Introduction: Why Actuators Matter
Imagine a plane flying high in the sky. When it needs to land, it drops its landing gear like strong legs. When it takes off or slows down, it moves special flaps on its wings. How does it do this? With actuators!
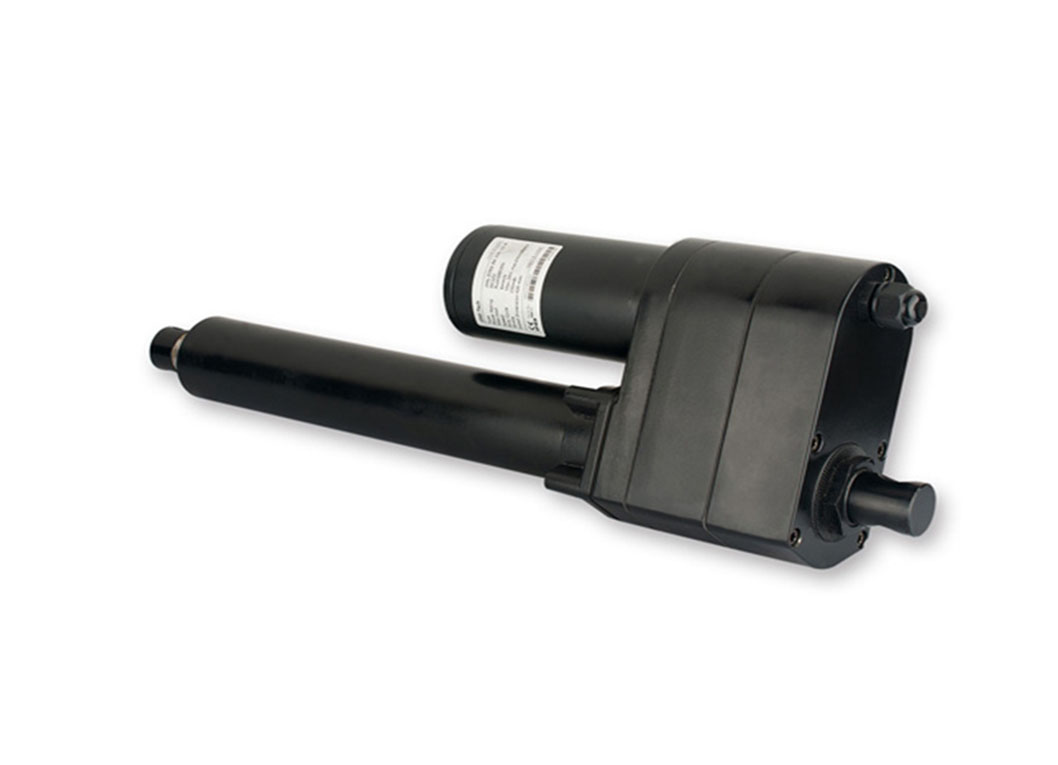
Actuators are the strong arms and legs of an airplane. They help raise the flaps and move the landing gear. If these parts do not work, the plane cannot fly safely.
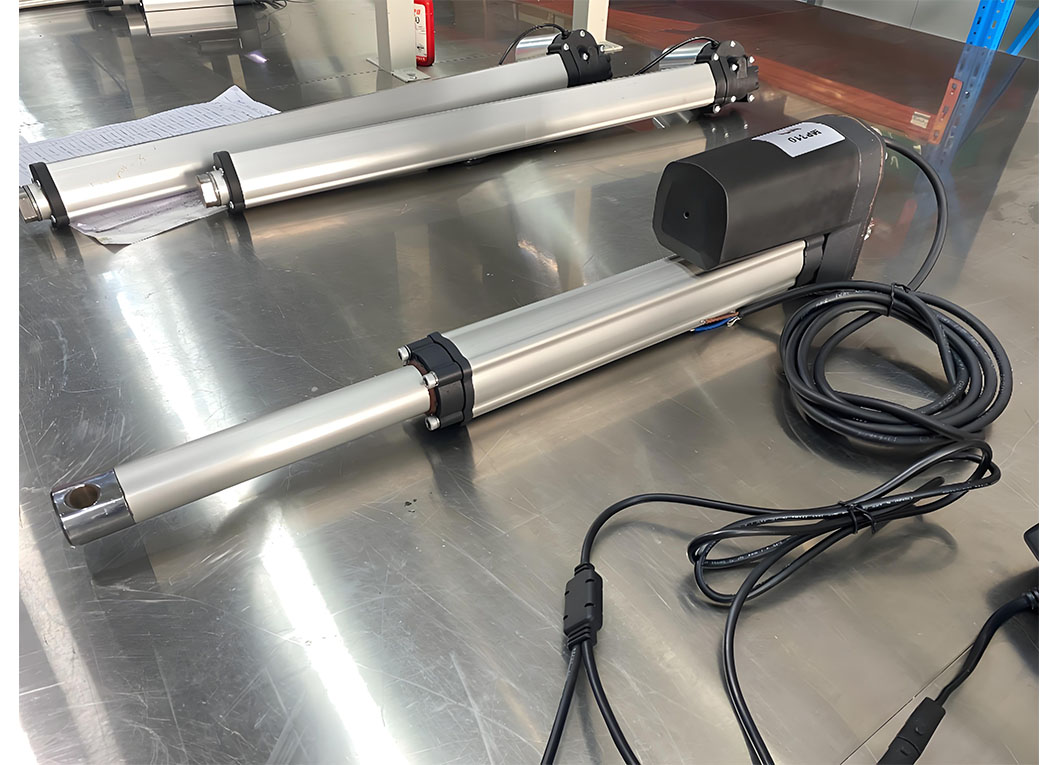
Testing each actuator is very important. At Jimi Technology Co., Ltd., we are experts in making and testing these smart parts. We make sure everything works right, every time.
What Kinds of Actuators Work in Planes?
Not all actuators are the same. Let’s look at some types:
- Hydraulic Actuators
- They use liquid to move.
- They are great for big jobs, like heavy landing gear.
- Electromechanical Actuators (EMA)
- These use electricity and gears.
- They are smart, use less space, and are used for flap system actuator validation.
- They work well in More Electric Aircraft (MEA).
- Electro-Hydrostatic Actuators (EHA)
- A mix of both: uses electric controls with fluid strength.
- Great for new, safe airplane designs needing redundancy testing.
At Jimi, we make all these types smart and strong!
Why We Test Actuators
Planes must be safe. If an actuator fails, the landing gear might get stuck. The flaps might not move. That’s bad for everyone.
Testing makes sure:
- Safety: Nothing fails, no matter what.
- Performance: The part moves fast and smooth.
- Long Life: Fine even after many, many uses.
- Meets Standards: Passes rules from FAA, EASA, RTCA DO-160, MIL-STD-810.
- Saves Money: The fewer faults, the lower the cost.
Here’s a quick chart:
Need | Why It Matters |
---|---|
Actuator reliability | Keeps people safe |
Durability & cycle life | Flaps/gear work year after year |
Regulatory compliance | Pass strict tests by FAA & EASA |
Cost savings | Stop surprise breakdowns, cut repair costs |
Fast validation | Planes built and ready quicker |
How Do We Test Actuators?
Testing is like a big, fun science project—but for planes! Here’s what the pros do:
- Performance Testing
- Load and force: Pull, push, and see how strong it is.
- Speed: How fast does it move?
- Sensors: Use LVDT and RVDT to see where and how the actuator moves.
- Power: Measure its energy use.
- Durability & Life Cycle Testing
- Run it again and again, thousands of cycles!
- Copy takeoff and landing movements.
- Catch problems early.
- Environmental Testing
- Put it in very cold and very hot chambers (from -55°C to +85°C!).
- Shake it with big vibration machines.
- Spray it with fog, dust, or even salty mist.
- Test for EMI/EMC, to avoid electric problems.
- Functional & Failure Mode Testing
- What happens if power stops? Or if liquid leaks?
- Actress like a “bad day.” Prove nothing can make the actuator fail.
- Acceptance & Production Testing
- Every actuator gets checked before it leaves the factory!
- Use data acquisition systems (DAS) to track everything.
Our team at China Linear Actuator Manufacturer does all these steps. We use smart benches, strong computers, and clever software.
Tools We Use for Best Results
At Jimi, we use the top tools for all aerospace actuator jobs:
- Test Benches: Strong stands for real world checks.
- Environmental Chambers: Hot, cold, shake, and spray.
- Servo Controls & PLCs: Smart brains for control.
- Test Rigs & Sensors: Include load cells, accelerometers, pressure transducers.
- Data Systems: Fast computers record every movement.
- Modeling Software: Like MATLAB/Simulink, Ansys, and Dassault Systèmes.
We build, test, and check—so you fly safe.
Testing By The Numbers
Let’s see some facts from the aerospace world to show why tough testing is key:
Metric | Data/Value | Why It Matters |
---|---|---|
Market growth | $9.5B to $13.2B by 2030 | More planes, more testing! |
Big landing gear cycles tested | 60,000 – 80,000 cycles | Far more than real flights |
EMA in new aircraft | 50%-70% of flap systems | Changing face of technology |
Actuator failure cost | $10,000 – $150,000 per hour (AOG time) | Testing avoids high bills |
Environmental testing required | Over 90% actuators tested to RTCA DO-160 | Must pass vibration, heat, EMI tests |
Data from one big test campaign | Terabytes of data | Smart software needed |
Maintenance savings (PHM used) | Up to 30% fewer surprises | Predict before problems start |
Source: Airbus, Boeing, Collins Aerospace, RTCA, MTS Systems, and more.
Are There Rules? Yes! Many Rules.
Aerospace is a serious business. We follow the best standards and rules:
Regulators & Standards We Meet:
- FAA (Federal Aviation Administration)
- EASA (European Union Aviation Safety Agency)
- RTCA DO-160
- MIL-STD-810
- AS9100 (top quality badge)
- Nadcap (accreditation for big jobs)
- SAE Aerospace Standards
- AIA (Aerospace Industry Association)
We tick all the boxes for type certification, TSO, PMA, and more. Safety first, always.
The Big Problems—and Our Solutions
It’s not always easy to keep up. Planes get smarter, systems more connected. Actuators must be smarter, too.
Some challenges:
- Smart actuators need smarter tests.
- Electric planes use electromotor actuators instead of hydraulic ones.
- More data needs better computers.
- Green testing—less waste, more saving.
- Testing must be quicker for new airplanes.
We keep up by building better actuators, using digital twins, and offering predictive maintenance. At Electric Linear Actuators, our engineers work with Collins Aerospace, Safran S.A., Moog Inc., and other big names. We know aerospace actuator testing inside out.
Why Trust Jimi? Here’s Why.
We are not just a seller. We are experts, teachers, and partners for your projects. We test every actuator for the longest life, strongest safety, and highest performance.
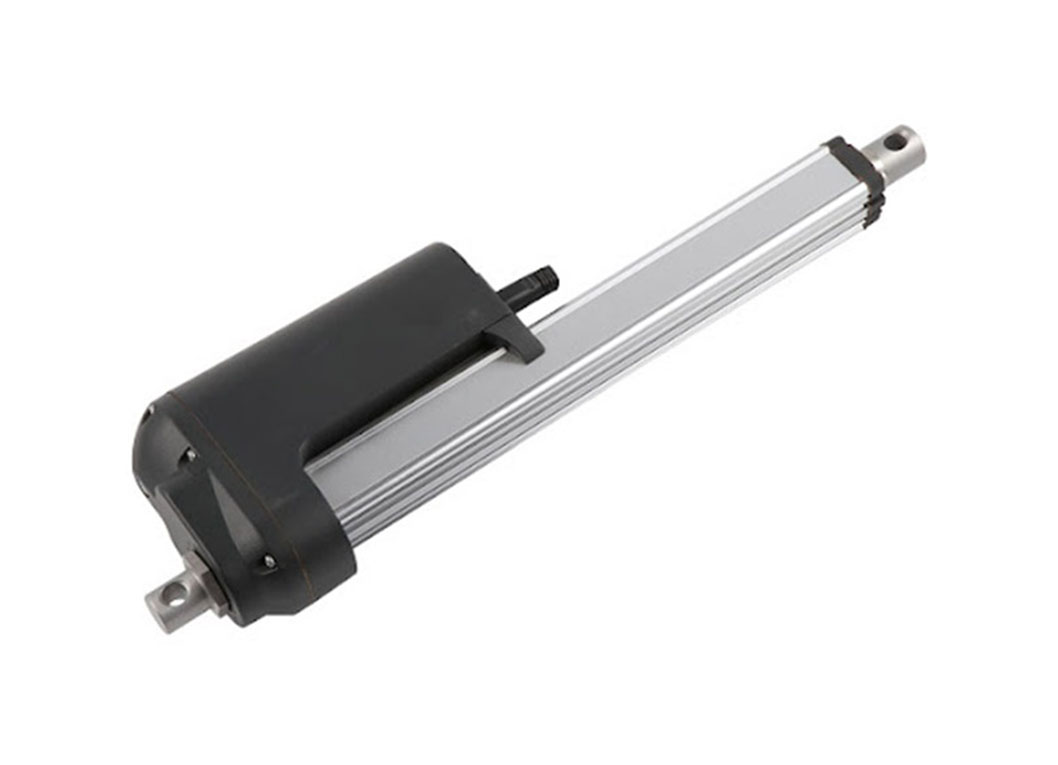
Our team is trusted by top names: Airbus, Boeing, Safran, Honeywell Aerospace, and more. We use all top standards and deliver full test data reports. When you ask for testing—hydraulic, electromechanical, or EHA—we deliver.
Find the best actuator for flights, robotics, or heavy machines. See our Servo Motor Actuators and Industrial Linear Actuators.
The Takeaway
Actuators are the muscles of an airplane. If they work right, everyone stays safe. If they are tested the right way, they last long and save money.
At Jimi, we test every actuator for:
- Safety
- Strength
- Speed
- Standards
- Satisfaction
Want to see more? Visit China Electric Cylinder Factroy, or ask about custom tests today.
References
- MarketsandMarkets: “Aerospace Actuators Market – Global Forecast to 2030”
- Airbus “A350 Systems Overview”
- SAE ARP 5716
- RTCA DO-160
- MTS Systems
Choose Jimi. Make flying safer. Make machines smarter.