Maximize Lifespan & Performance: A Comprehensive Guide to Linear Motion System Lubrication
Why Proper Lubrication is Non-Negotiable for Linear Motion Systems
Imagine you’ve got a production line that runs day and night. Or you’re counting on your CNC machine to make every cut, every time, with pinpoint accuracy. Now think about what happens if a tiny, overlooked thing—like bad grease or no oil—brings that line to a grinding halt. That’s not just a headache. It’s money out the window and precious time lost.
Linear motion systems (LMS)—linear guides, linear actuators, ball screws, bearings—drive the heart of automated factories, precision robotics, standing desks, and even hospital beds. Proper lubrication is the simple act that reduces friction, cuts down wear, fights heat, and keeps corrosion at bay. When you ignore it, the results are ugly: bearings fail before their time, productivity drops, accuracy goes out the window, and energy use jumps. Downtime can cost you big. A single hour of broken equipment can mean hundreds or thousands of dollars gone.
But there’s good news. By learning how to lubricate your linear motion system the right way, you’ll boost its life by up to five times. You’ll stop breakdowns before they start. And you’ll ensure your system runs quieter, smoother, and longer—with less hassle for you. Let’s get you there.
Understanding Your Linear Motion System and Its Lubrication Needs
Lubrication isn’t one-size-fits-all. Each component inside your LMS has its own quirks and favorite foods (okay, lubricants).
A. Linear Guides (Rails & Carriages)
Linear guides are made up of rails, carriages, and either balls or rollers inside. Most come with grease nipples or oil ports, asking you—politely!—to give them the care they need.
Key factors:
- Load and speed: Heavy, fast-moving guides need grease that stays put and won’t splatter out.
- Pre-load: Tighter guides need just the right film to avoid “grinding.”
- Environment: Dusty? Wet? Use grease with sealing power.
B. Ball Screws
Ball screws convert spinning motion into straight-line action for actuators, CNC machines, and more.
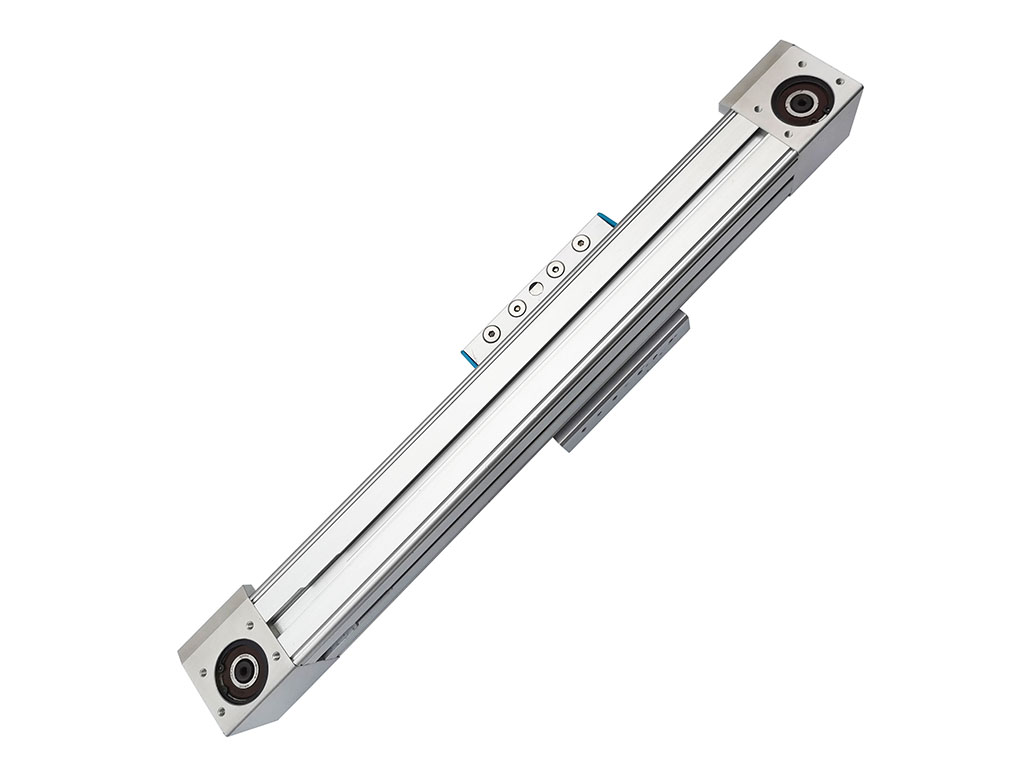
- You must lubricate the threads, ball nut, and support bearings. Don’t let dry metal grind together.
- Keep a thin layer of lubricant—like a “magic carpet” for those balls to roll on without resistance.
C. Linear Bearings (Bushings & Pillow Blocks)
You’ll find ball-type recirculating bearings, sliding bushings, and pillow blocks in all sorts of machines.
- Ball-type bearings love a thin but lasting film of grease.
- Plain bushings prefer the right oil—something that won’t dry up between re-lubrication.
- Always check your component’s manual or spec sheet. Design matters.
Want to get deeper into the world of linear guides & rails? We’ve got you covered with more resources.
Choosing the Right Lubricant: Grease vs. Oil and Key Properties
Staring at that shelf of lubricants, you might ask, “Do I need grease or oil? What’s with all these numbers?” It’s not rocket science, but, like a good recipe, details matter.
A. Grease
Think of grease as the peanut butter of lubrication. It sticks where you put it. It has:
- A base oil, a thickener, and special additives.
- NLGI grade: Tells you how stiff or runny it is (most guides like NLGI #1 or #2).
- Additives: Look for extreme pressure (EP), anti-corrosion, or special rust inhibitors.
Plus, grease is quiet, keeps out dust, and handles heavy jobs. The downside? It can trap dirt or get “gummy” over time, so cleaning is key.
B. Oil
Oil flows. It’s like salad dressing but better for machines.
- It cools parts well and flushes away bits of dirt.
- It lets you fine-tune application with systems like drip feed or forced circulation.
- You’ll need to reapply it more often, especially if your system is fast or under big loads.
When picking oil, pay attention to:
- Kinematic viscosity (how thick it runs).
- Viscosity index (how it handles changes in temperature).
- How stable it stays after lots of use.
C. Specialty Lubricants
Food industry? Cleanroom? High heat? There’s a lube for that. Choose food-grade for kitchens, cleanroom for labs, or dry-film for dusty or light-load environments.
D. Compatibility
Never mix lubricants. Old leftovers can cause nasty reactions that destroy components. Always check what your system’s manufacturer recommends. Don’t wing it.
Step-by-Step Guide to Proper Lubrication Techniques
Ready to get your hands a little dirty? Lubricating your LMS is simple, but the devil’s in the details.
A. Preparation is Key
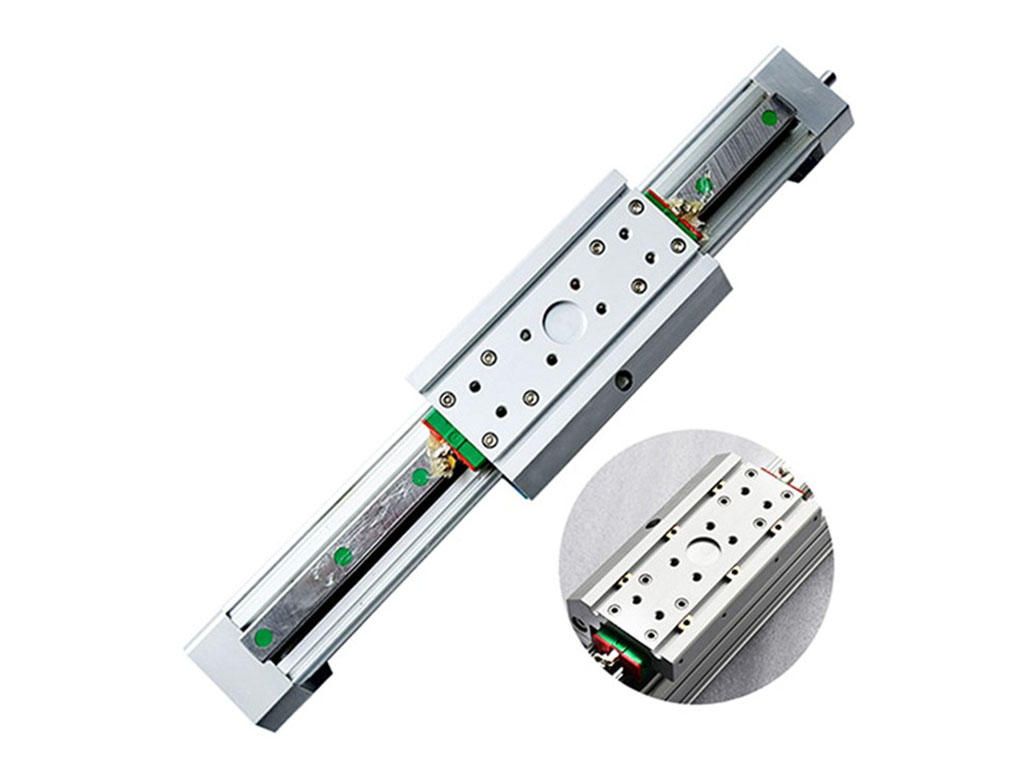
- Safety first
Shut down and lock out the system. Never lubricate while parts move.
- Cleaning
Wipe away grease, grime, and dust using lint-free cloths and mild solvents.
- Inspection
Look for scoring, pitting, or odd wear. If parts look rough, call us, or check our maintenance best practices for troubleshooting tips.
B. Application Methods
1. Manual Lubrication (Grease Gun)
Choose the right nozzle that matches your grease fitting.
Pump slowly. You want lubricant to fill, not explode out. Stop when you see fresh grease squeeze out the seals. Resist the urge to keep going—more is not better. Over-lubrication can increase drag, damage seals, and make a real mess.
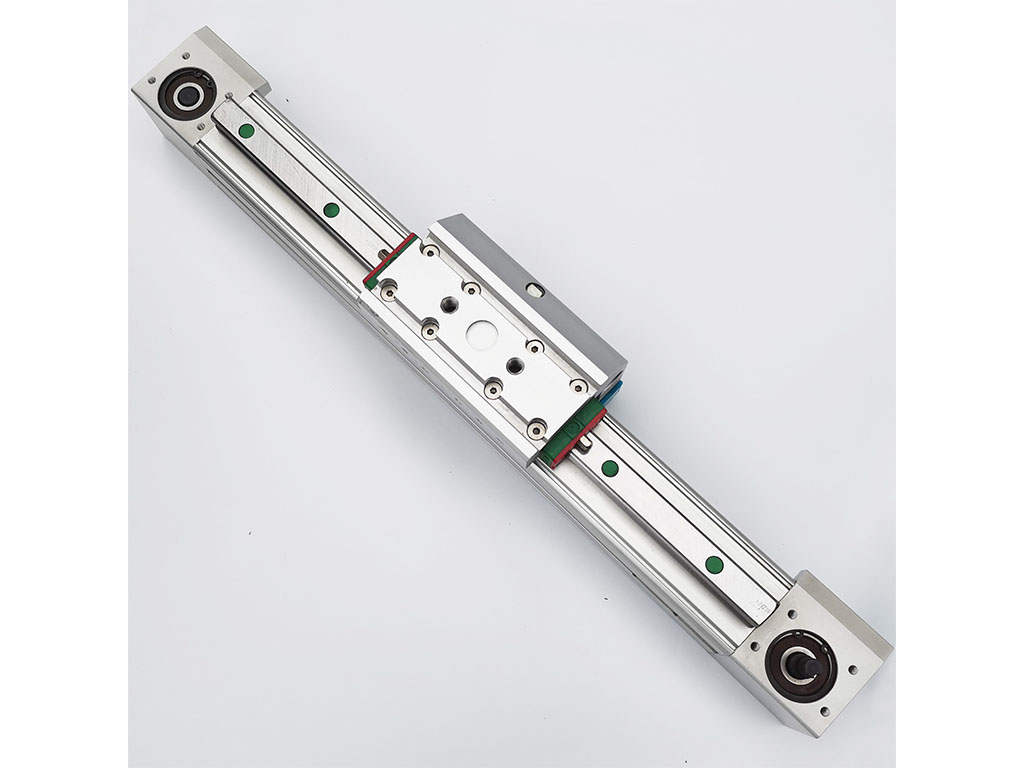
2. Oil Lubrication
If your system wants oil, use the right port. Drip-feed, oil bath, or forced oil systems need the correct flow rate. Don’t drown your bearings, just keep them moist and happy.
3. Integrated Lubrication Units
Some guides or bearings feature built-in lubrication units—think of them as “set it and forget it” systems. Still, you’ll want to check these every few months for performance.
C. Re-Lubrication Frequency & Quantity
- Machine too fast? Lubricate more often.
- Heavy loads or harsh environments (dust, heat, water)? Step up your schedule.
- Always start with your manufacturer’s recommended interval, then tweak based on how your system sounds or feels (noisy or sticky movement means you’re overdue).
- Use calculation charts, or check out our industrial automation actuator schedules for more info.
D. Post-Lubrication Checks
Once you’ve applied the new grease or oil:
- Run the system for a few minutes.
- Listen and watch—movement should be smooth, quiet, and leak-free.
If things are noisy, sluggish, or you see lube pouring out—stop and review your process.
Common Lubrication Mistakes to Avoid
Let’s keep your system out of the emergency ward. The mistakes below can shorten equipment life fast.
- Using the wrong type of lubricant: Grease in an oil system, or vice versa, is a surefire recipe for failure.
- Over-lubrication or under-lubrication: More isn’t always better. Too much grease can cause just as much trouble as too little.
- Skipping cleaning: Never lube over dirt. Old grease, grime, and dust can wreck new bearings.
- Mixing lubricants: This can cause chemical reactions that ruin both old and new lube.
- Ignoring the manual: Manufacturer specs exist for a reason. Don’t improvise.
- Exposing lube to contamination: Dirty hands, open containers, or storing lubricant in dusty conditions introduces particles that chew up your bearings.
Follow these simple rules, and your system will thank you with years of trouble-free operation.
Advanced Lubrication Strategies & Monitoring
Ready for leveling up? For big factories or tough applications, automation pays off.
– Automatic lubrication systems: These use pumps and timers to deliver just the right amount, reducing human error.
– Lubricant analysis: Test your lube with oil or grease analysis to monitor wear and contamination, so you catch little problems before they turn ugly.
– Condition monitoring: Vibration sensors or thermal imaging can spot trouble as soon as it starts. It’s like an X-ray for your machine.
We can help with all sorts of advanced automation and lubrication management. Need help choosing or integrating? Contact the expert team at Jimi Technology for guidance.
Lubrication Facts: What the Numbers Say
Aspect | Real-World Impact | Implication |
---|---|---|
Bearing failures | 43% come from improper lubrication | Don’t let bad lube take down your system |
Life extension | Lubrication boosts guide/ball screw life by 2-5x | Protects your investment, stops early failure |
Downtime cost | Downtime runs up to $1000s/hour | Proper care prevents money literally vanishing |
Energy savings | Friction drop means 10-20% less energy use | Your wallet and the environment win |
Maintenance savings | Right lube saves 15-30% in repairs | Invest now, save a bundle all year |
Water/dirt | Just 0.002% water in grease cuts life by 48% | Keep it clean, keep ruin out |
Too much lube | Over-lubrication spikes heat, breaks seals | Get it “just right” for long-term success |
Lube analysis | Regular checks predict and prevent failures | Data-driven moves for the win |
Jimi Technology: Your Partner in Precision, Protection, and Performance
We know every linear motion system is different, and that’s where our decades of hands-on experience come into play. At Jimi Technology, we’re not just a China Linear Actuator Manufacturer; we’re your expert in maximizing service life, boosting efficiency, and making every move count.
Our products—from Electric Linear Actuators and Ball Screw Actuators to Actuator Controllers—are built for easy, reliable lubrication and years of consistent performance. We back this up with deep technical support and application know-how, so whether you’re running a robot, standing desk, or complex industrial line, we’ve got answers.
Jimi supplies lubricants, linear guides, accessories, and tailored automation solutions—trusted by global manufacturers.
Why choose us?
- Expert advice that matches your application—not just catalogue pages.
- Proven products, rigorously tested to ISO and ASTM standards.
- Support that sticks around after the sale.
No more guesswork. No more wondering “Did I do it right?” Just smooth, reliable motion that lets you focus on achieving more.
Ready to take the next step? Start your system upgrade now:
- Visit our linear guides & rails section
- Check out our Electric Linear Actuators
- Or talk to our automation pros about your unique application
Conclusion: Protect Your Investment With Smart Lubrication
Lubricating your linear motion system isn’t just a maintenance chore. It’s your front line of defense against failure, noise, and waste. Do it well, and you unlock years of high-precision, worry-free moves. Forget it, and you pay in downtime, costly repairs, and lost peace of mind.
So, set your schedule, pick the right grease or oil, and trust in proven practices. And if you ever feel stuck, know that Jimi Technology is ready to back you up. Build a better, smoother, more efficient world—one drop of lubricant at a time.