Choosing the Right Linear Motion Platform for Automation: A Comprehensive Engineering Guide
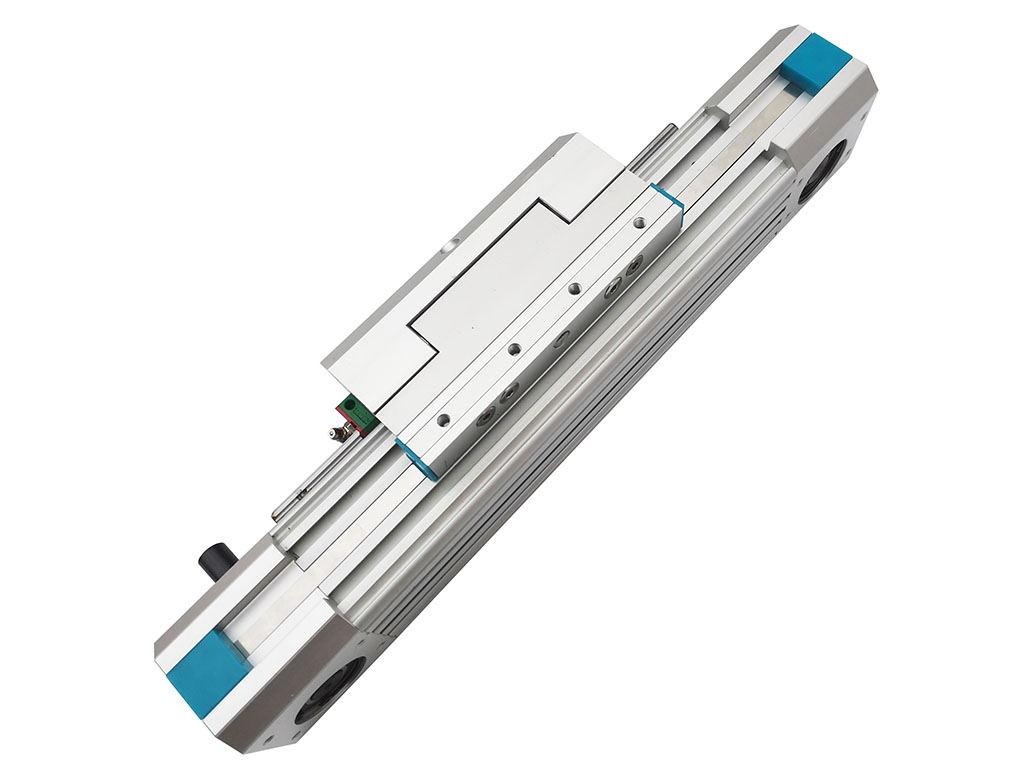
Every engineer faces a major headache at some point—choosing the right linear motion system for automation. Maybe you have a new assembly line coming online, or your packaging line keeps stalling. Perhaps your cleanroom equipment needs an upgrade before a new regulation hits. The cost of a bad decision looms large. The stakes are high: your selection will impact not just how well machines run, but how often they break, how much time you waste on repairs, and how much money your company loses when things go off the rails.
Have you ever watched your machine slow to a crawl or shivered at the sound of a motor grinding away? Maybe you’ve seen product piles up in a corner because the actuator failed again—or met a customer unhappy with the repeatability of your dispensing line. It’s frustrating. The downtime eats into your output. Maintenance eats into your budget. Your boss just wants it fixed. You want stability, speed, and peace of mind.
Worse, if you pick the wrong linear motion platform, you could lock your team into years of inefficiency and rising costs. Downtime can eat up to 25% of total production hours according to recent surveys. Each hour lost means profit slipping through your fingers. Maintenance calls get more frequent, and parts wear out before you expect. Suddenly, your automation investment looks more like a money pit. There’s a better way.
What exactly is a linear motion platform? It’s the backbone of every automated movement. From electric linear actuators to advanced linear motors, these systems turn rotary or electrical energy into smooth, controlled straight-line motion. Robots for pick and place, CNC machines, conveyor belts, automated dispensers—all of these depend on the right linear platform. You can’t achieve precision, speed, or reliability without the right choice.
But how do you sort through ball screws, belt drives, pneumatic cylinders, and linear motors? How do you know which works for your workload? The answer impacts your total cost of ownership and your uptime performance.
At Jimi Technology, we have spent years helping companies like yours solve exactly this problem. We guide engineers to the best-fit solution for every application—from harsh manufacturing floors to pristine pharmaceutical cleanrooms. Let’s break it all down.
I. Understanding the Impact—Why Platform Choice Decides Everything
A linear motion platform isn’t just another component. It’s the heartbeat of your automation system. Select the wrong one and you risk poor throughput, limited accuracy, and rising costs. Get it right and you’ll boost quality, save energy, and keep your machines humming with fewer headaches. That goes straight to your bottom line.
- Performance: The right platform means you meet repeatability targets—down to ±5µm for high-precision tasks, or get the speeds you need for rapid pick & place (think up to 10 m/s on modern, high-speed belt-driven actuators).
- Total Cost of Ownership (TCO): Don’t just look at the initial price. Remember, energy use, routine maintenance, and parts replacement add up fast. A pneumatic cylinder that’s cheap upfront might waste 40% more energy than an electric alternative long term.
- Uptime & Reliability: Choose poorly and unscheduled breakdowns creep in, costing as much as $260,000 per hour in lost big-factory output according to some industry sources. Downtime wrecks production schedules.
II. Core Criteria—How to Match the Platform to Your Task
Let’s keep it simple and personal. Here are the nuts and bolts you need to get right:
- Precision & Accuracy
- Repeatability: Can the platform come back to the exact same point each time? Ball screw-driven actuators shine with ±5µm; ordinary belt drives give you ±200µm.
- Absolute accuracy: Is the actual position what your controls say it is? Look for solutions with integrated encoders like Actuators with Position Feedback.
- Speed & Acceleration
- Need blistering speed? Belt-driven (up to 10 m/s) or linear motors (up to 15 m/s+) win the race. For assembly automation, nothing slows a line like a sluggish axis.
- Load Capacity & System Stiffness
- Heavy tool? High moment loads? Choose solutions like ball screws or rack and pinion for robust handling. Belt drives suit lighter, rapid moves.
- Avoid “banana syndrome”—where flexible or poorly supported actuators deflect and kill your accuracy.
- Stroke Length & Travel Range
- Only need short motion? Pneumatic or hydraulic cylinders do the trick. Need long travel (over 6m)? Belt or rack-and-pinion actuators work best.
- Duty Cycle & Life Span
- Is your process non-stop? Pick hearty systems with proven operational life in millions of cycles. Don’t let your actuator retire early!
- Environmental Factors
- Working in the food industry, beverage, or pharma? Cleanroom requirements might dictate sealed, lubrication-free, or non-contact solutions like linear motors.
- Hot, cold, wet, or dusty? Rugged, sealed profiles or industrial linear actuators are your friends. See our range at Industrial Linear Actuators.
III. A Tour of the Top Linear Motion Platform Types
Here’s what you need to know about the main players and where they shine. Pick your favorites, but know their limits.
Ball Screw Driven Systems
- Strengths: High accuracy, tough rigidity, great efficiency.
- Drawbacks: Critical speed limits exist (go above and you shake and rattle), not cheap for ultra-long strokes.
- Best for: CNC machines, medical device assembly, test & measurement.
Belt-Driven Actuators
- Strengths: Fast, quiet, long travel lengths, affordable for big projects.
- Drawbacks: Not as precise as ball screws, belts stretch over time (plan for tensioning!).
- Best for: Quick pick & place, moving boxes, packaging, big printers.
- Take a look at High-Speed Linear Actuators if speed sets the pace for your line.
Linear Motor Systems
- Strengths: No friction, crazy speed, ultra-precise (±1µm repeatability), whisper-quiet.
- Drawbacks: High sticker price, needs expert tuning, heat build-up possible.
- Best for: Semiconductor lines, inspection systems, laser cutting.
Pneumatic & Hydraulic Cylinders
- Strengths: Move big loads, simple, cheap upfront, thrive in hostile environments.
- Drawbacks: Not precise, can waste energy (air escapes, fluids compress), messy if leaking.
- Best for: Push/pull jobs, clamps, big gates, heavy lifting.
Rack & Pinion Systems
- Strengths: Stroke lengths only limited by your shop size, lots of force, solid rigidity.
- Drawbacks: Some backlash, can’t match linear motors’ precision.
- Best for: Large gantry robots, heavy-duty transfer lines.
IV. Installation, Integration & Ongoing Management
You have your platform, now milk every advantage.
- Mounting & Alignment: Even the best gear fails if mounted poorly. A little care now saves mountains of pain later!
- Control System Compatibility: Will it “talk” seamlessly with your PLC or motion controller? Make sure. Check out Actuator Controllers for easy integration tips.
- Operating Cost & Energy Efficiency: Modern electrics save 30-50% energy versus old pneumatics. Think ahead for green wins.
- Routine Care: Plan for lubrication, seal checks, and routine inspections. A little grease beats a costly breakdown.
- Safety & Compliance: Are you legal? ISO standards and CE/UL marks matter for risk and insurance.
V. Real-World Lessons: Results You Can Expect
Need proof? Here’s how smart choices pay off in the wild:
Semiconductor Cleanrooms
A wafer fab swapped out aging ball screws for direct-drive linear motors. Wafer throughput shot up 30%. Fewer particles, fewer failures. Zero complaints about noise. Linear motors cost more up front but delivered massive, sustained uptime and 50% fewer quality problems. For high-stakes environments, they’re gold.
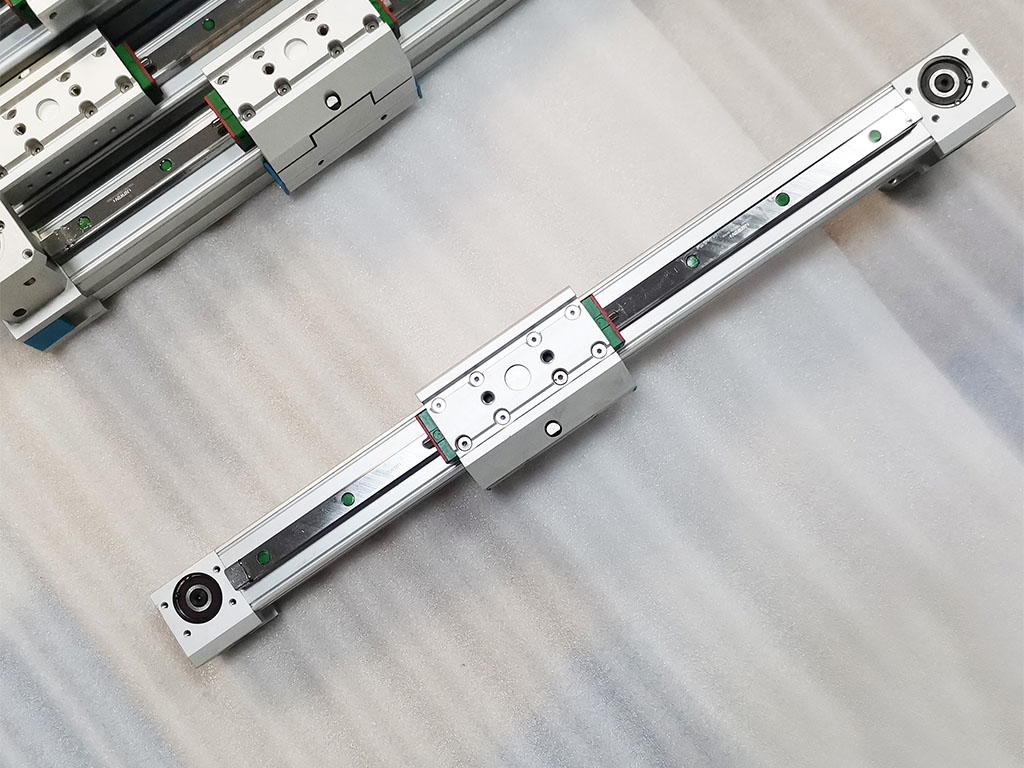
Packaging Lines
A major food packager replaced noisy air cylinders with fast belt actuators and servo controls. The result? 25% more packages per hour and 40% lower energy bills. Workers stopped wearing ear protection. Maintenance managers stopped sweating actuator failures.
Medical Device Precision
Ball screw-driven actuators with feedback sensors let a medical device maker cut reagent waste by 15% and increase perfect runs by 10%. That repeatability meant more quality, less scrap, and happier clients.
Market numbers back up these stories: the linear motion systems market is racing ahead at a 6-8% yearly growth rate. Companies that pick smart platforms see real ROI. Failures in motion systems can cause 20-25% of automated downtime, and today, energy costs for poor choices are higher than ever.
VI. Your Selection Checklist—Don’t Miss a Step
Stay out of trouble and follow this battle-tested approach:
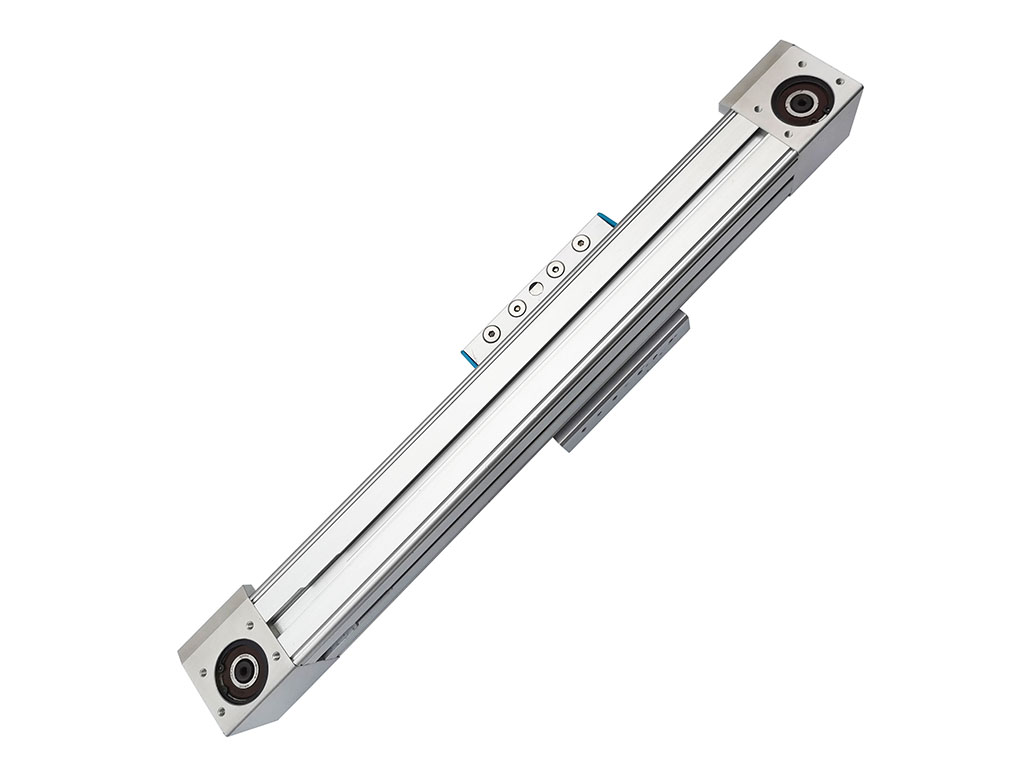
- List your specs: How precise, how fast, how heavy, how far, how often will you run?
- Map your environment: Dust, water, extreme heat, cleanroom? Choose accordingly.
- Compare the platforms: Weigh up ball screw, belt, linear motor, pneumatic, or rack and pinion—pros and cons versus your needs.
- Budget smartly: Don’t be fooled by upfront price. Look at lifetime costs, including downtime, maintenance, and energy.
- Review supplier support: Get tech help, training, and strong after-sales service. The right partner makes your life 10x easier.
- Prototype: Not sure? Test a sample unit before full rollout.
VII. Why Jimi Technology Makes Your Job Easier
We at Jimi don’t just ship boxes. As a top China Linear Actuator Manufacturer, we work hand-in-glove with clients. Our team has helped hundreds of factories, labs, and OEMs pick and install the ideal platform for their needs. Quality isn’t just a word—it’s built into our heavy-duty, miniature, and custom linear motion solutions.
- Need custom travel, load, or IP rating? We design to fit.
- Want a platform that survives harsh washdowns or delicate cleanrooms? We’ve got you covered.
- Require fast, expert support from engineers, not sales reps? Our experience ensures you get answers and results, fast.
Internal Resources
- Looking for tough, durable options? Browse our Industrial Linear Actuators.
- Need a solution for fast, light-duty applications? Check out Light-Duty / Miniature Actuators.
- Want precise positioning for advanced robotics? Discover Servo Motor Actuators and Ball Screw Actuators.
Conclusion—Move Smart, Stay Ahead
Choosing the right linear motion platform can feel overwhelming. But you don’t have to risk your project or your budget. With a clear checklist, honest performance comparisons, and an experienced partner like Jimi, you can automate boldly, slash downtime, and achieve results that push you ahead in your industry. Want to start on the right path? Reach out to our experts, share your automation challenge, and together, let’s build your next triumph.
Ready to take your automation from ordinary to extraordinary? Get in touch now—let’s put your motion challenges in the past and your project’s future in motion.