Modern factories never stand still. Technology gets more advanced. Products change faster than ever. But behind the scenes, a hidden struggle drags everything down: making different machines, robots, and systems actually work together. Factory teams rush new product lines, only to face months of engineering bottlenecks. One small change in a production line delays everything. A fancy new robot with the wrong connector? Start again. Even today, integrating machines feels like putting together ten puzzles where none of the pieces fit.
If you’ve ever waited for a new production cell—wondering when that custom wiring will finally arrive—you know this pain. Projects run late. Budgets explode from endless rework and “unexpected” problems. You’d think with all our tech breakthroughs, connecting machines could be as easy as clicking LEGO® bricks together.
This is the bottleneck that holds back modern manufacturing. The old way, known as monolithic machine design, forces every part to depend on the whole system. The more you add, the messier it gets. Complexity doubles, then triples. Downtime stretches out while engineers hunt for bugs buried deep in code and cables.
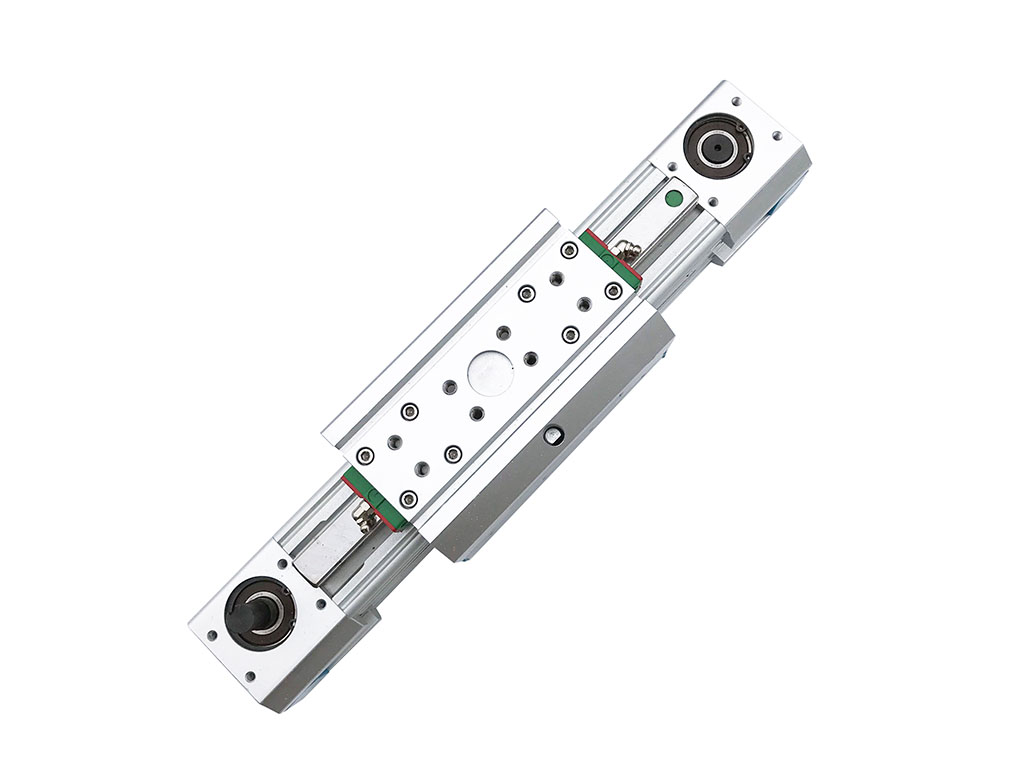
Traditional integration cost teams weeks or months every time they launched a new product or tweaked a process. Changing one piece triggers a domino effect of changes everywhere else. Need to add new vision sensors or a conveyor to handle bigger boxes? Forget a quick fix. You’re tackling spaghetti wiring, outdated drawings, and custom solutions that only one engineer understands. If that person takes a vacation, good luck.
Workers feel it, too. The rush to finish forces operators to train on each new system from scratch. Maintenance staff scramble for spare parts that only fit on one model. Troubleshooting turns into detective work.
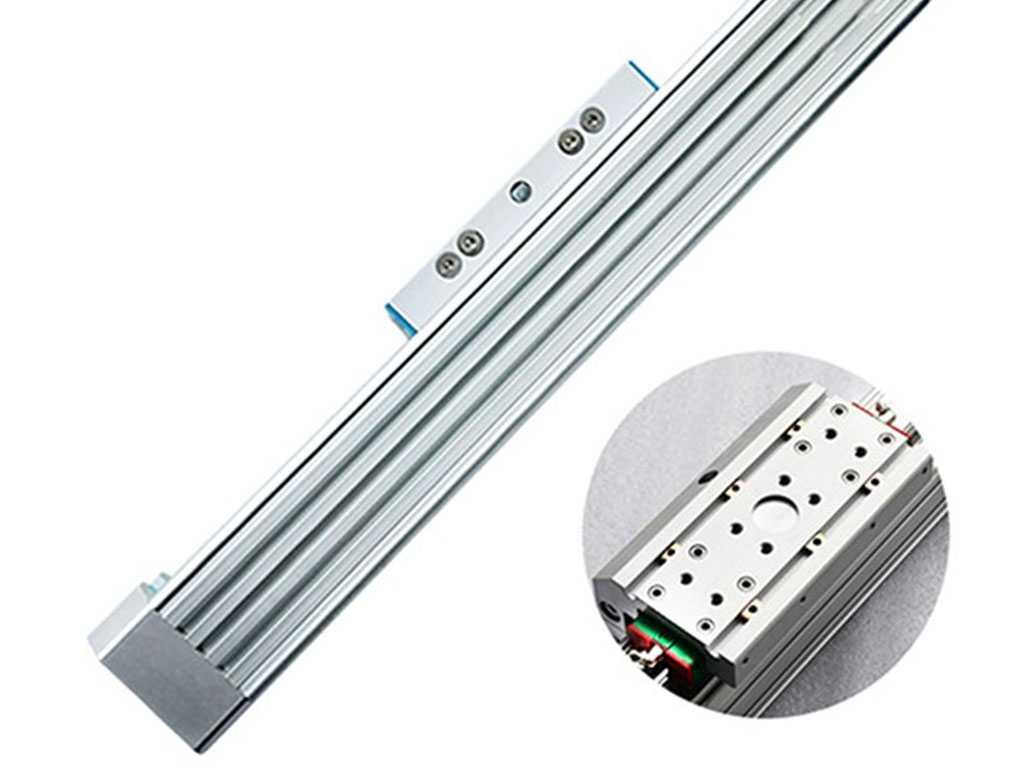
Now imagine a different world. One where you swap out old hardware for the new in hours, not days. Where each “block” of your production line just plugs in and runs. This is what modular design delivers.
Modular design treats machinery like a set of well-defined “modules.” Each unit has a job—lifting, sorting, packaging, testing—and comes built to a common standard. They snap together with plug-and-play precision. You don’t have to redesign the whole line every time you want to add a robot or upgrade a section. Standardized machine interfaces and connectors take care of the details. Engineering teams stop burning out on custom work and instead spend time improving real value.
Let’s break it down:
Modular Design in Industrial Applications—No More Square Pegs in Round Holes
Modular design is simple in concept but powerful in practice. Think of it as building with blocks. Each module is:
- Independent: It works by itself, without constant babysitting from other systems.
- Interoperable: It speaks a standard “language” to other equipment—hardware, software, and even data.
- Reusable: You can move modules between lines, swap them out, or upgrade one without redoing everything.
Compare this with monolithic machine design, where everything gets tangled together. One failure often brings down the whole line. Troubleshooting turns into a marathon, costing you both time and money.
How Modular Design Makes Integration Simple
- Standardized Interfaces and Plug-and-Play Robotics
Modular machines get their power from common interfaces. Jimi modules, for instance, pack all the right connectors for power, data, and controls into each block. You can connect a new vision inspection module or switch out a failed conveyor just as you would plug in a printer at the office.
- Reduced Custom Engineering: Instead of custom cabling and long engineering cycles, modules hook up fast. Less chance for errors.
- Compatibility Across Vendors: With open standards, you’re free to use parts from Siemens or ABB—or mix in your favorites from Jimi’s Electric Linear Actuators and Industrial Linear Actuators lines.
- Breaking Down Complexity into Manageable Chunks
Forget “fixing” the whole machine just to update one part. Each module in a flexible manufacturing system handles its own logic and operation. You isolate problems down to a single block. No more wild goose chases in endless wiring.
- Simplified Troubleshooting: You find faults in minutes.
- Minimized Interdependencies: If you need to increase speed or size, swap modules, not the whole line.
- Parallel Development and Faster Launches
With modules, engineering teams make and test each piece at the same time.
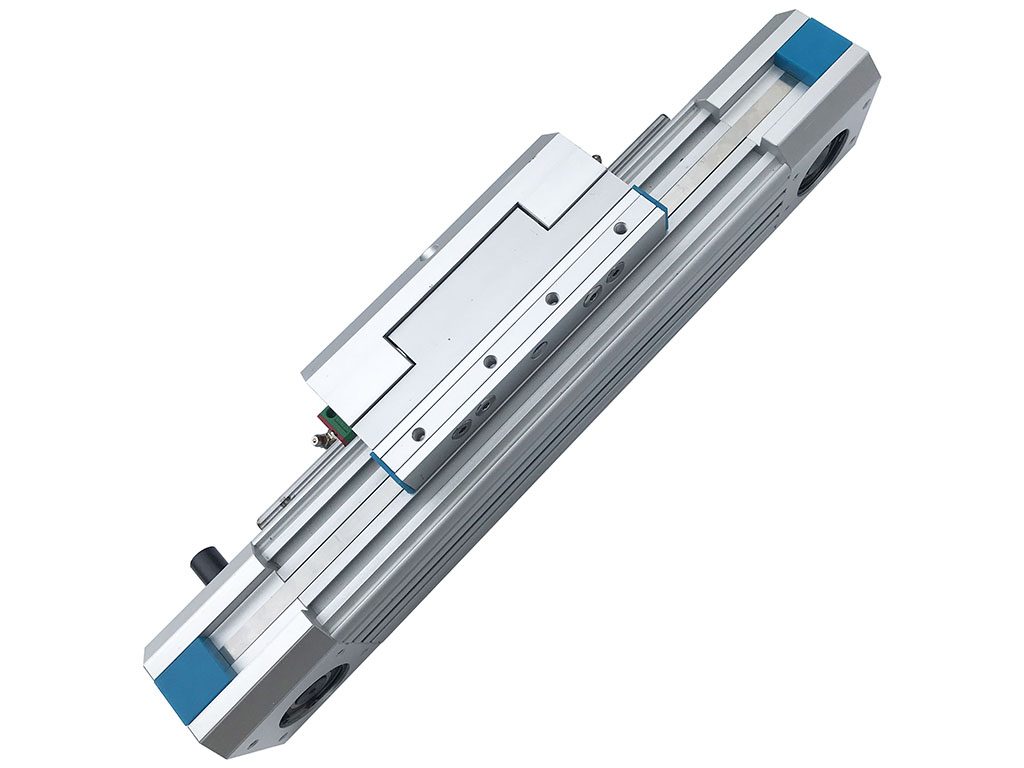
- Faster Assembly: Crews install multiple modules simultaneously.
- Less Downtime: Ramping up for new products gets cut from weeks to days.
- Decreased Time-to-Market: Data shows integration time drops by as much as 50%. A process that took 12-18 months now wraps up in 6-9 months. (See our case table below.)
- Flexibility and Scalability That Pays
Business needs change fast. Modular architecture lets you keep up. Adding, removing, or upgrading modules is quick.
- Flexible Manufacturing: Need to launch a new size, pack, or format? Slide out one module, add another. Done.
- Scalable Production: Grow by adding identical modules—no complete rebuilds.
- Streamlined Testing, Maintenance, and Upgrades
Teams can test each module before bringing everything together. No more late-night scrambles because one cable shorted.
- Simplified Repairs: Replace a faulty or worn module in hours, not days.
- Incremental Upgrades: Add new features without halting the entire plant.
The Real, Hard Benefits—Not Just for Engineers
Modular manufacturing isn’t only about simple connection—it’s about serious business results.
Cost Reduction
- Lower Engineering Costs: You can drop custom work by up to 30% by sticking with standardized, repeatable modules.
- Reduced Downtime: Quick module swapping means lines spend more time running.
- Optimized Inventory: Stock a few versatile spares versus dozens of custom parts.
Return on Investment and Asset Use
- Faster Payback: In many industries, ROI on flexible, modular solutions lands around 1-1.5 years—retiring old, wasteful setups in half the time.
- Productivity: Assembly lines push through more product with less headache and fewer breakdowns.
Future-Proofing and Agility
- Tech Upgrades: Add smart cameras or digital twins without rewiring everything. Stay current with Industry 4.0 and Internet of Things (IoT) advances.
- Market Resilience: Swap modules, not machines, as you chase new products or market changes.
Check out the numbers in action:
Table: How Modular Design Impacts Integration
Metric/Challenge | Traditional Approach | Modular Design Improvement | Example Industry |
---|---|---|---|
Integration Time | 12-18 months | 6-9 months (up to 50% faster) | Automotive |
Engineering Cost | High customization | Down 20-30% | Robotics |
Changeover | 2-4 days downtime | 4-8 hours (up to 90% faster) | Electronics Assembly |
Flexibility | Slow, high extra cost | Quick module swaps—easy | Packaging |
Maintenance | Hours–days | Minutes–hours (module replacement) | Pharma |
Scaling Up | Months (rebuild) | Weeks (add new modules) | Data Centers |
Troubleshooting | System-wide headaches | Narrowed to one module | Pumps, HVAC |
Error Rate | Frequent integration bugs | 15-25% fewer errors | Mixed Vendor Factories |
Operator Training | New training per system | Learn once, apply everywhere | Production Workforce |
Numbers don’t lie. What once required entire engineering teams can now be handled by a few skilled workers swapping out Standard/Inline Actuators or updating software on a modular HMI.
Jimi Technology: Machine Integration Should Be Effortless
We at Jimi understand the stakes. We’ve watched too many great products bottlenecked by integration woes and downtime. That’s why our focus stays sharp: deliver modular solutions that just work.
- Our actuators—such as Servo Motor Actuators and Rodless Actuators—arrive factory-ready for plug-and-play assembly, with robust controllers and easy-to-use connectors.
- Need industrial strength? Our Heavy-Duty Linear Actuators hold up under the toughest loads.
- Want to automate quickly? Our full line—from smart Kits with Remote Control to specialized Industrial Automation Actuators—keeps your crew moving, not waiting.
As an expert modular machine integration partner, we help world-class factories solve these exact challenges. We work side by side with manufacturers to standardize interfaces, decouple system layers, and supply modules that meet real-world demands—from the automotive giants to agile robotics startups.
Best Practices: How to Make Modular Manufacturing Work for You
- Start Early: Define your modules and standard interfaces at the project’s first stage. Solve the problem before it starts.
- Work Together: Bring suppliers, integrators, and even vendors like Fanuc or Cognex into your planning. More eyes, fewer blind spots.
- Standardize and Stick With It: Don’t let customization creep back in. Stay disciplined with design rules.
You’ll see quick wins even with small, early moves—like adopting modular Actuator Controllers or switching to common Mounting Brackets that fit every machine.
Looking Forward: Industry 4.0 and Beyond
This isn’t just a trend. The next generation—smart factories powered by AI, digital twins, and modular automation—runs on rapid change. Imagine simulation-driven design, machine learning that predicts maintenance before a breakdown, or quickly shifting to batch-of-one production. All require machines that don’t need weeks of coupling and coding each time you shift gears.
The Bottom Line—Modular Design Sets You Free
Modular design does more than simplify your day. It flips the script: integration stops being your biggest headache and becomes your competitive advantage.
- **Save time, slash costs, and boost ROI—**all proven with real-world results.
- Adapt and win, no matter what the market throws your way.
- Work with a partner who knows modular inside and out.
Don’t wait for the next integration crisis. Start building your flexible, efficient future today. Explore our China Linear Actuator Manufacturer solutions or dive into more specialized options, from Electric Cylinders to Industrial Automation Actuators. Jimi Technology stands ready to help your operation run smarter, faster, and more reliably. Let’s move your world forward, one module at a time.