, and reliable.
What Are High-Thrust Electric Cylinders? Technology Explained
High-thrust electric cylinders aren't just motors and rods. They're machines that use a powerful servo motor to turn rotary energy into strong, direct push-and-pull movement. Picture a very strong arm, perfectly controlled by tiny electric signals. Inside, you'll find a ball screw or roller screw, sliding and spinning to make straight-line power. A feedback encoder tells the motor exactly where to go and how hard to push. This closed-loop control keeps everything precise, even when demands shift or conditions change.
These cylinders push with the muscle needed for car body welding — from just a few kilonewtons (kN) up to dozens for the toughest steels or multiple layered joins. Some premium Electric Cylinders even offer thrust beyond 30T (think: many tons of force, yet always under sharp electronic control).
Distinguishing High-Thrust Capabilities
What makes an electric cylinder truly “high-thrust”? In automotive welding, you’re looking at:
- Force often between 3 kN and 15 kN (sometimes more for advanced jobs)
- Blazing-fast speeds and snap-quick acceleration
- Pinpoint repeatability down to just a few microns (±5µm)
- Heavy-duty construction for the harsh shop floor
- Robust, long-duty cycles — these keep pushing for years without wearing out
Every detail matters, from the design of the servo motor system to the selection of tight, solid guides. It’s these little differences that mean your welds always stay strong and your line keeps rolling.
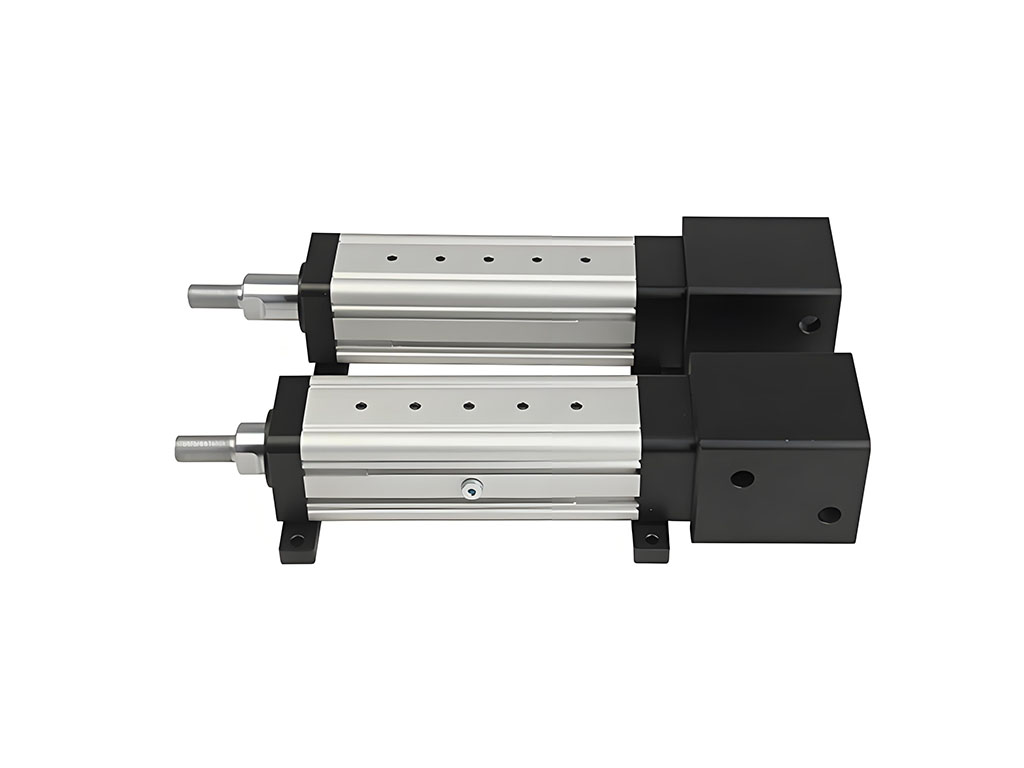
Unlocking Unprecedented Advantages: Why Electric Cylinders Lead in Welding
Let’s zero in on the clear wins you gain by switching to high-thrust electric cylinders, like the trusted 250 Series Max Load Servo Electric Cylinder or 110 Series Heavy Duty Electric Cylinder.
1. Weld Quality & Consistency Jump
Spot welding isn’t forgiving. With electric cylinders, every weld gets exactly the right force, right when you want it. You can program the force profile for each job, so there’s less spatter and better nugget formation. Consistency isn't luck—it's built right into the drive.
2. Faster Production, Higher Throughput
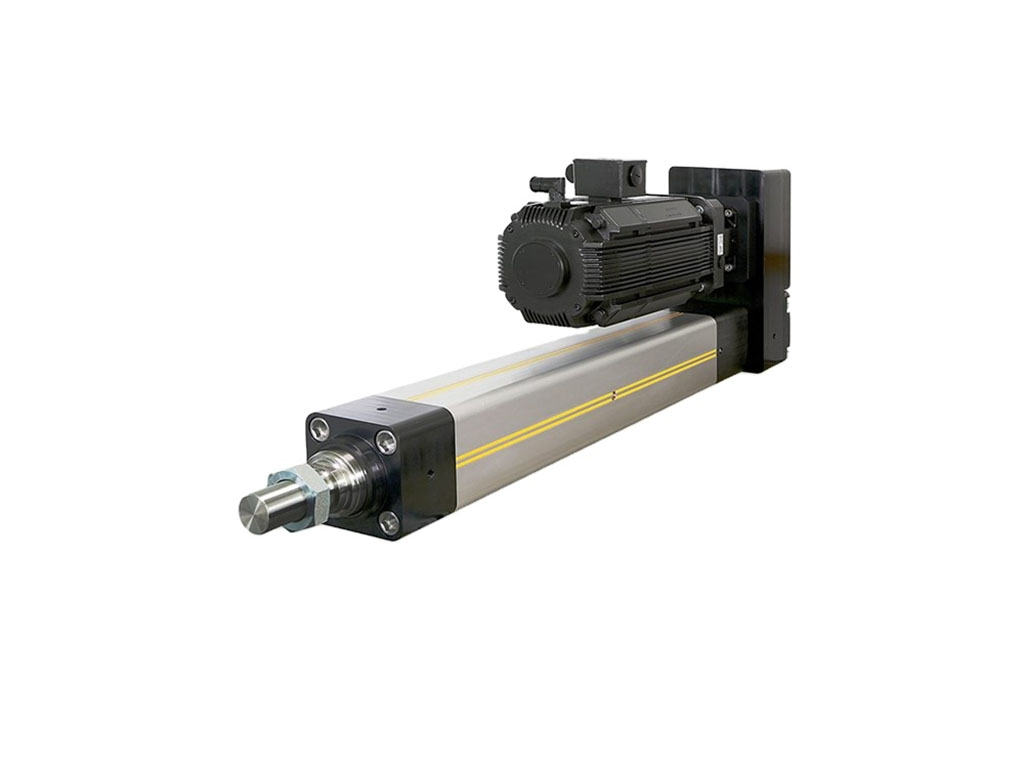
Time is money. Electric cylinders can snap into position and move at speeds that slice seconds from every cycle. Car makers often see cycle-time improvements of 15-25%, boosting your output without training your staff to work faster.
3. Energy Savings & Cost Control
Forget the noisy compressors and high energy bills. Studies show electric cylinders use up to 80% less energy than air-driven systems in tough, high-usage conditions. The savings add up, both in your monthly expenses and your environmental impact.
4. Quieter, Cleaner, and Safer Operation
No oil to leak. No hydraulic fluid to discard. The air stays clean. Your floor is quieter, too, which means a nicer, safer workplace for everyone on your team.
5. Simpler Maintenance, Less Downtime
Electric cylinders have fewer moving parts. No seals to blow, no valves to gum up. In fact, their lifetime maintenance costs run 50-70% lower than hydraulics. When you do need a tweak, troubleshooting is straightforward and cost-effective.
Here’s a quick comparison to show the difference:
Feature | Electric Cylinder | Hydraulic Cylinder | Pneumatic Cylinder |
---|---|---|---|
Max Precision (Repeatability) | ±5µm | ±50µm | ±100µm |
Energy Efficiency | High | Medium | Low |
Maintenance Needs | Low | High | Medium |
Cycle Time | Fast | Medium | Fast |
Environmental Impact | Low | High | Medium |
Suitable Applications | Welding, Clamp | Heavy Lift | Light Move |
Core Applications in Automotive Car Body Welding
Electric cylinders now shine in several key welding roles inside the car plant:
- Resistance Spot Welding. This is the workhorse — pushing the electrodes together with exact, repeatable force.
- Seam Welding & Roller Hemming. Making long, leak-free seams needs gentle touch and steady speed. Electric cylinders deliver both.
- Robotic Welding Cell Integration. Leading robot makers like KUKA and ABB build their systems to work hand-in-glove with electric servo guns. Plug in, sync up, and get top control at every touchpoint.
- Clamping and Holding. When positioning panels or reinforcing lines, electric cylinders hold firm so your parts never budge.
For all these jobs, you want a proven partner. That’s where Jimi Technology steps in.
Electric vs. Traditional: A Comparative Analysis for Welding
Old-school pneumatic cylinders sound simple. They push with air—quick but jumpy. The compressibility of air means the force wobbles, and the energy needed for all that compressed air creates high costs and plenty of noise.
Hydraulic cylinders bring big muscle but at a price. They need pumps, hoses, and fluid. They’re messy (ever chased an oil leak under a robot?), expensive to maintain, and not as sharp when forcing down to the last micron. For ultra-heavy-duty one-off tasks, hydraulics persist. Yet the tide has turned.
Electric cylinders leap ahead on nearly every metric:
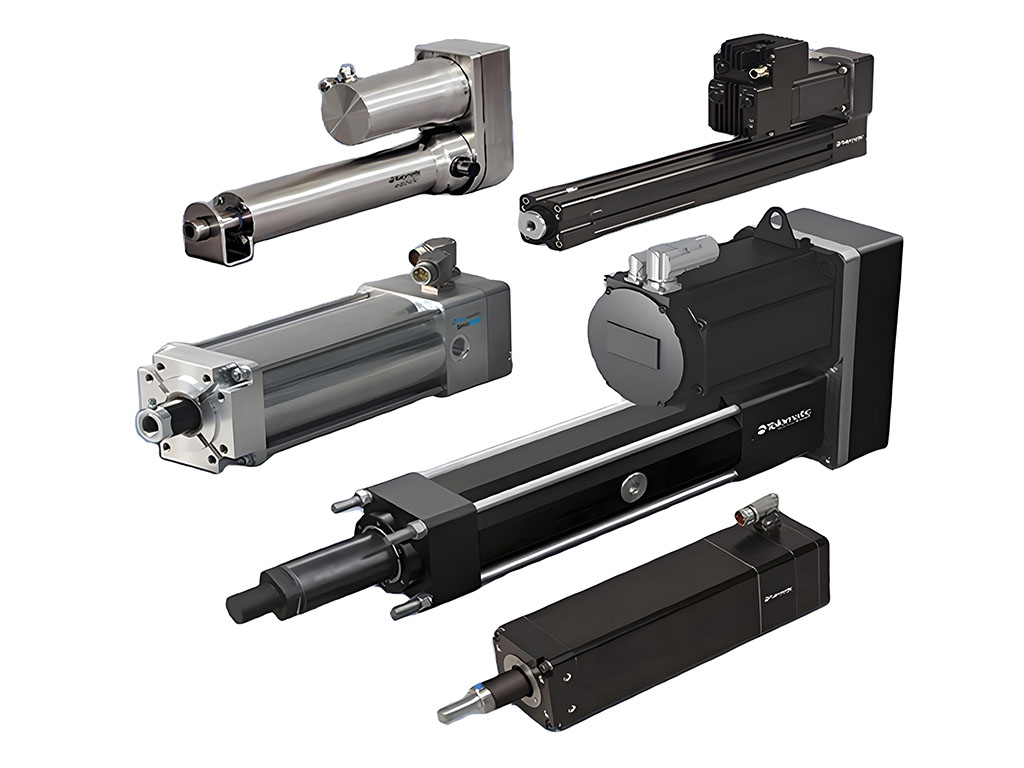
- Total Cost of Ownership — much lower
- Environment — no oil, no air leaks, no waste
- Speed and Precision — exactly on target, time after time
- Simplicity — just wire it up, plug it in, and go
Curious about these differences for your own system? Check out more details on hydraulic linear actuators or see our electric cylinder solutions ready for action.
Integration & Control: The Brains Behind the Power
Here’s where electric cylinders show real smarts. Using servo drives, PLCs, and direct motion controllers from companies like Siemens and Rockwell, you get brainpower behind every push.
Thanks to fieldbus communication protocols like EtherCAT and PROFINET, electric cylinders talk easily with your robots and control rooms. Closed-loop feedback keeps position and force exactly locked in, and you open the door to Industry 4.0 — collecting data, monitoring wear, and planning maintenance before a hiccup halts your line.
If you want to automate further or connect cylinders into bigger digital systems, the path is smooth. Look into advanced actuator controllers for seamless integration.
Key Considerations for Selecting High-Thrust Electric Cylinders
Choosing the right cylinder comes down to a few key questions:
- How much force do you truly need (peak and steady)?
- What stroke length and speed will keep you on target?
- Will the cylinder see heavy use, or sit idle?
- Any tough shop conditions — water, dust, heat?
- Are your robots and controls ready to connect?
A reputable supplier walks you through each answer. And while performance is king, don’t forget support and after-sales service.
Frequently Asked Questions
What are the main benefits of using electric cylinders for spot welding in automotive?
Electric cylinders give stronger, more exact force, better weld quality, faster cycles, major energy savings, and lower maintenance compared to air or hydraulic cylinders.
How do high-thrust electric cylinders improve weld quality compared to pneumatic systems?
They cut force fluctuation to near zero. This means every weld gets the same, optimal pressure, reducing waste and flaws.
Are electric cylinders more energy-efficient than hydraulic or pneumatic cylinders for welding?
Yes — often cutting energy use by up to 80%. No compressors, no pumps, just smooth electric motion.
What is the typical lifespan and maintenance requirement of an electric welding cylinder?
Most last many years and need little attention. With few moving parts and no fluids, costs drop by 50-70% over their life.
Can electric cylinders be easily integrated into existing robotic welding cells?
Absolutely. Top brands design electric cylinders for simple, reliable plug-in with major robotics brands.
What thrust forces are typically needed for resistance spot welding on car bodies?
Force ranges from 3kN to 15kN are common, with higher numbers for exotic applications.
How do electric cylinders contribute to faster cycle times in automotive production?
Speed, sharp repeatability, and reliable positioning cut welding cycle time by 15-25%.
What control systems are compatible with high-thrust electric cylinders for precise welding?
Any leading PLC, servo controller, or fieldbus protocol like EtherCAT or PROFINET fits.
What are the environmental advantages of switching to electric welding cylinders?
No oil leaks, no fluid disposal, less noise, less energy use, and a far greener profile.
Which manufacturers offer reliable high-thrust electric cylinders for industrial welding?
Jimi Technology is a leader, trusted for performance, support, and expertise.
Conclusion & The Future of Automotive Welding
High-thrust electric cylinders are transforming car body welding. They drive precision, cut waste, clean up the shop, and speed production. With growing demand for smarter, greener factories, they’re no longer an option. They’re the standard for teams who want the best. We at Jimi Technology have led this shift, delivering cutting-edge actuators loved by engineers worldwide.
Ready to take the next step? Explore our Servo Linear Actuator Factory, Industrial Linear Actuators, or connect with us directly. Power your line, perfect your weld, and steer your plant into the future — one electric cylinder at a time.