What Are Food-Grade Stainless Steel Electric Cylinders and Why Are They Essential for F&B?
Picture a food factory where machines move with perfect accuracy, and everything looks clean and shiny. There's a reason for that shine: food-grade stainless steel electric cylinders. These small but mighty devices power the lifts, pushes, and even the tilts you need in processing—just at the press of a button.
So, what is an electric cylinder? It's a simple device that uses an electric motor to change spinning motion into straight-line (linear) movement. It’s like a magic arm that moves up, down, or sideways when you tell it to. The "food-grade stainless steel" part means this arm can be used around food. It’s smooth, shiny, and doesn’t rust. Most often, you’ll see types like 304 or especially 316L stainless steel. These grades resist corrosion, clean up easily, and won’t trap germs or dirt. In the food business, safety is key. Food-grade cylinders get designed with no sharp corners, minimal gaps, rounded edges, and tight seals. Bacteria or leftover bits? They don’t stand a chance here.
Why does this matter? You don’t want germs growing or food getting stuck where you can’t clean. These cylinders help prevent that—guaranteed.
Electric vs. Traditional Actuators: A Game-Changer for F&B Operations
Let’s look at how these compare to the old ways, like pneumatic cylinders or hydraulic cylinders. Maybe you’ve used them before—air or oil pushes a rod forward and back.
Unmatched Precision and Control for Critical Processes
Electric cylinders win big on precision. You can set them to stop at any spot you want, every single time. Need to fill a bottle to exactly 300ml or slice cheese to an exact 10mm? No problem. This precise control means less waste and the same portion every run. According to major manufacturers, you get repeatability down to 0.02 mm—that’s like splitting a hair!
Significant Energy Savings and Reduced Operating Costs
Here’s a huge plus: you only use power when the cylinders move. No need to keep noisy air compressors running all the time. That means you save energy—and money. One technical paper shows switching from pneumatics to electric can cut power use by up to 90%. Over a year, that’s cash in the bank.
Enhanced Cleanliness and Reduced Contamination Risk
No oil leaks. No blown seals spraying air. Just smooth, sealed movement. This makes electric cylinders the safe choice for washdown environments. They help you meet strict food standards, like FDA or EHEDG guidelines, where even a tiny leak could risk a recall.
Lower Maintenance Demands and Longer Lifespan
Fewer moving parts mean fewer things break. If you’re tired of constant fixes or unscheduled downtime, electric cylinders show up strong here too. Some factories report up to 30% less surprise breakdowns after switching.
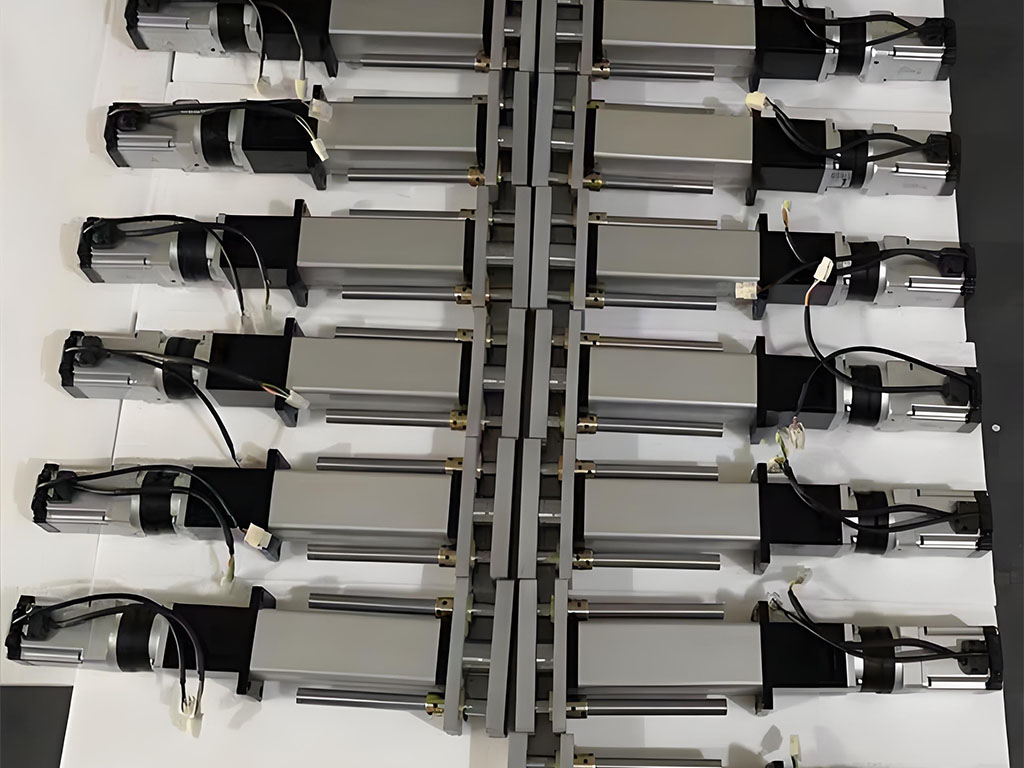
Key Features and Design Considerations for F&B Compliance
Let’s break down the essential features you’ll want.
The Importance of IP Ratings, Especially IP69K
Look for IP ratings—a number system that shows how well stuff handles water and dust. For food factories, the IP69K rating stands at the top. It means a cylinder can take high-pressure, high-temp water jets from all directions. That’s the toughest cleaning test gear can face.
Choosing the Right Stainless Steel Grade (304 vs. 316L)
Both 304 and 316L stainless steel shine, but 316L adds molybdenum—making it even tougher against harsh cleaning agents and salt. Got sauces, dairy, or any process with lots of salt? Go with 316L. These grades stand up to washdown after washdown.
FDA-Approved Materials and Seal Technology
The secret to true food safety isn’t just the metal—it’s also the seals and lubricants. Only FDA-approved components should touch your products. Advanced sealing stops water, dirt, and cleaning liquids from sneaking in.
Holistic Hygienic Design: Beyond Just Materials
It’s not only about the steel—it’s about the whole shape and build. Smooth, sloped surfaces help water run off. No cracks or hidden spots. Simple details, like mounting bolts outside the food zone, all add up to one thing: easier cleaning and better safety.
Practical Applications of Food-Grade Electric Cylinders Across the F&B Industry
Where can you use these cylinders? Pretty much everywhere in a food plant:
Precise Filling and Dosing Systems
Electric cylinders let you set exact fill levels for bottles, trays, or bags—no guessing, no waste.
Automated Cutting, Slicing, and Portioning
Every slice or portion comes out the same size, every time. That keeps your customers happy and saves you money in materials.
Reliable Packaging and Sealing Operations
From sealing bags to closing trays, these cylinders get timing and pressure right.
Dynamic Sorting and Diverting Mechanisms
Need to push snack packs onto the right conveyor? These are your go-to.
General Automation in Harsh Washdown Zones
If it needs to move and gets washed often, an electric cylinder with a high IP rating is the best bet. For heavy loads, check out solutions like heavy-duty linear actuators.
Navigating Regulatory Compliance: FDA, EHEDG, and Beyond
Understanding FDA Guidelines for Food Contact Materials
The FDA spells out which materials can safely touch food. FDA-compliant cylinders use approved metals and seals, so you stay in the clear.
Adhering to EHEDG Principles for Hygienic Design
The EHEDG sets rules for easy-to-clean equipment. Following these rules isn’t just smart—it’s a must for exporting to Europe or operating top-tier plants.
Other Relevant Certifications (e.g., NSF, ISO)
Some buyers or markets need extra stamps, like NSF or ISO marks. These show your setup’s truly world-class.
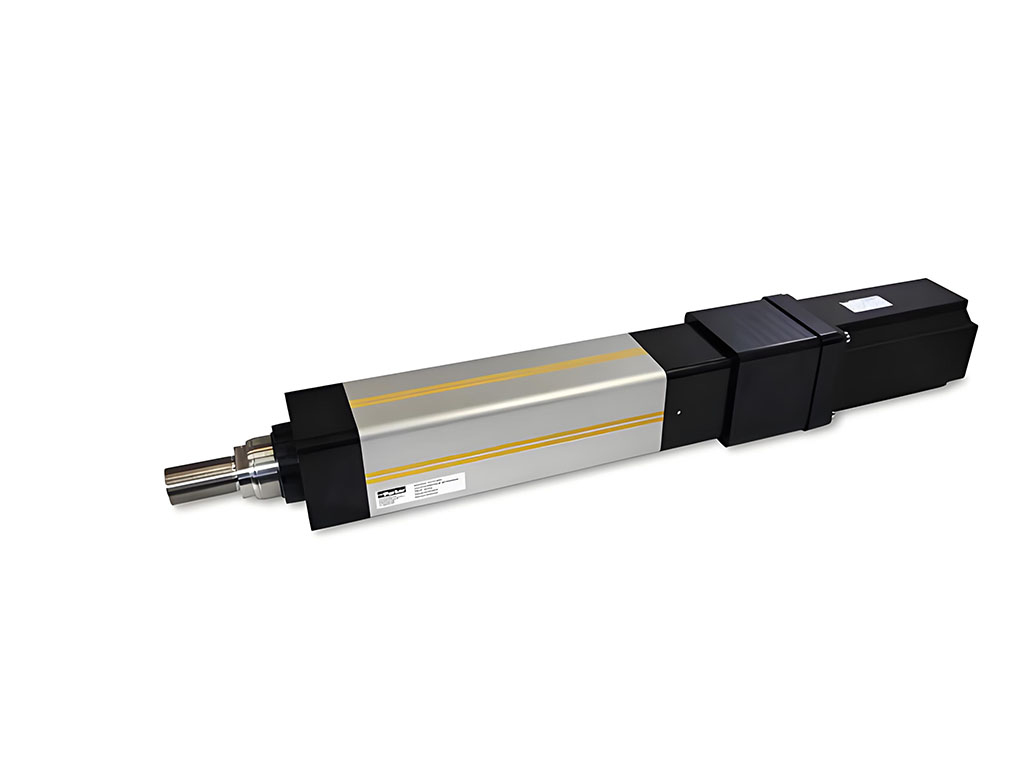
Avoiding trouble keeps your products safe and your reputation strong. Ignore standards, and you risk recalls, fines, and angry headlines.
Selecting the Optimal Food-Grade Electric Cylinder for Your Needs
To pick the right cylinder:
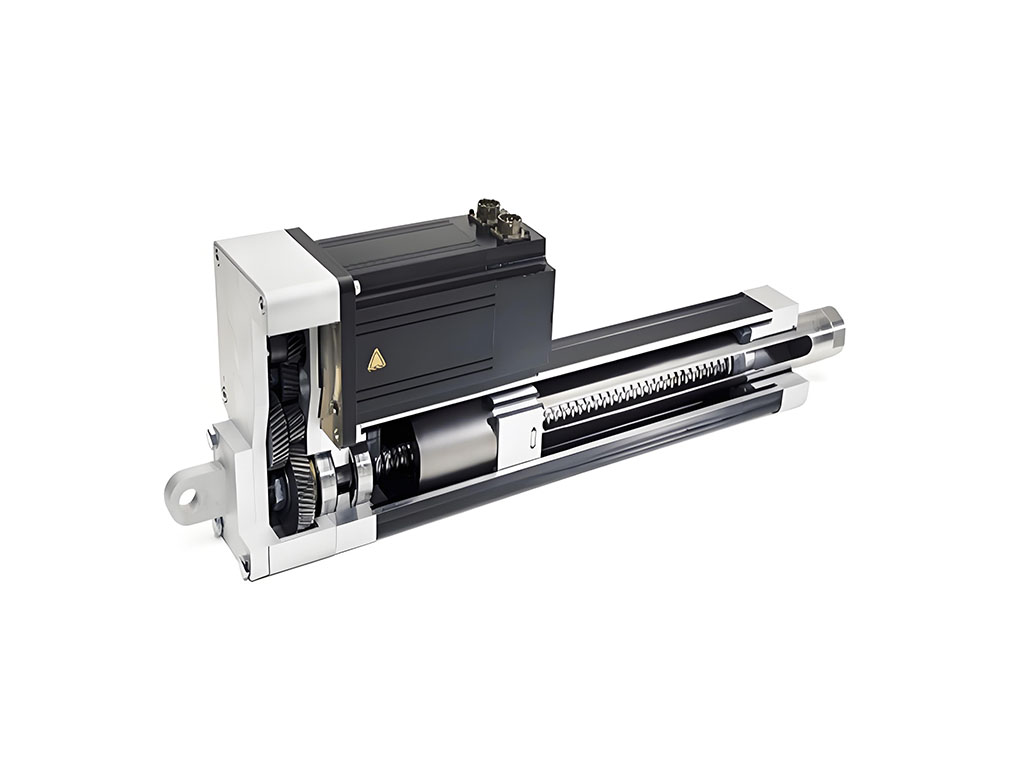
- Know your required force, speed, and how often it runs.
- Check your plant’s temperature, wetness, and chemicals.
- Make sure it's compatible with your control systems.
- Think beyond sticker price. Look at maintenance, downtime, and parts costs.
- Partner with trusted experts, not bargain-basement traders. China Electric Cylinder Factroy offers deep support and proven reliability.
A strong supplier will help you select, customize, and integrate the perfect fit.
FAQ (Frequently Asked Questions)
What is the difference between pneumatic and electric cylinders in food processing?
Pneumatic cylinders use air. Electric cylinders use motors. Electric types bring more control, lower energy use, and less maintenance.
What stainless steel is food grade?
304 and 316L are both considered food grade. 316L has better corrosion resistance, especially with salt or harsh cleaners.
Are electric actuators food safe?
If labeled "food-grade" with proper materials, seals, and certifications, yes—they’re safe for food contact.
What IP rating is required for food processing equipment?
IP69K is the gold standard. It withstands high-pressure, high-temp cleaning.
What are the benefits of electric cylinders for hygienic applications?
They don’t leak, are easy to clean, save energy, and cut downtime.
How do electric cylinders ensure cleanliness in washdown environments?
Hermetic sealing, smooth surfaces, and corrosion-proof materials keep them bacteria-free.
What is EHEDG certification and why is it important for F&B?
EHEDG checks gear for easy cleaning and germ resistance. It’s key for food safety and global trade.
How can electric cylinders reduce energy costs in food plants?
They use power only when moving. No need to run compressors all day.
What are common applications of electric cylinders in packaging lines?
Filling, sealing, pushing, sorting, and lifting—anything that moves or measures.
Where can I buy food-grade stainless steel electric cylinders?
Turn to China Linear Actuator Manufacturer or Stainless Steel Actuators for trusted products and solutions.
Conclusion & Next Steps
Food-grade stainless steel electric cylinders are changing the face of modern food automation. They keep your line clean, safe, and running at peak precision. They use less power, break down less, and clean up fast. That saves you money, keeps your products safe, and makes audits a breeze.
At Jimi Technology, we’ve spent years perfecting automation for food and drink factories. From smart design to rugged materials, our cylinders meet all the toughest standards. We’re not just a maker—we help you turn your ideas into a reality.
Ready to modernize your plant? Explore electric linear actuators and food-grade electric cylinders or contact Jimi for expert service. Future food factories run on safe, smart, energy-saving automation. Yours should too.