Introduction: The Brains Behind Precise Linear Motion
Think about your last tough day at work. Did you need something done fast, but your machine just wouldn’t cooperate? Maybe the moving parts were too slow or shaky. Maybe you even had to stop everything to fix one little problem. In the world of automation, these problems are common. They waste time, cause headaches, and make work harder than it should be. But what if you could control every movement with total accuracy, safety, and speed—every time?
You can, when you choose the right linear actuator controller. This smart device is the “brain” that tells your actuator motor how far, how fast, and how strong to move. It turns electric signals into smooth, powerful motion. Whether you’re running a giant robot or moving a small desk at home, the controller is what makes precision possible. But with so many choices and new features—how do you know which is right for you? Let’s walk through what matters, from the basics to advanced solutions, and see how Jimi Technology is leading the way.
Foundational Concepts of Linear Actuation
Not all linear actuators are built the same. First, you’ll find three main types: electric, hydraulic, and pneumatic. Today, electric linear actuators rule in home and industrial automation because they’re clean, precise, and easy to control. Want to see the difference? Compare these actuator designs:
- Electric linear actuators: Run with motors and move with high accuracy using a controller. Find great examples at Electric Linear Actuators.
- Hydraulic actuators: Powerful, but messy and need a pump.
- Pneumatic actuators: Fast, but often noisy and hard to control for small movements.
Now, the secrets to “smart” motion are the actuator’s key specs:
- Stroke: How far can it push or pull?
- Force: How strong is it?
- Speed: How fast does it move?
- Duty Cycle: Can it run non-stop or only in bursts?
- Environment & Protection: Will it endure dust, water, vibration, or extreme heat?
You can’t control what you don’t measure. So smart systems add feedback (like encoders or sensors). The actuator, controller, and feedback sensor form a tight-knit team. The controller listens to the sensor and keeps motion right on target no matter what.
Core Control Methods and Underlying Principles
Craving simple? Some systems use open-loop control. You flip a switch, and the actuator moves. But without a feedback sensor, you never know if it stopped in the right place. That’s fine for simple jobs like opening a lid, but risky for machines where exact position or speed matters.
Closed-loop control fixes all that. With feedback like potentiometers or encoders, the controller “knows” exactly where the actuator is and adjusts as needed. Here’s how advanced closed-loop magic works:
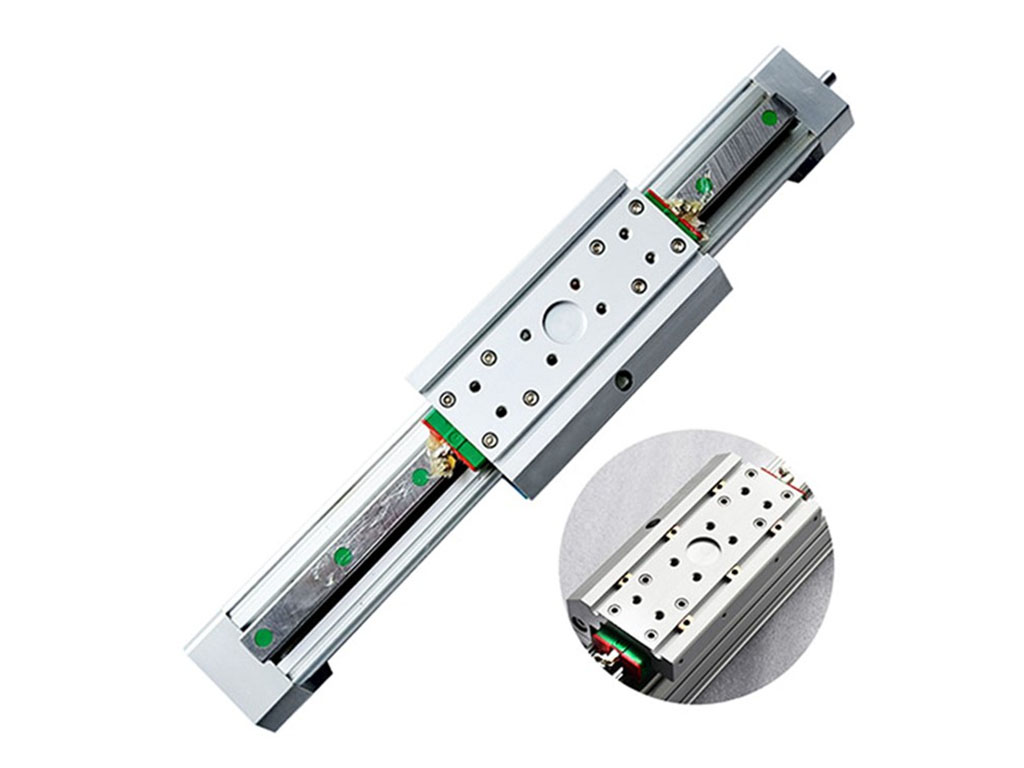
- Pulse Width Modulation (PWM) lets you fine-tune speed or position by adjusting how much power goes to the motor and for how long.
- PID control takes it further. It looks at the difference between where you want to go and where you are. Then it tweaks movement until you get perfect, stable results. This is how you hit accuracy like ±0.01 mm and repeatability up to ±0.005 mm—numbers that matter in cutting-edge factories.
Some systems snatch smart ideas from advanced math. Fuzzy logic and other algorithms handle twisty, real-world problems with ease.
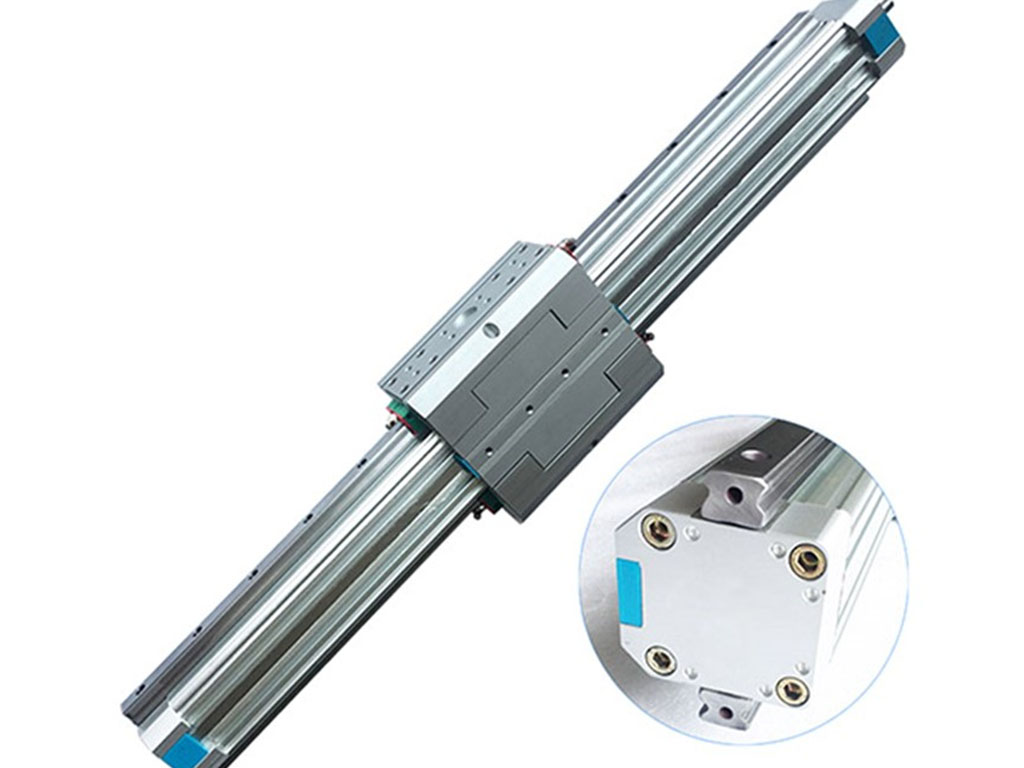
Don’t forget motor choice. Should you use voltage control or current control? DC, stepper, and brushless DC (BLDC) motors each have their best uses. DC motors love smooth moves. Steppers hit fixed points like clockwork. BLDC motors shine when speed, silence, and power matter most. Your controller should match and optimize your motor, not hold it back.
Comprehensive Classification of Linear Actuator Controllers
Ready to choose? You’ll find two main controller families: integrated and external/standalone.
- Integrated controllers fit right in the actuator housing. This gives you:
- Small footprint.
- Easier installation.
- Less wiring hassle.
- Quick, simple jobs (think adjustable beds, hospital lifts, or simple smart home kits) love these. The downside? You trade flexibility and may risk overheating in hard jobs.
- Find powerful integrated solutions for all scales of automation at Industrial Linear Actuators.
- External or standalone controllers bring the big guns:
- Basic motor drivers (like H-bridges): Offer simple on-off and direction control.
- PLCs (Programmable Logic Controllers): Take on industrial-scale controls, letting you tie in sensors, alarms, and complex logic.
- Microcontrollers (Arduino, Raspberry Pi): Ideal for prototypes, labs, or budget systems.
- Dedicated motion controllers: Handle tricky, multi-axis operations—like robotics or automated production lines.
They come with tons of features (multi-axis sync, heavy-load handling, custom programs) but need more setup. And you’ll face more wires!
Looking for the latest? Specialized options offer network control (Modbus, CAN bus, EtherCAT) or go wireless (Bluetooth, Zigbee, Wi-Fi). Some have touch screens or full Human-Machine Interfaces (HMI) built in—no extra display needed.
Key Features and Specifications to Evaluate
Picking a great controller isn’t just about speed or power. You want features that make your life easier—and your work safer.
- I/O Capabilities: Digital (on/off), analog (smooth variable input), and relay outputs so you can connect to any signal.
- Feedback Compatibility: Works with all top sensor types—encoders, potentiometers, Hall sensors, and limit switches.
- Communication: Knows all the big languages—Modbus, CANopen, PROFINET, EtherCAT, Ethernet/IP, RS-232/485.
- Programming: Includes GUIs, ladder logic for PLCs, or open scripting and APIs for custom code.
- Safety Measures: Overload protection, thermal shutdown, emergency stop, dynamic braking, and anti-pinch features.
- Environmental Ratings: IP ratings mean the controller can battle dust, water, and weather. Check ranges for shock, vibration, or wide temperature swings.
- Power: Handles your input voltage and current needs without risk. Bonus points for energy-saving modes.
It’s not just fancy words. Adding optimized PWM, regenerative braking, or standby modes can yield up to 80% energy savings compared to old hydraulic or pneumatic units (Manufacturer Technical Reports).
The Strategic Selection Process: Matching Controller to Application
Here’s where the rubber meets the road. Before you pick a controller, ask yourself:
- How precise does this motion need to be—down to a millimeter, or just “close enough”?
- Does your project need huge speeds, monster force, or both?
- Will the gear live in dust, heat, wet environments, or shake from nearby machines?
- Do you need to plug it into other equipment—PLCs, SCADA, or an HMI?
- What’s the real budget, and where do you want to invest for results?
Pick a controller that matches your motor: DC for smooth moves, Stepper or BLDC for exact hits. Think long-term, too. Is your system growing soon? Choose scalable gear and vendor support now, so you avoid giant headaches in a year. And always check for solid documentation, support, and certifications (CE, UL, RoHS) to make sure your investment stands up to the toughest standards.
Looking to see the hardware in action before you buy? Check out internal resources such as Actuator Controllers for comprehensive solutions and product specs.
Advanced Integration, Connectivity, and IoT
Today’s smart factories and homes talk to everything. So do today’s controllers.
They connect to PLCs and DCS systems with ease, slotting into big automation builds. You can track and tweak every move live, thanks to visual HMI or SCADA dashboards.
And here’s the cool part: Many new controllers link to the cloud. You monitor them from anywhere—phone, PC, you name it. They send alerts before problems hit. They log data that helps you fine-tune, plan, and even predict breakdowns. Modern controllers offer open APIs, SDKs, and familiar programming tools. That’s how you future-proof and customize your system your way.
Check out DIY Projects & Robotics Linear Actuators for examples and modules that thrive on open connectivity.
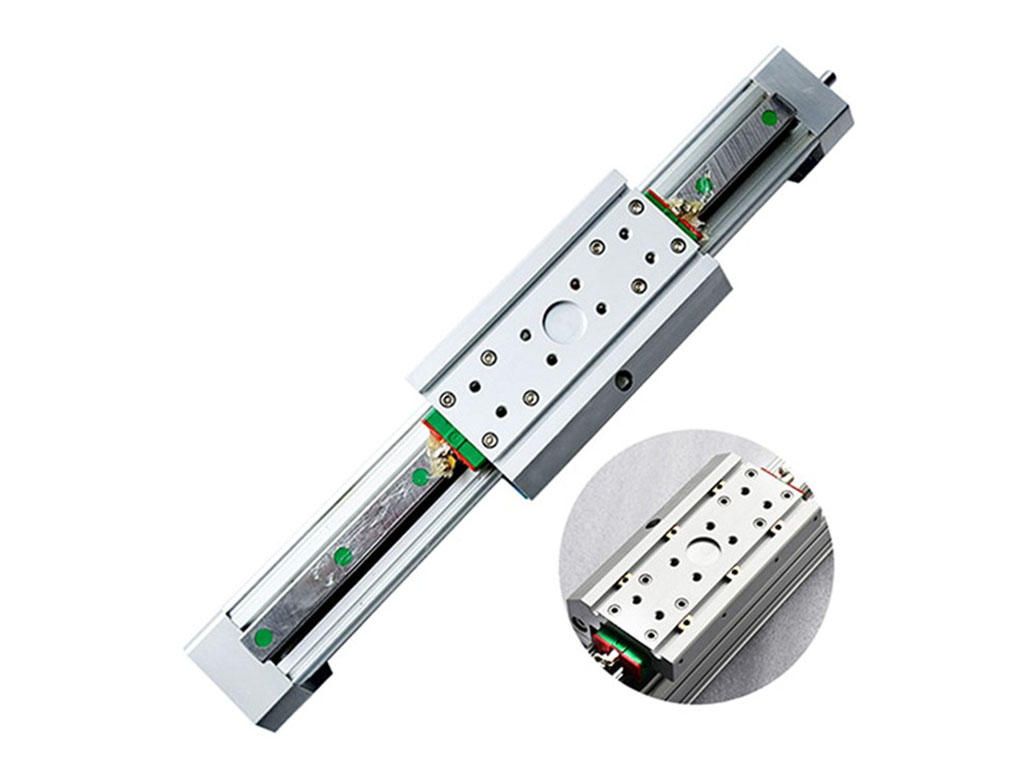
Real-World Applications and Illustrative Examples
So, what can a great controller do for you or your business? Let’s look at real scenarios.
Industrial Automation
Manufacturers use linear actuator controllers to automate robots, move products, or position valves with crazy accuracy. According to industry numbers, automation now grabs almost 45% of the global linear actuator market. Smart controllers mean fewer errors, less downtime, and higher profits.
Medical Devices
Ever watch a hospital bed adjust quietly and smoothly? Or see a robotic surgical tool move with pinpoint control? That’s high-end actuator control at work. Medical automation is the fastest-growing segment, valued for its gentle, energy-saving motion.
Home & Building Automation
Imagine blinds that open at sunrise, desks that rise with one tap, or hidden TVs that pop out of a cabinet. These all use compact controllers tucked out of sight, running smooth and silent.
Agriculture
Farmers automate greenhouse vents, feeders, even seed drills using rugged, weather-rated controller-actuator pairs—saving huge time and resources.
Specialized Applications
From controlling flight surfaces in aerospace, to making delicate scientific test equipment, to moving solar panels, linear actuator controllers are everywhere. For custom needs like these, China Electric Cylinder Factory offers tailored solutions and design consulting.
And it’s not just comfort or convenience. A smart, IoT-enabled linear actuator controller can cut downtime by 20-30% and stretch your equipment lifespan as much as 20%, thanks to predictive maintenance.
Troubleshooting Common Linear Actuator Controller Issues
Stuff happens. You push “go,” but nothing moves… or moves the wrong way. Let’s fix it:
- Erratic Movement: Check feedback sensors or wiring. Dirty encoders and loose connectors can cause jitters.
- Overheating: Is the load bigger than rated? Maybe ambient temps are too high, or you’ve chosen the wrong duty cycle.
- Comm Failures: Make sure the communication protocol matches on both ends. Bad cables or EMI can mess up data.
- Power Problems: Grab a multimeter. Confirm supply voltage and ground. Any dip can knock your controller offline.
Most issues clear up fast if you use systematic diagnostics. Start at the power, then check wiring, sensors, and controller firmware. Replace parts one by one to quickly isolate faults.
The Future Landscape of Linear Actuator Control
Where’s all this headed? The next wave of actuator controllers is getting even smarter. AI and machine learning let systems adjust themselves in real time, handling changing loads and predicting faults before you notice them.
We’re seeing edge computing—controllers with enough power to crunch data on the fly, without waiting for the cloud. More and more, you’ll see modular, plug-and-play controls anyone can install. Shrinking sizes, growing brains—these are not your grandfather’s motors.
Controllers focus more than ever on saving energy, being green, and working in any environment. The result? More uptime, less waste, and faster ROI for any project.
Conclusion: Powering Precision, Performance, and Progress
Here’s the bottom line. The controller is the unsung hero in every linear motion system. Pick the right one, and you get speed, power, and pinpoint accuracy—plus less maintenance, greater uptime, and huge energy savings. That’s progress you can measure.
At Jimi Technology, we put thirty years of engineering muscle behind every linear actuator system we build. Our controllers fit everything from mini medical bots to industrial muscle. We help you engineer upgrades, customizations, and integration into your factory or your home—backed by a team that cares about your success. It’s not just equipment. It’s a promise to power your ideas and make every motion count.
Ready to see the difference? Explore our full range of Servo Linear Actuator Factory solutions, talk to our engineers, or browse our Actuator Controllers for more specs, guides, and real-world stories. If you want ultimate control—Jimi is here to help you move your world, one smart step at a time.