Imagine standing on an automotive factory floor. Robots buzz and sparks fly as metal pieces come together with a perfect hiss. In the middle of this, a small but mighty force powers each critical move: the electric cylinder. This device turns simple electric energy into a smooth, strong push or pull—making cars safer, faster, and greener than ever. What makes electric cylinders so special? Let’s dive in.
The Dawn of Precision: Why Electric Cylinders are Critical for Modern Automotive Production
An electric cylinder is a kind of linear actuator that uses electricity to move things in straight lines. Unlike old pneumatic or hydraulic cylinders, it doesn’t need air or oil. Instead, it gets its smooth, direct motion from an electric motor and a screw system inside. This clever combo creates force that’s easy to control and repeat—right down to the tiniest millimeter.
Why does this matter in car manufacturing? Cars are tough to build. They need thousands of parts put together just right, again and again. Even the smallest slip leads to mistakes or weak welds. Old systems using air (pneumatic) or oil (hydraulic) often wobble or drift. Temperature, leaks, or worn-out seals can wreck precision. Electric cylinders change the game with digital control. They respond to each command just as asked, every single time.
This is the start of a whole new way to build cars. Everything gets faster, cleaner, and more accurate. Mistakes drop. Lines run longer with less downtime. Energy use plummets. Best of all? Electric cylinders make it easy to join the world of smart factories and Industry 4.0, where machines "talk" to each other for better, safer work.
Unmatched Advantages: Transforming Automotive Welding and Assembly Operations
Precision and Repeatability: Driving Uncompromised Quality
Don’t let their small size fool you. Electric cylinders can move with stunning accuracy—down to ±0.01 mm, compared to pneumatics’ ±0.5 mm. They use servo motors and sensors called encoders. These tools measure and adjust the cylinder’s position non-stop, so every spot weld or press hit lands where it should.
What does this mean for you? Welds stay strong. Joints fit tight. Every car on the line matches the last one. If you want proof, a top carmaker using electric actuators in welding saw a 15% jump in weld consistency and 10% fewer fix-its. That's quality you can see and measure.
Energy Efficiency and Cost Savings: A Leaner Footprint
Old air and oil systems run all day, even when nothing moves. Electric cylinders? They only use power when needed. This can slash energy use by up to 80%. Not only does this cut bills, but it fits green goals too. When you run hundreds of cylinders, those savings add up—fast.
You don’t just save on energy. Electric cylinders last much longer than their rivals. No air leaks. No messy oil. Less downtime. Fewer broken parts. That adds up to a lower total cost over time.
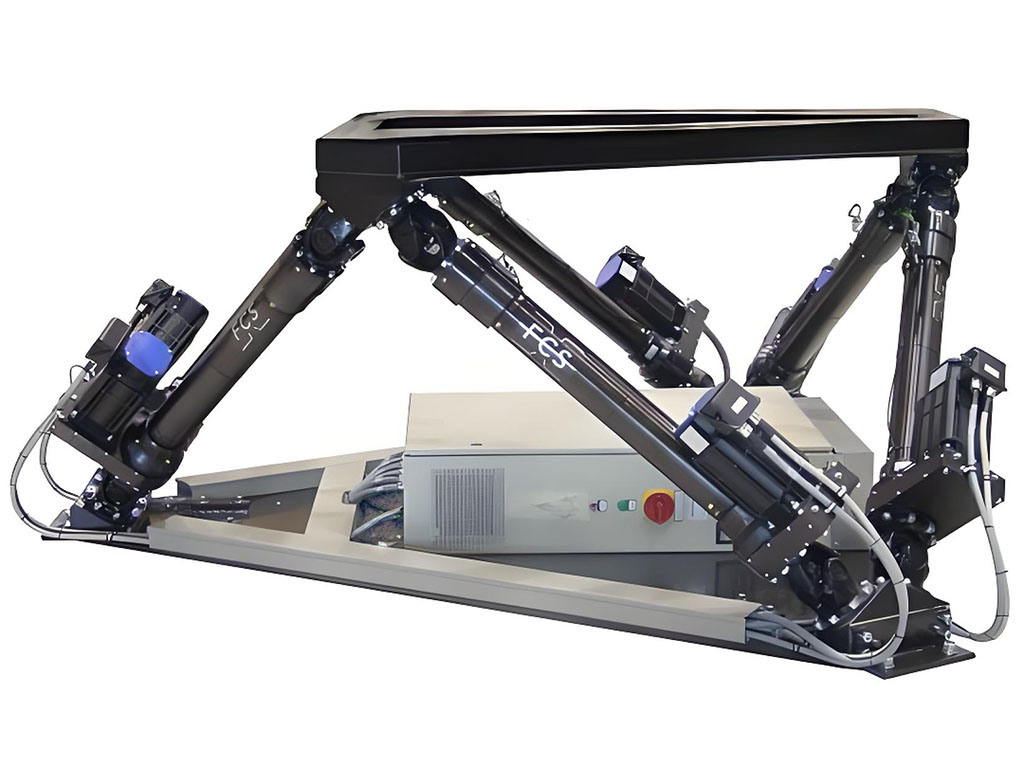
Enhanced Control and Flexibility: The Smart Factory Enabler
Need new weld patterns today? Adjusting force for a thicker door panel tomorrow? No problem. Just reprogram the electric cylinder from your main control system—no manual tweaks or tool changes needed. Electric cylinders link with PLCs and industrial robots, letting them switch tasks or check their own health. That means more cars fit your plans. Less time gets lost on setup.
Cleanliness, Noise Reduction, and Maintenance Benefits
Factories can be loud and dirty places. Pneumatic systems hiss. Hydraulics can spill. Electric cylinders run nearly silent and never leak. You get a cleaner, safer work zone for everyone. And with fewer parts needing care, maintenance stops less often.
Core Applications: Where Electric Cylinders Excel in Automotive Manufacturing
Electric Cylinders in Automotive Welding Processes
- Spot Welding: In spot welding, two sheets of metal get pinched together. You want every pinch to match. Electric cylinders keep the pressure tight and even. That means cleaner welds, less spatter, and reliable quality, shift after shift.
- Arc and Laser Welding: Laser and arc welding need perfect positioning. Electric cylinders move the tools gently for sharp, well-placed seams. Soft starts and stops help, especially with delicate metal.
- Material Handling and Clamping: Holding parts while they’re welded? Electric cylinders clamp with just the right squeeze, every time. They can swap force levels in a snap—ideal for lines making many types of cars.
Electric Cylinders in Automotive Assembly Lines
- Pressing and Joining: Installing bearings, bushings, or gears means pushing them in at set pressures. Electric cylinders control that force exactly, so nothing cracks or jams.
- Riveting and Fastening: Robots using electric cylinders can set fasteners at just the right depth and speed. No bolts stripped. No loose joints.
- Clamping and Gripping: Need to grip different-sized doors or hoods? Electric cylinders adjust in real time.
- Testing and Inspection: For quality checks, control is everything. Electric cylinders help measure and test each part, moving with a gentle touch.
Technical Deep Dive: Selecting and Integrating Electric Cylinders
Every job has its match. When you pick an electric cylinder, think about:
- Force: How much push or pull do you need?
- Speed: How fast should it move?
- Stroke Length: How far does it travel?
- Duty Cycle: Does it run all day or just sometimes?
- Environment: Is it dusty, hot, or vibrating?
Let’s not forget sensors and servo drives. These keep the cylinder in perfect sync with your main controls, whether it’s using EtherCAT or PROFINET. Need to retrofit? No sweat! Our cylinders fit with existing PLCs and networks.
Table: Core Parameters to Consider
Specification | Typical Range | Jimi Electric Cylinder Advantage |
---|---|---|
Force | 100N – 30,000N | Wide range, high peak force |
Accuracy | ±0.01mm or better | Top-level precision |
Speed | 10mm/s – 1500mm/s | Fast, adjustable, consistent |
Duty Cycle | 10% – 100% | Full industrial uptime supported |
Environment | -20°C to +60°C, IP65+ | Rugged, sealed, dustproof models |
Explore more: Electric Cylinders
High Force Servo Linear Actuator | Custom OEM
Electric vs. Traditional Actuation: A Comprehensive Comparison
Feature | Electric Cylinder | Pneumatic Cylinder | Hydraulic Cylinder |
---|---|---|---|
Precision | ±0.01mm | ±0.1-0.5mm | ±0.05-0.2mm |
Energy Use | Only on demand | Air leaks, always on | Oil pumps always on |
Setup | Simple, digital | Tubing, air lines | Pipes, storage tanks |
Maintenance | Low (electric drive, few moving parts) | High (leaks, seals) | High (oil, seals) |
Noise | Low | High | Medium |
Cleanliness | No spills or hiss | Air leaks | Oil leaks |
Integration | Digital, direct to PLC | Needs valves | Needs valves |
Each system has its place. But if you need top precision and want to save energy in tough factory settings, electric cylinders get the edge. For some ultra-heavy jobs, hydraulics still have a spot, but they trail behind in speed, safety, and control.
The Road Ahead: Challenges and Future Innovations
Switching to electric can cost more up front, but don’t panic! Studies show you may spend less over time because of energy savings, longer life, and fewer repairs. With sensors and smart networks, you can even spot problems before they cause downtime.
What’s next? Electric cylinders are getting smaller, stronger, and even smarter. Soon, they’ll help enable “lights out” manufacturing where robots run factories at night. With predictive maintenance and more data, you’ll know exactly when to swap parts or update settings.
FAQ
Q: What are the main advantages of electric cylinders over hydraulic or pneumatic cylinders in automotive manufacturing?
A: Electric cylinders offer better precision, less energy use, longer life, and cleaner, quieter work.
Q: How do electric cylinders improve precision and quality in spot welding applications?
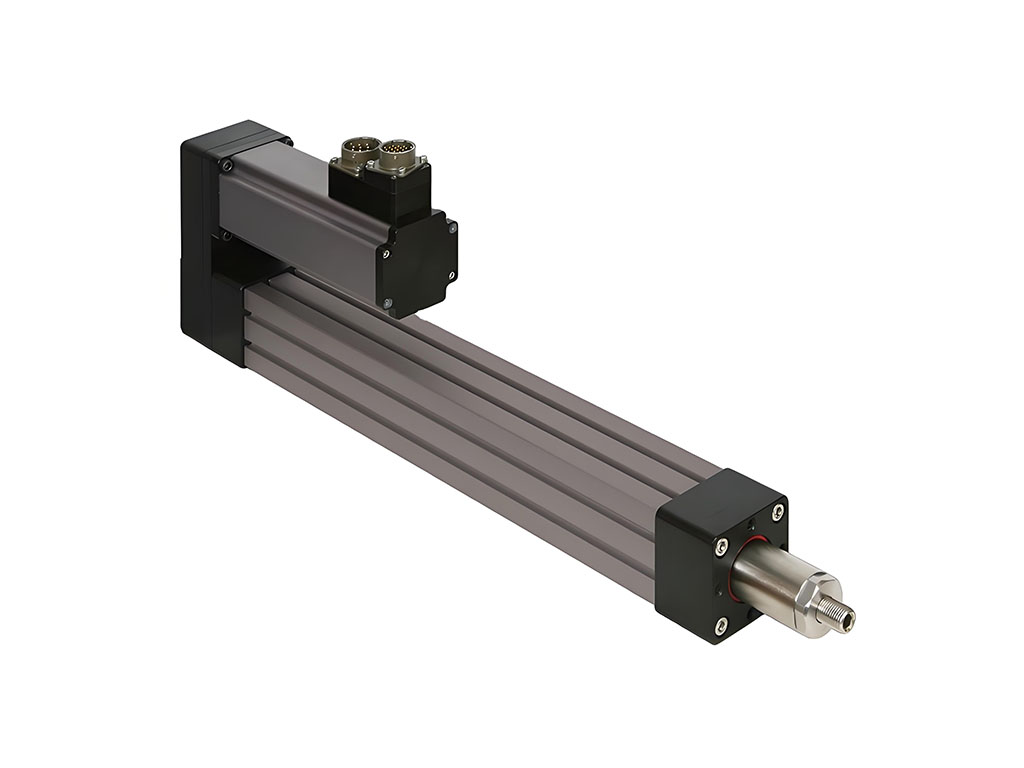
A: They deliver exact, repeatable force on each weld, reducing errors and increasing consistency.
Q: Can electric cylinders handle the high forces required for automotive assembly processes like pressing?
A: Yes. Our models like the 250 Series 30T Servo Linear Actuator push up to 30,000N or more.
Q: Are electric cylinders more energy-efficient than pneumatic systems?
A: Yes. Electric models use power only when moving, with savings up to 80%.
Q: Which assembly operations benefit most from electric cylinders?
A: Pressing, riveting, testing, clamping—any process that needs speed and precision.
Q: How do electric cylinders connect with modern factory systems?
A: They use industrial networks like EtherCAT or PROFINET for instant data sharing and control.
Q: What about maintenance and lifespan?
A: Our cylinders can last 5–10 times longer than air systems, with less frequent service.
Q: What is the ROI for switching to electric cylinders in an automotive plant?
A: Lower energy costs, fewer repairs, and less downtime mean payback in just a few years.
Q: How do electric cylinders support smart manufacturing?
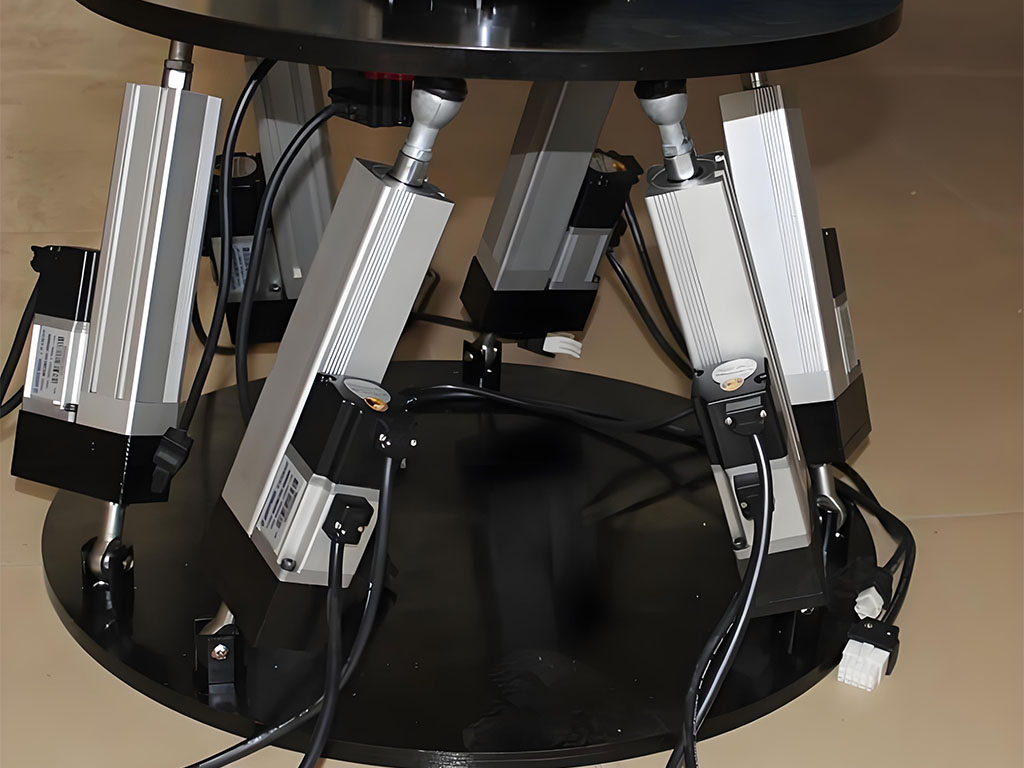
A: Their sensors let you track performance and predict failures, fitting right into Industry 4.0 plans.
Q: What’s most important when picking a cylinder for your line?
A: Match force, speed, and environment needs, and check integration with your control system.
Conclusion & Next Steps
Electric cylinders stand at the heart of modern automotive manufacturing. They lift, push, pull, and clamp—quietly and precisely—every day. Over time, they help you build better cars, use less power, cut costs, and reach greener targets.
Ready to make your factory smarter, faster, and more reliable? At Jimi Technology, we bring years of expertise, world-class products, and hands-on support for every project. We aren't just a supplier; we’re your automation solution partner. From robust servo linear actuators, electric cylinders, to smart controllers—let’s unlock new ideas together.
Start today. Talk with our experts or see how others have transformed their lines. We’ll help your team move towards the future with confidence.