Introduction: The Critical Role of Linear Guides in Tire Manufacturing
Walk into any tire factory. Everywhere you look, tire machines lift, press, and shape tough rubber into tires we all depend on. Now, imagine all those heavy parts gliding back and forth, thousands of times each day. That smooth, strong movement? It all comes down to one thing—high-load linear guides. They are the backbone of tire production. But what happens when these guides struggle against heavy loads, soaring heat, dust, or constant vibration?
Picture a busy production line. Workers scramble to keep up. Suddenly a tire press grinds to a halt. Why? A worn-out linear guide stalls under the burden, sending downtime—and costs—soaring. This is a problem that hits hard and fast. Missed delivery deadlines, ruined batches, and the headache of emergency repairs pile up.
These production pains aren’t rare. In fact, bad guides in high-load environments like tire factories mean the difference between smooth sailing and constant firefighting. When a single linear guide fails, it can spell hours of lost output and thousands in extra expense. Worse still, loose or uneven guides ruin part alignment, so you get more faulty tires and wasted materials. The frustration bubbles up—mechanics curse yet another breakdown, managers fret about wasted time, and customers wonder why orders got pushed back, again.
But all this doesn’t have to be your story.
Understanding High-Load Linear Guides: Types & Critical Characteristics
So, what does “high-load” really mean? In the world of linear motion systems, “high-load” means guides built to handle punishing weights, harsh shocks, and nonstop running—in other words, exactly what tire machines demand. Ordinary linear rails might get by in light-duty machines. However, tire presses, building machines, and curing units call for heavy-duty linear motion systems built to thrive where most components fail.
Key types of linear guides for heavy-duty use:
- Profile Rail Guides (Ball vs. Roller Type):
Ball type rails use ball bearings for smooth travel but top out at moderate loads. Roller type rails swap those balls for tough rollers, boosting strength and rigidity for true high-load performance.
- Heavy-Duty Recirculating Ball and Roller Bearings:
Designed for major presses and molds, these deliver robust support without sagging or stuttering under weight.
- Precision Linear Slides and Gantry Systems:
Perfect for accurate part placement, especially critical where small misalignments mean rejected tires.
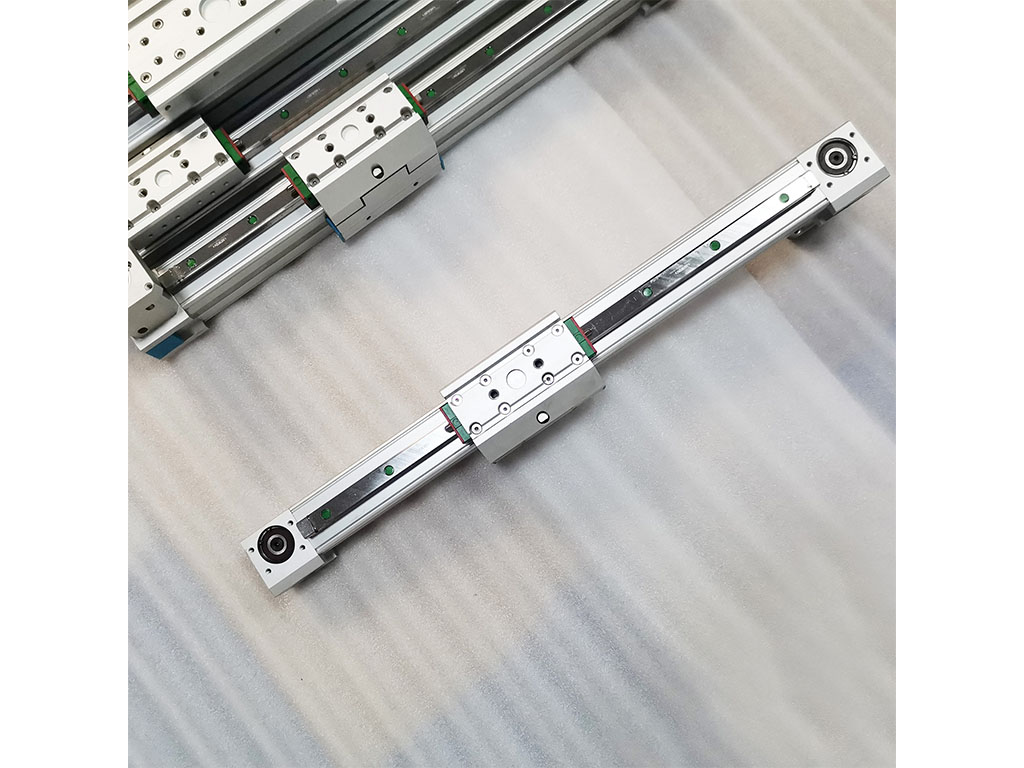
- Crossed Roller Bearings:
Take it up a notch. These provide extreme precision and rigidity for demanding testing and inspection stations.
All top tire machines must weigh these essential performance features:
- Static and Dynamic Load Capacity:
How much unwavering weight can a guide hold? How much force can it safely move, again and again?
- Stiffness and Vibration Damping:
A stiff guide keeps presses and platens from wiggling—critical for tire shaping. Good vibration damping means machines run smoother, longer.
- Positional Accuracy and Repeatability:
Even tiny slips can wreck tire uniformity. High-grade guides guarantee perfect placement every time.
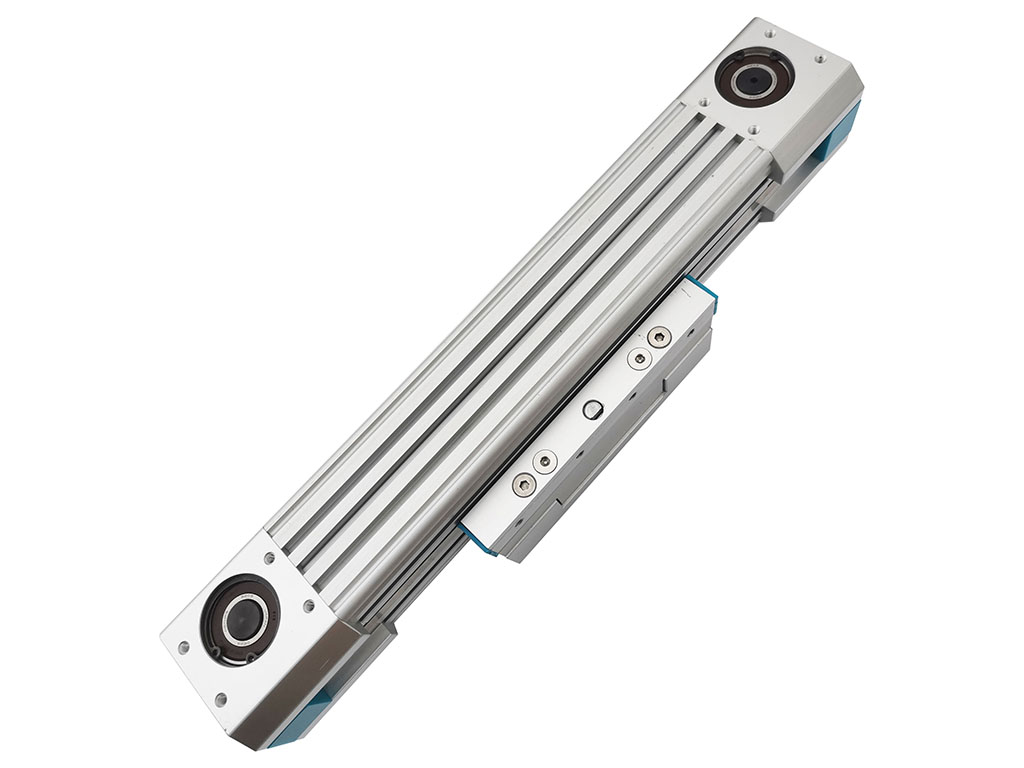
- Speed and Acceleration:
Strong guides let you work faster, not just heavier—raising productivity without risking damage.
- Service Life and Durability:
Better guides mean less downtime. Instead of changing rails every two years, advanced options last five, seven, even more years with the right care.
Application-Specific Needs: Where High-Load Guides Excel in Tire Machines
Tire Building Machines: Here accuracy counts. Components must line up perfectly for every layer—rubber, bead, and inner liner. High-load guides ensure each move is crisp and repeatable, holding heavy platens in lockstep so every tire emerges flawless.
Curing Presses: In the tire’s last forming step, gigantic molds and steel platens move in and out, sometimes dozens of times per hour, in wicked heat. Here, only robust, heat-resistant guides stand a chance.
Tire Uniformity & Testing Machines: Every tire gets tested for balance and strength. High-precision guides let heavy test drums squeeze and spin tires under tight tolerances, delivering reliable data for safety and performance.
Automated Material Handling & Robotics: Modern tire plants rely on robots to move unfinished tires (the “green tire”) from station to station. Sturdy linear rails keep these robots accurate—no missed pickups or dropped parts.
Assembly Lines and Inspection: Everywhere parts move, or cameras scan, linear guides make the journey smooth. Even light loads benefit from the durability and positioning only high-load designs can deliver.
Selecting the Right High-Load Linear Guide: Key Considerations for Optimal Performance
Can you simply swap in any heavy-duty guide and call it a day? No way. Every tire machine tells a different story, and picking the perfect guide means looking at every angle:
- Machine Requirements:
What loads will the guide see? How fast must it go, and for how long each day? Track duty cycle and temperature range.
- Materials and Coatings:
Dust, chemicals, and water are everywhere in a tire plant. Stainless steel or coated guides resist rust and corrosion.
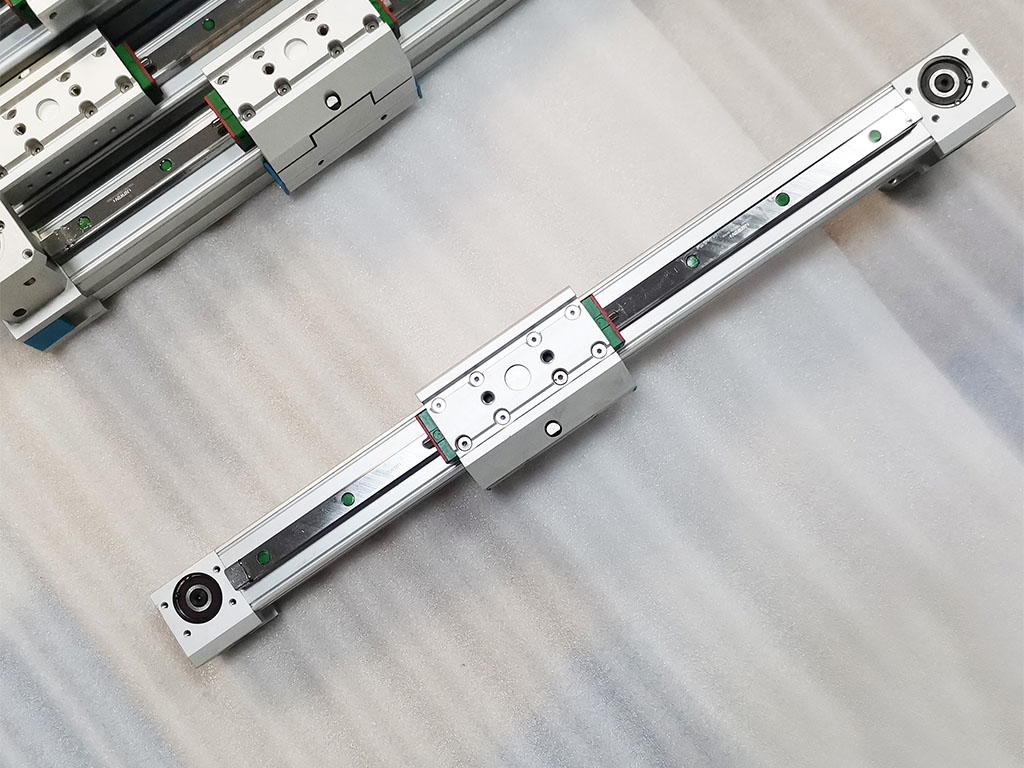
- Sealing & Protection:
Good end seals and wipers shield against rubber dust, keeping rails clean and running smooth.
- Lubrication:
Manual lubrication eats labor time. Automatic or self-lubricating units cut maintenance hours way down.
- Mounting, Alignment & Preload:
Install guides with care. Tiny mounting errors grind guides down early and kill accuracy. Preload settings fight lash and slack, especially important for high-speed applications.
- Supplier Expertise:
Not all brands are equal. Top suppliers like Jimi provide not just products but full support, from specification to custom solutions.
- Total Cost of Ownership:
Don’t just chase the lowest price. Ask: how long before replacement? How much downtime? How much labor in lube and alignment every month?
Let’s take a real-world example. A global tire manufacturer ran into nonstop headaches: their presses went down more times than they could count, losing over 15 hours per month to guide failures. Switching to heavy-duty roller-type guides with auto-lubrication cut downtime by 70%. The guides lasted years, not months, and scrap rates fell by half a percent—a boost worth its weight in gold.
Installation, Maintenance, and Troubleshooting for Maximizing Uptime
Getting the best from high-load guides is all about care, from day one.
Best Practices for Setup:
- Precision Installation:
Always check guide flatness and alignment. Tiny errors here balloon into crooked presses and rapid wear.
- Routine Maintenance:
Establish clear lubrication schedules. With automated systems, you can move from weekly grease-ups to quarterly ones.
- Inspections:
Listen for odd noises, check for loose bolts, and watch for extra play in movement. Early catch means quick fix.
Common Issues and Fixes:
- Wear:
Pitted or scored rails? Bad lubrication or wrong preload might be the issue.
- Misalignment:
If you see uneven movement or binding, stop and check alignment straight away.
- Contamination:
Fine rubber dust can sneak in past poor seals. Use dust-resistant guides, and keep wipers fresh.
- Noise:
Squeaks or rattles are warning signs. Lubricate and check for loose hardware.
Stick to genuine replacement parts and demand certified service techs. Cheap knockoffs or sloppy installs will cost you more in the end.
Innovations and Future Trends in Linear Motion for the Tire Industry
The future of tire manufacturing moves fast—and smart.
- Industry 4.0 and Smart Guides:
High-load guides now come with built-in sensors. They track temperature, wear, and movement. Hooked to a plant’s automation system, they predict failures before disaster strikes, earning back lost hours and saving piles of money.
- Better Materials & Coatings:
New alloys and surface treatments fight rust and wear, lasting longer in the worst environments.
- Energy Efficiency:
Lower-friction, lighter guides mean less energy spent pushing loads. Tire plants see up to a 15% reduction in energy use, lowering CO₂ and cutting bills.
- Custom Solutions:
Every line is unique. We at Jimi provide custom linear motion systems tailored to your plant—servos, gantries, automation controls, all working together for top performance.
Conclusion: Ensuring Reliability and Efficiency in Modern Tire Manufacturing
Let’s recap. The right high-load linear guide brings more than smooth movement:
- Longer lifespan means five years of uptime instead of two.
- Less downtime, less maintenance, more output.
- Better tire quality, fewer rejects, and lower scrap rates.
- Cleaner, more energy-efficient operation means higher profits and a smaller footprint.
For your next upgrade, don’t just settle. Rely on experienced pros like Jimi Technology. With decades of expertise in the rubber industry and heavy-duty linear motion, we guide top manufacturers from selection to installation—all backed by world-class support.
Ready to take control of your plant’s performance? Explore Linear Guides & Rails, discover high-strength Heavy-Duty Linear Actuators, and see how advanced Ball Screw Actuators can transform your line. Need custom motion for robotics or assembly? Check out DIY Projects & Robotics Linear Actuators or Industrial Automation Actuators from our full range.
Choose engineered reliability—choose Jimi. Your tire machine’s backbone depends on it. Get in touch today, and drive your production forward with confidence.