Maximize Lifespan & Performance: A Comprehensive Guide to Proper Linear Motion System Lubrication
==============================================================================================
Do you ever hear a screech from your CNC machine that makes you wince? Or spot a little jerk in your robotics system and suddenly worry your linear guides are wearing down before their time? You’re not alone. Linear motion system owners around the world face this exact fear: parts breaking early, unexpected downtime, and the cost of replacing components that should have lasted for years. At Jimi Technology, we’ve seen it all. And almost every time, one thing is at the heart of the problem—improper or forgotten lubrication.
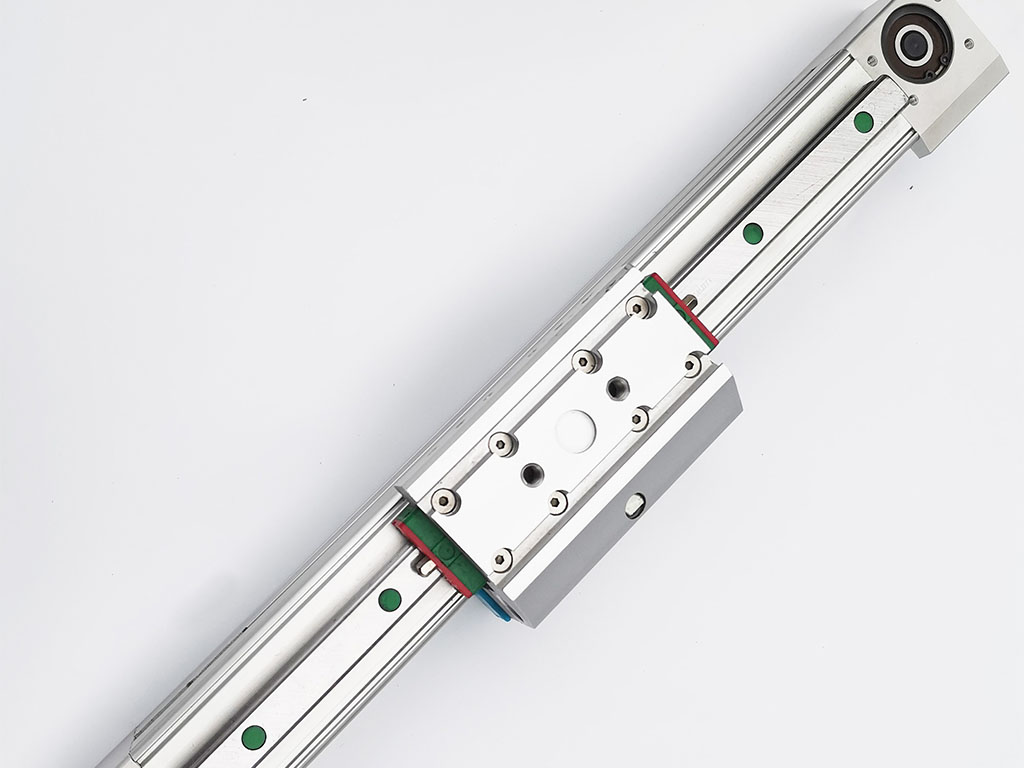
Let’s dig into why that happens, how it costs you, and most importantly, how you can fix it for good.
The Pain: Why Poor Lubrication Haunts Linear Motion Systems
Imagine this. You fire up your industrial automation gear. This thing is the backbone of your operation—precision and speed rolled into one. But today’s different. You hear grinding from the linear rail or those ball screw actuators don’t sound so smooth. Maybe you run a routine check, and your rodless actuators feel stiff, or your CNC bed vibrates and jitters.
That’s bad news. Here’s the kicker: studies show that 50-70% of all linear bearing failures stem from improper lubrication. That’s right—half or more of costly downtime, inaccurate cuts, lost output, or broken equipment often comes down to skipped grease or the wrong oil. Every year, maintenance and engineering teams waste days (and budgets) fixing problems dirt-simple lubrication could have stopped.
Even small neglect grows fast. Without the right grease, friction builds heat that destroys bearings, triggers wear, and even invites corrosion. Loose particles sneak into unprotected metal-to-metal contact, cutting down precision and shortening component lifespan. Your “set it and forget it” system ends up being the opposite, needing constant repairs.
You might think, “I just add a touch of oil when things get noisy, right?” Not quite. Under-greasing causes the system to grind and chew itself apart. Over-greasing blows seals, messes with system accuracy, and traps contamination. Using kitchen-grade stuff on a high-speed lead screw? That disaster needs no explanation.
In real-world terms, improper lubrication can:
- Slash linear guide or ball screw life by more than half
- Cause up to 40% more unscheduled downtime
- Increase maintenance costs by 15% or more each year
- Waste 5–10% more electricity due to extra friction
- Drop overall system accuracy and reliability
No factory, machine shop, or automation enthusiast wants those headaches.
The Agitation: How Improper Lubrication Drains Your Time and Money
Think about the last time your linear system moved slower than before or got louder. That’s not just normal aging—it’s a warning sign. Each hour of missed grease or the wrong oil eats at your investment.
Some shop floors, we’ve seen, create emergency schedules just for unscheduled breakdowns linked to poor lubrication. Talk about wasted labor. Others pay for new electric linear actuators or mounting brackets long before they should. More than a quarter of maintenance crews admit they go by “it feels about right” instead of following manufacturer specs, leading to disaster.
Imagine saving up to 40% on downtime or doubling the working life of your linear guides just by adopting the right lubrication habits. These aren’t pipe dreams—they’re proven facts.
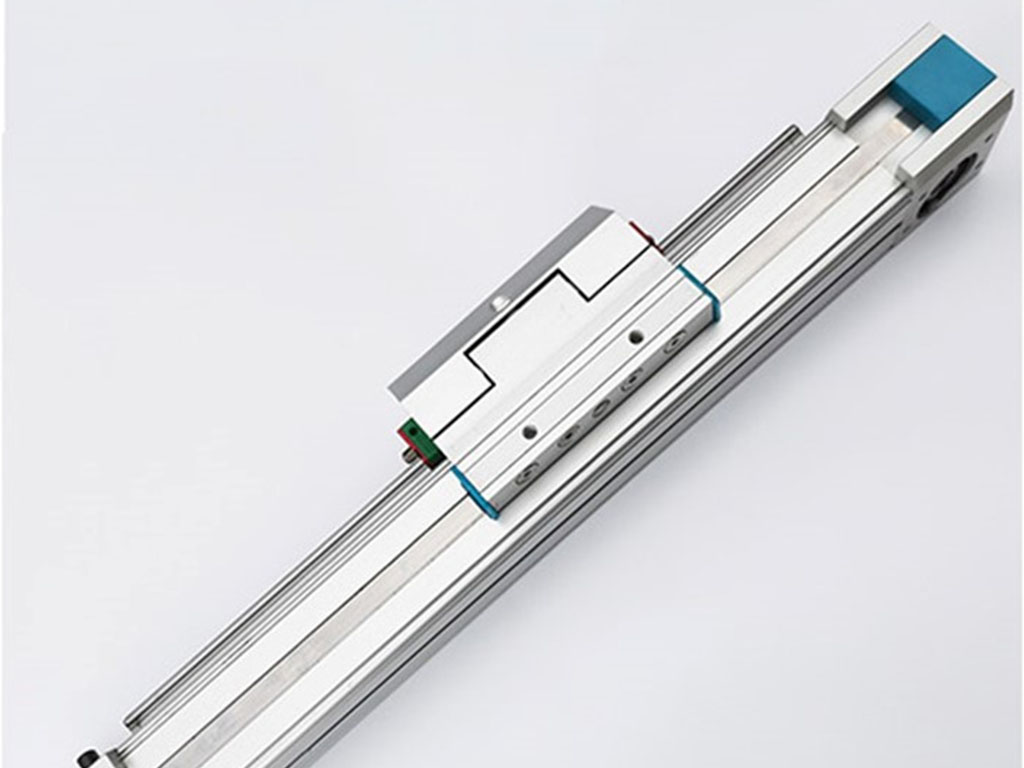
The Solution: Perfect Lubrication, Step-by-Step—The Jimi Way
At Jimi Technology, we help users—from home robotics tinkerers to heavy industry leaders—extend the life and accuracy of their equipment with one powerful habit: perfect linear motion lubrication. We’re not just your average China Linear Actuator Manufacturer. We’re the experts that factories and labs rely on to keep motion systems running like new.
Let’s break it down.
1. Understand Your System’s Lubrication Needs
Every linear motion system has critical points crying out for the perfect lube:
- Linear guides (rails and carriages): These move loads in a precise line. Keep friction low and they’ll run like silk.
- Ball screws and lead screws: Responsible for smooth Translation and accuracy—even a little dirt or dryness can throw off performance.
- Linear bearings and bushings: They take the pounding, so extend their life with TLC.
Lubrication isn’t just about moving parts with less resistance. Done right, it:
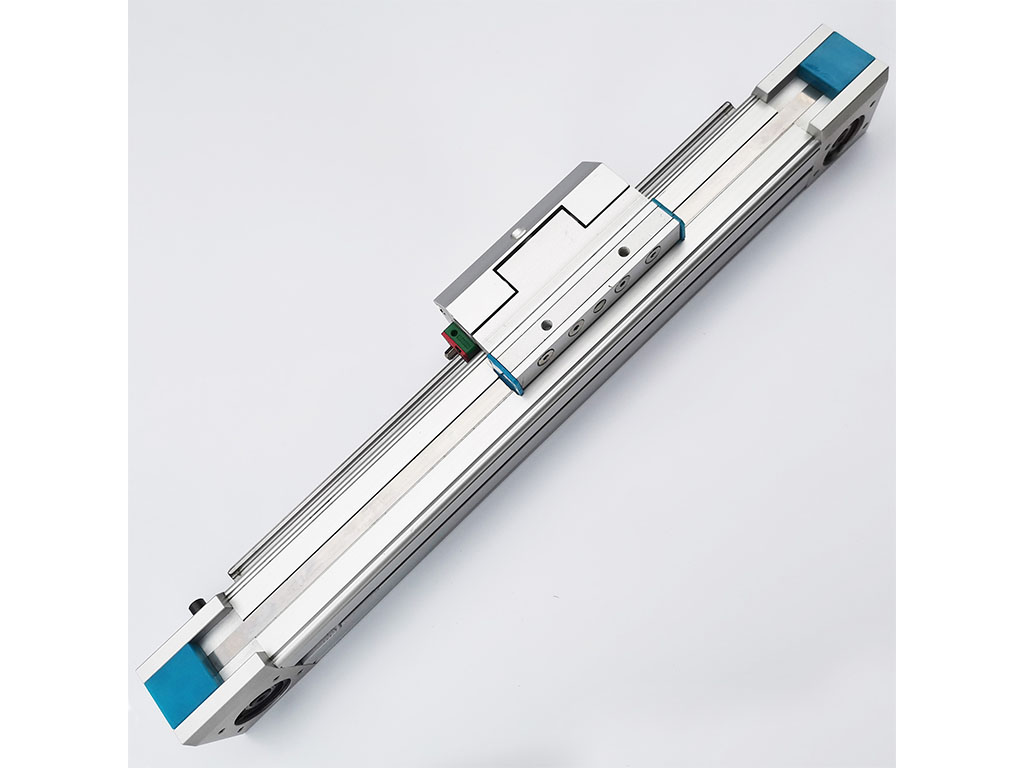
- Reduces friction and wear
- Dissipates heat so nothing seizes up
- Prevents rust and corrosion
- Damps noise and vibration
- Seals out grime and particles
- Keeps your system moving with accuracy and repeatability
2. Choose the Right Lubricant—Grease, Oil, or Special Types?
Not all lubricants are equal. Here’s what you need to know:
- Grease (your go-to for most linear systems): Made from base oil, a thickener, and special additives. Grease sticks in place, lasts longer, and works great for seals and enclosed guides. When picking grease, consider “NLGI Grade” (how stiff it is), base oil viscosity, and temperature range.
- Oil (for continuous lubrication or extreme heat): Flows better, carries away heat, but needs a pump or drip system. Works best for high-speed or open systems.
- Specialized lubricants: Food-grade (for kitchens or medical), water-resistant (for outdoor or washdown), high-temp, low-temp, or dry film types exist—choose based on your need.
Crucial rule: Always check your system’s manual or ask a pro (like us at Jimi). Leading brands like THK, NSK, HIWIN, SKF, and Bosch Rexroth always give their recommended grease or oil specs. Don’t wing it with what’s lying around.
Table: Grease vs. Oil for Linear Motion Lubrication
Lubricant Type | Best For | Pros | Cons |
---|---|---|---|
Grease | Ball screws, guides, bearings | Stays put, long interval, protects seals | Tougher to apply, can attract dirt if overused |
Oil | High-speed, high-temp equipment | Flows, cools, easy for automated systems | Needs regular replenishment, may leak |
3. Prep Like a Pro—Clean and Protect Before You Grease
Don’t just squirt in new lube and call it a day. Set the stage:
- Safety first: Wear gloves and goggles. Lock out power on large machines.
- Clean everything: Remove old grease, grime, and dust with a lint-free cloth and mild solvent.
- Inspect parts: Look for visible damage, worn seals, or signs of under-lubrication (rust, noise, vibration).
A clean starting point ensures the fresh grease does its job, not just push around old grit.
4. Lubrication in Action—How to Apply Grease or Oil the Right Way
- Manual lubrication: Use a grease gun (manual, battery, or air-driven), brush, or oiler.
- Find the lube ports or grease nipples on your linear rail or ball screw actuator.
- Pump steadily until you see new grease pushing out the old (called “purging”). If you see dirty old grease pushing out, you’re doing it right.
- Run the axis or screw through its full motion to spread the grease everywhere.
- For ball screws: Focus on both the nut and the shaft. Make sure every recirculating ball gets a coat.
- Automatic lubrication: For big or hard-to-reach systems, install a single-point or centralized lubricator. It keeps the right amount flowing and reduces the risk of human error.
- Keep it clean: Only use clean tools and sealed grease. Dirt can wreck high-precision linear bearings without warning.
5. Lubrication Frequency—How Often is Enough?
This varies. The perfect schedule depends on:
- Load
- Speed
- Environment (dust, heat, humidity)
- Number of operating hours
Still, a good rule? Check manufacturer specs, inspect visually, and err on the side of “just right”—not too much, not too little.
6. Common Mistakes to Avoid (Trust Us, We’ve Seen Them All)
- Over-lubrication: You’ll trap heat, damage seals, and attract more dirt. Go until you see new grease pushing out, then stop.
- Under-lubrication: If bearings squeak, get hot, or parts move stiffly, they need more.
- Wrong type of grease: Using the wrong base oil or NLGI grade can eat up performance. Always use what the manual or supplier recommends.
- Contamination: Never use dirty rags or open containers. One grain of sand is all it takes to damage micron-level tolerances.
- Skipping cleaning: Never squirt new lube on old grime. Clean first!
Tip: Keep a simple log of what you used, how much, and when. We’ve seen customers reduce their downtime by weeks just by tracking this info in a notebook or spreadsheet.
7. Troubleshooting & Best Practices—From Frustration to Automation
Are you hearing noisy rails? Is movement jerky, or accuracy falling off? High heat, weird vibration, or visible wear? These are red flags for poor lubrication.
Create a preventative maintenance plan—set dates for lube checks, cleaning, and refills. Store grease and oil in sealed containers, away from dust and sunlight, so it won’t spoil.
For some systems, especially in industry or automation, moving to a Servo Linear Actuator Factory or adopting automated lubricators pays off quick. Many clients recoup that expense in less than a year through reduced wear and fewer emergency repairs.
Why Choose Jimi for Your Linear Motion Needs?
We’re not just a supplier—we’re your automation partners. With decades of experience, we know what keeps medium-duty linear actuators and industrial-grade linear guides working smoothly. Our team picks and supplies only trusted lubricants that match your exact specs—no one-size-fits-all approach.
Our manufacturing muscle means every Jimi actuator, guide rail, and accessory comes ready for long life, precise motion, and easy maintenance. Still not sure what you need? Reach out to our expert team for practical help and personal recommendations.
Convinced it’s time to level up your linear motion maintenance? Browse our full lineup of electric linear actuators, ball screw actuators, or get help from our China Electric Cylinder Factory.
Invest in Lubrication—Invest in Longevity
Taking care of your linear motion system isn’t hard—but it is critical. With the right grease, the proper schedule, and a little attention to detail, you save money, boost accuracy, and perk up productivity. Lubrication done right turns annoying breakdowns into smooth motion that lasts. Start with a clean system. Pick the right grease or oil. Apply carefully, not carelessly. Avoid shortcuts and keep your system’s manual close.
Need authoritative advice or top-quality parts? Jimi Technology stands ready to help you solve your biggest linear motion headaches and keep your production line, robotics, or home automation running smooth for years. Start today—your future self and your bottom line will thank you.