Introduction: The Foundation of Precise Motion
Imagine building a CNC machine for delicate engraving. Your design looks perfect. Yet, the lines come out wobbly, not sharp. The reason? Often, it’s not the software or even the operator but the hidden heroes in the machine’s heart—the linear guides. These rails give direction to every move. But only when tuned for preload and rigidity do they deliver true precision.
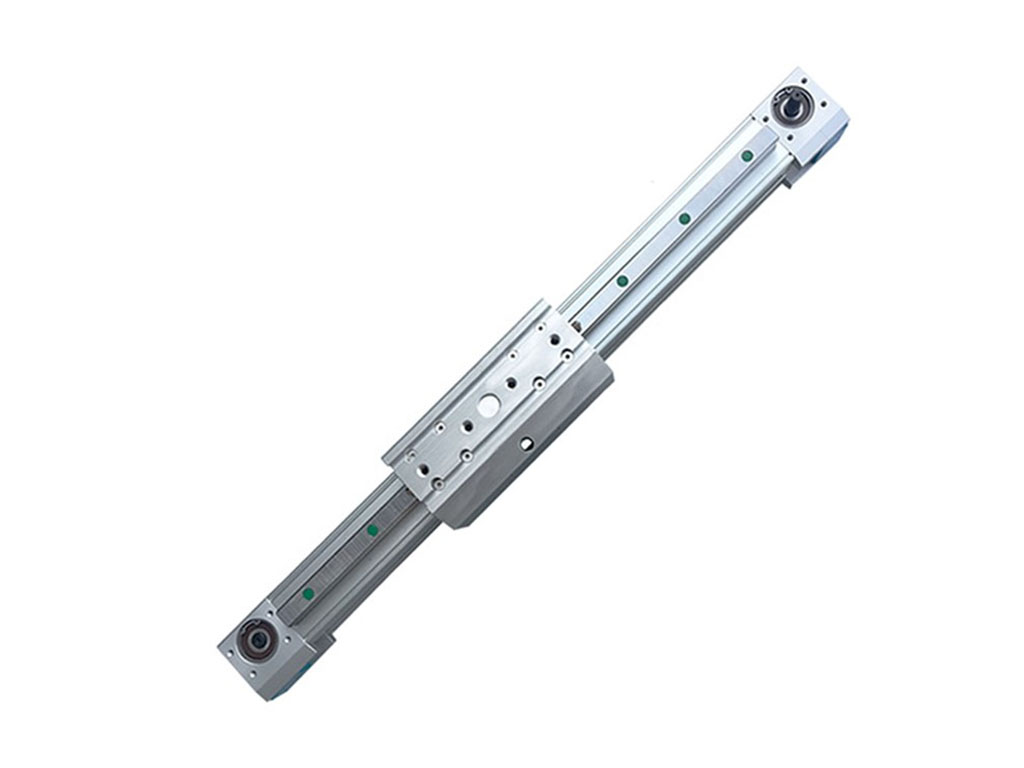
In industry, every fraction of a millimeter matters. That’s why we at Jimi Technology focus so much on the science of motion. Preload and rigidity set the tone for accuracy, repeatability, and performance in any modern motion system, from robots assembling smartphones to the measuring arms in metrology labs. If you want your automation to shine, you need to tackle these two factors head-on.
Understanding Linear Guides: Beyond Basic Motion
Let’s break it down. Linear guides—think of them as train tracks and linear bearings as the train cars—let parts glide in perfect straight lines. You’ll find three main types:
- Ball bearings: the all-rounders, great for speed and lower loads.
- Roller bearings: built for tough jobs, offering high stiffness.
- Plain bearings: simple, cost-effective, but not for deep accuracy.
Their job? Deliver smooth, constrained movement, minus the hiccups. In manufacturing, that means every part lines up just right. In clinics, surgery robots operate with steady hands. Even a tiny slip costs time, quality, and money.
Why sweat such fine details? Because the closer you cut to perfection, the higher your productivity climbs. Fewer errors mean less downtime and happier clients. That all comes down to linear motion precision.
Deconstructing Preload: Eliminating Play for Performance
What is Preload?
Picture yourself shaking a drawer. If it rattles, there’s “play”—looseness that can ruin accuracy. Preload is the gentle squeeze engineers build into a linear bearing, pushing balls or rollers snug against their raceways. This internal force wipes out all clearance.
How Do You Create Preload?
There’s more than one way to add this magic touch:
- Fit slightly oversized balls or rollers in the bearing.
- Use offset raceways so movement starts under a gentle force.
- Precision grind the parts to super-tight specs.
- Sometimes, compress key components, like a ball nut, just a hair.
Classes of Preload
Not every job needs the same squeeze. There are three main preload “classes”:
- Light (C1/Z1): For basic guiding or where you want minimal friction, like in packaging lines.
- Medium (C2/Z2): Your everyday hero—balancing friction, stiffness, and lifespan for general industry or robots.
- Heavy (C3/Z3): Think ultra-precise—making semiconductors, measuring parts down to microns.
Benefits of Optimal Preload
When the setup is just right:
- No more play or backlash. The carriage moves exactly as commanded.
- System stiffness jumps. Parts resist flex, holding positions steady.
- Precision soars. Devices hit the same spot over and over.
- Less vibration. Preload dampens jitter, keeping machines quiet.
- Longer fatigue life if the load’s in the sweet spot.
Drawbacks of Excessive Preload
Go too far though, and trouble creeps in:
- Friction and heat rise. Motors work harder.
- Service life drops. Parts wear out fast.
- Energy costs jump. Machines gulp extra power.
- Plus, you might hear more noise from stressed bearings.
The Essence of Rigidity: Minimizing Deflection Under Load
What is Rigidity?
Rigidity is a simple idea with huge power. It answers this: when a force pushes, how much does the part bend? Technically, it’s force per unit of movement (N/µm). You want as little give as possible.
Why Is Rigidity Critical for Precision?
Here’s why engineers lose sleep over this:
- Low rigidity means parts flex under heavy loads. Machines miss their marks.
- Good rigidity means every position is true, even as tools change direction or speed.
- It keeps the relationship between tool and workpiece rock solid, especially in cutting, grinding, or 3D printing.
- Most importantly, high rigidity kicks vibration and chatter—the enemies of smooth surfaces—to the curb.
What Shapes Linear Guide Rigidity?
Several factors come into play:
- Bearing design: Rollers pack more punch than ball bearings for stiffness.
- Material matters: High Young’s modulus equals less flexing.
- Mounting surface: A wavy mounting surface robs you of all the gains; flat and parallel is a must.
- Support and fastening: More bolts, better support, less wobble.
- System integration: It’s not only the guides—it’s also the rail, ball screws, couplings, even the frame.
The Interplay: How Preload Enhances Rigidity for Superior Precision
Preload’s Direct Contribution to Rigidity
Here’s where the magic happens. When you preload a bearing, every point of contact starts tight. This banishes the initial “free play”—the wobbly zone—so small forces can’t shift anything. The whole system jumps to a stiff, linear response.
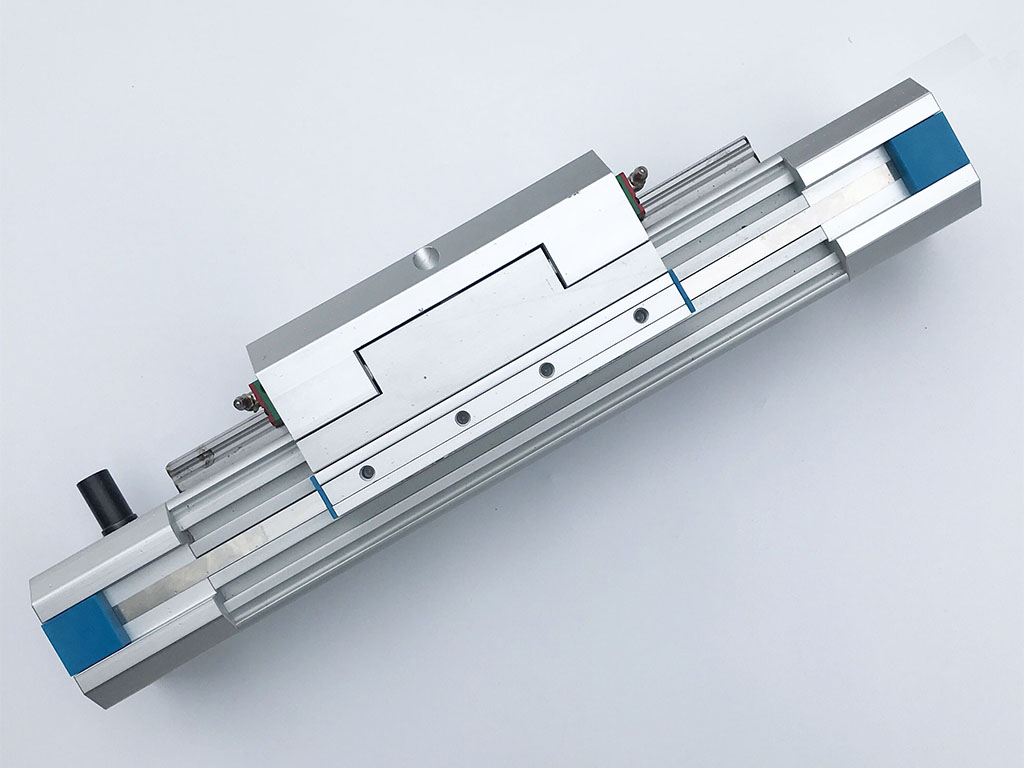
Impact on Positioning Accuracy and Repeatability
Real-world result? Less flex means tight positional accuracy and repeatability. Your machine will always return to the same spot, whether you’re stacking tiny chips or carving intricate molds.
Mitigating Vibration and Chatter
More rigidity does double duty: it raises the system’s natural vibration frequency. That moves troublesome resonance out of reach. Add preload and you even get some damping, sucking up vibrational energy before it turns into chatter or tool marks.
The Optimization Balance: Finding the Sweet Spot
Not too tight, not too loose. Here’s how it plays out:
- Too little preload: The carriage wiggles. Results are sloppy, and vibrations sneak in.
- Too much preload: Bearings burn out, motors strain, and costs go up.
- The sweet spot? A precise preload matched to your machine’s real loads, speeds, and accuracy needs.
Beyond Preload & Rigidity: Other Factors Affecting Linear Guide Precision
Shoring up preload and rigidity unlocks most of your precision, but keep these in mind:
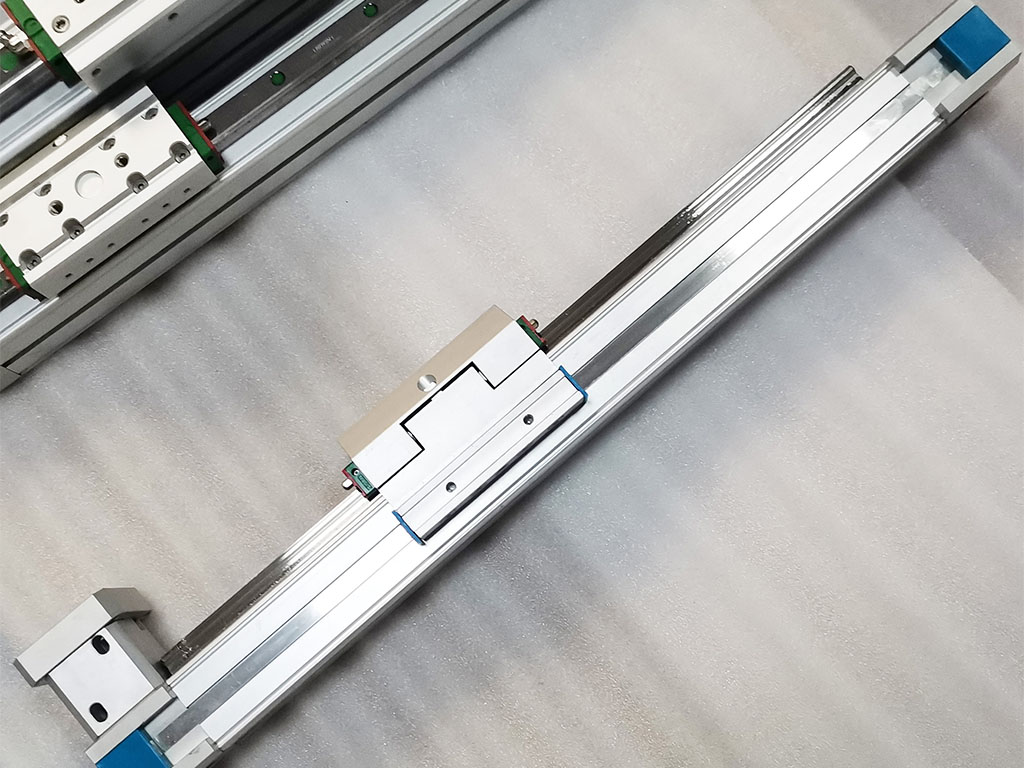
- Mounting surface quality is king. Bumpy or out-of-parallel bases destroy rail accuracy.
- Thermal expansion shifts parts around as they heat up or cool.
- Contamination and lubrication keep movement smooth. Dirt kills bearings.
- Drive system stiffness—like the ball screw or coupling—matters.
- Dynamic loads—sudden accelerations—test the whole system.
- Wear and tear: Even tough components lose their edge over time. Check for signs of play or rough motion.
Real-World Impact: Data, Case Studies, and Application Insights
Let’s get concrete with a simple table:
Preload/Rigidity Level | Stiffness | Precision | Application |
---|---|---|---|
Zero/Loose | Very low | Poor | Budget machines, low demand |
Light Preload (C1/Z1) | Moderate | Improved | Packaging, light automation |
Medium Preload (C2/Z2) | High | Good | CNC, general robots |
Heavy Preload (C3/Z3) | Very High | Excellent | Metrology, semiconductor, optics |
Excessive Preload | Too high | Risk of failure | Not recommended |
Low System Rigidity | Low | Unstable | Poor surfaces, slow processes |
High System Rigidity | High | Tight tolerances | High-end CNC, imaging |
Think about a CNC machine running at full speed. Switch from zero preload to medium and repeated positioning error drops from ±20 microns to ±2 microns. No more throw-away parts. In a coordinate measuring machine (CMM), heavy preload ensures measurements never wander, even under big probe forces.
We’ve seen similar stories with customers in the robotics and medical device industries. Proper preload and rigid design have cut cycle times and sent their defect rates plummeting.
Want to see real engineering in action? Check our Linear Guides & Rails for proven solutions and Electric Linear Actuators optimized for precision and repeatability.
Choosing the Right Linear Guide & Preload for Your Application
Every project has its own “right answer.” Here’s a quick guide:
High-Precision Applications (CMMs, Optical Systems)
- Go for maximum rigidity. Heavy preload (C3/Z3) wins here.
- Use roller guides for minimal deflection.
High-Speed/High-Acceleration (Pick & Place Robotics)
- Choose medium preload (C2/Z2). Balances stiffness with low friction to prevent overheating.
- Roller or high-quality ball guides depending on load size.
Heavy Load/General Industry (Material Handling, Large Machines)
- Prioritize load capacity and stiffness over top-end precision.
- Ball or roller guides; select preload based on duty cycle.
The Role of Engineering Consultation
Not sure what fits? Don’t guess. Consultation with machine designers or experts like our team at Jimi saves time and money—and stops headaches before they start. Our deep knowledge in linear motion engineering, strict manufacturing standards, and a full range of products help you match every preload and rigidity need. Still have questions? Explore our China Electric Cylinder Factory, get custom advice, or browse Industrial Automation Actuators for your exact industry challenges.
Conclusion: Engineering for Uncompromising Precision
If you’re after serious precision, preload and rigidity are non-negotiable. These two factors can make or break your accuracy, repeatability, and system quality. At Jimi, we blend experience, engineering know-how, and top component choices, so you never have to settle. Want your motion systems to work smarter, not harder? It’s time to get serious about linear guide design. Check out our full product range, download detailed specs, or reach out for technical guidance. Turn motion headaches into reliable, high-performance systems today.
FAQs about Linear Guide Preload & Rigidity
Q: What's the difference between accuracy and repeatability?
A: Accuracy is how close you come to the target every time. Repeatability is how closely you hit the same spot, regardless if it’s the target. High rigidity and optimal preload boost both.
Q: How do I know what preload class I need?
A: Check your machine’s load, speed, and required precision. For top accuracy, go heavier. For long life at moderate speeds and loads, medium usually works. Our experts can help—just ask.
Q: Can I adjust preload on an installed linear guide?
A: Some guides allow minor tweaks but, for most, preload is set during assembly. Swapping to a guide with a different preload class often gives a better result.
Q: Does preload affect the service life of a linear guide?
A: Yes, optimal preload can increase fatigue life. Excessive preload cuts life short due to heat and wear. Balance is key.
Q: What are signs of insufficient or excessive preload?
A: Too little? Backlash, noise, and vibration. Too much? High heat, stiffer movement, decrease in speed, or early bearing failure. If in doubt, consult the experts.
Ready to learn more about linear motion? Dive deeper with our Ball Screw Actuators, or ask us for custom solutions—Jimi is here to make every move the right one.