Gantry systems have become the backbone of modern automation. These big, boxy robots glide back and forth in factories and labs. They move with the type of precision you expect from a master craftsman—at speeds and forces no human could ever match. But behind that smooth motion lies a big challenge: how do you make every axis, every motor, and every part move as one? That is exactly what “sync control for linear modules in gantry systems” is all about.
Why Sync Control Matters: The Problem You Can’t Ignore
Picture a huge gantry robot carrying a delicate glass panel, a row of milk bottles, or an entire car door. If one side lags or pulls ahead, even by a hair, you risk disaster. The panel might crack. Bottles might topple. Welds might not line up. The system starts to skew—one side forward, the other catching up, causing vibration, extra noise, or, worse, breakdowns. Skew breeds wear, missed targets, slower cycles, and costly failures.
We at Jimi have seen it happen everywhere:
- In an electronics factory, chips misalign by just half a millimeter. That means a hundred components fail in a flash.
- A material handling gantry without proper sync? It binds, jerks, and soon grinds to a halt.
- Laser cutters miss their mark, wasting sheets of expensive metal.
Without real sync control, every task on a gantry becomes a gamble. Messy motion means short equipment life. It raises costs, causes downtime, and turns “precision” into a pipe dream.
The Agitation: When Small Errors Become Big Headaches
Still not convinced you need sync? Remember the last time you tried pushing a heavy bookshelf and one side moved ahead of the other. The whole thing wobbled, maybe even stuck or scratched the floor. With gantries, the stakes are much higher:
- Even tiny differences in motor speed or load throw the system out of line.
- Skewed motion leads to binding. It wears out linear guides, ball screws, and actuators.
- Vibrations shake loose precision parts.
- Over time, the accuracy everyone wants—gone.
According to industry studies, poorly synchronized gantries see linear guide wear increase by 25%, and motor life drops by 20%. Throughput in material handling lines dives by up to 18%. Plus, the final quality—whether it’s a car body, a printed circuit, or a 3D-printed part—suffers.
And here’s the kicker—these problems don’t just add up over the years. They hit fast. Within days or weeks, friction rises, cycle times slow, and costly service calls pile up. What’s meant to be the most reliable part of your production line turns into your weakest link.
The Solution: Sync Control That Makes Gantries Dance
Now, let’s flip the script. Imagine every motor and actuator moving in lockstep, every axis “knowing” exactly what the other is doing, making complex moves look easy. It’s not magic—it’s sync control.
The Building Blocks of Coordinated Motion
At its heart, sync control means every action is in tune. Here’s how we get there:
Core Principles
- Master-Slave Control: One axis (the “master”) sets the pace. All others (the “slaves”) follow its every move.
- Electronic Gearing: Each follower gets a digital nudge to match speed, position, and acceleration.
- CAM Profiles: Instead of just straight lines, we create complex, dynamic paths that can speed up or slow down in perfect sync.
- Cross-Coupled Control: Real-time feedback compares every axis so errors vanish before they start.
- Feed-Forward & Adaptive Control: These “smart” systems learn and compensate as conditions change, whether it’s a heavier load or changing temperatures.
Key Control Objectives
- Position Synchronization: Both sides arrive at the target together, every time.
- Velocity Synchronization: Smooth speed control means no jerks or stutters.
- Acceleration Sync: Corners, starts, and stops are gentle and sharp at the same time.
- Load Sharing: Forces balance out—no overworked motors or bent rails.
The Tech That Makes It Possible
You might think all this requires endless tinkering or wizard-level programming. But with the right technology, you gain control without the pain.
- High-Performance Motion Controllers: Think of them as orchestra conductors. Brands like Siemens, Beckhoff, or Rockwell coordinate real-time moves using dedicated chips (DSPs, FPGAs) or advanced PLCs.
- Real-Time Communication Protocols: Networks like EtherCAT, PROFINET IRT, and SERCOS III let pieces “talk” to each other instantly. You get split-second data across every axis.
- Precision Linear Modules & Actuators: Ball screws, linear guides, servo motors, and even zero-backlash linear motors keep mechanical slop at bay. Systems from trusted China Linear Actuator Manufacturer and others power true sync.
- Accurate Feedback Devices: Encoders (like those from Heidenhain or Sick) and resolvers provide position checks that are as precise as a micrometer.
Sync doesn’t stop at hardware. Modern software algorithms—PID control, cross-coupled loops, and safety interlocks—bring everything together.
Want even more detail? Explore solutions like our Ball Screw Actuators and Industrial Automation Actuators, which set the standard for accuracy and robustness in today’s automated lines.
Proof in Action: Real-World Gains from Sync Control
Still wondering if sync control is worth it? The numbers speak for themselves:
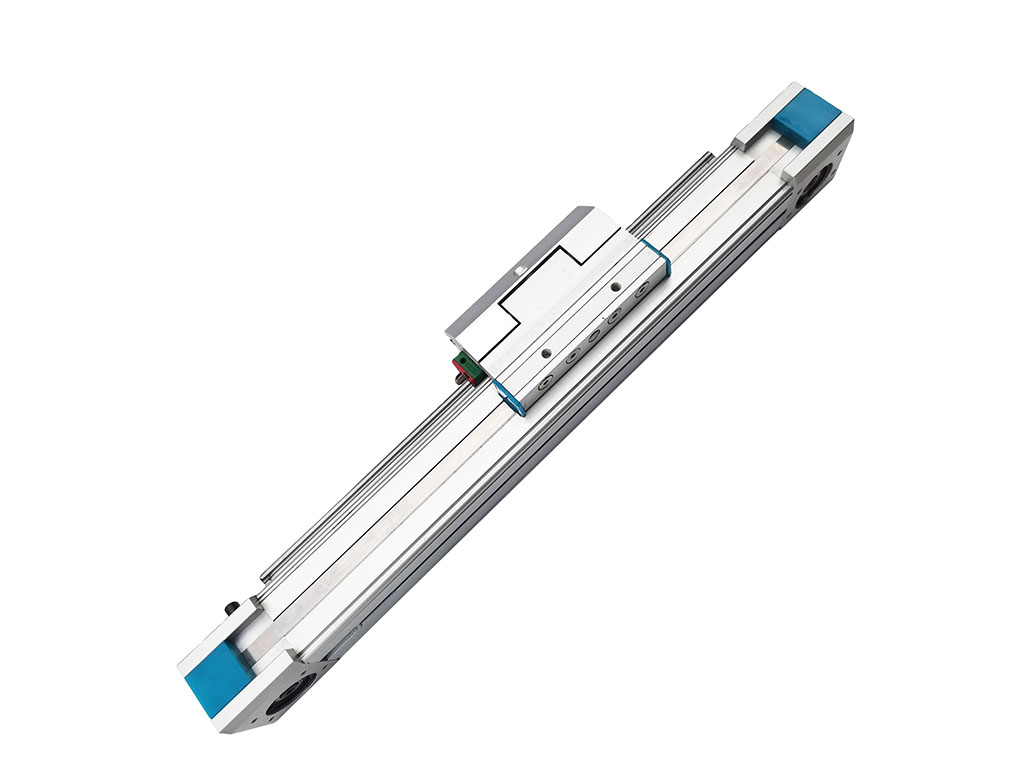
Application | Benefit/Improvement | Numbers Tell the Story |
---|---|---|
Electronics Assembly | Reduced skew & higher accuracy | Skew down by 90%, repeatability up 30% |
Material Handling | Faster cycles, less waiting | Cycle time drops 15–20%, throughput up 18% |
Laser Cutting | Fewer repairs, longer life | Guide wear down 25%, motors last 20% longer |
3D Printing | Lower bills, greener production | Power use during rapid moves down 10–12% |
Quality Inspection | Catch even the smallest defects | Path errors down 85%, vision catches more |
Automotive Assembly | Faster setup, less downtime | Setup time cut by 30% |
Viscous Dispensing | Smooth lines, fewer blobs | Resonance drops 40% |
Heavy Loads | Move more, break less | Payload up 10–15% |
We at Jimi have helped customers all over the world unlock these gains. When you use the right linear modules and real sync control, you boost not just speed and accuracy, but the life expectancy of every piece of your system.
Looking for inspiration? Check out our advanced Servo Motor Actuators—engineered to thrive in the harshest environments, from semiconductor labs to automotive pressing lines.
Where Sync Control Shines: Applications That Demand Perfection
You’re likely to find sync control hard at work in:
- Electronics assembly: Fast pick-and-place of microchips, where even a blink of delay means failure.
- Large-format additive manufacturing: Deposition of thin, even layers over wide surfaces.
- Automotive and aerospace assembly: Handling, welding, and fitting large, heavy or delicate parts.
- Life sciences labs: Automated pipetting and diagnostics need flawless step-by-step motion.
- Semiconductor manufacturing: wafer handling at speeds and precision that no manual system could match.
Curious about the complete stack? Industrial Linear Actuators handle everything from light duty tweaks to heavy payload transfers, all in synchronicity.
Best Practices: How to Get Sync Right—The Jimi Way
Sync control may sound complex, but some simple best practices go a long way. Here’s what to keep front-of-mind:
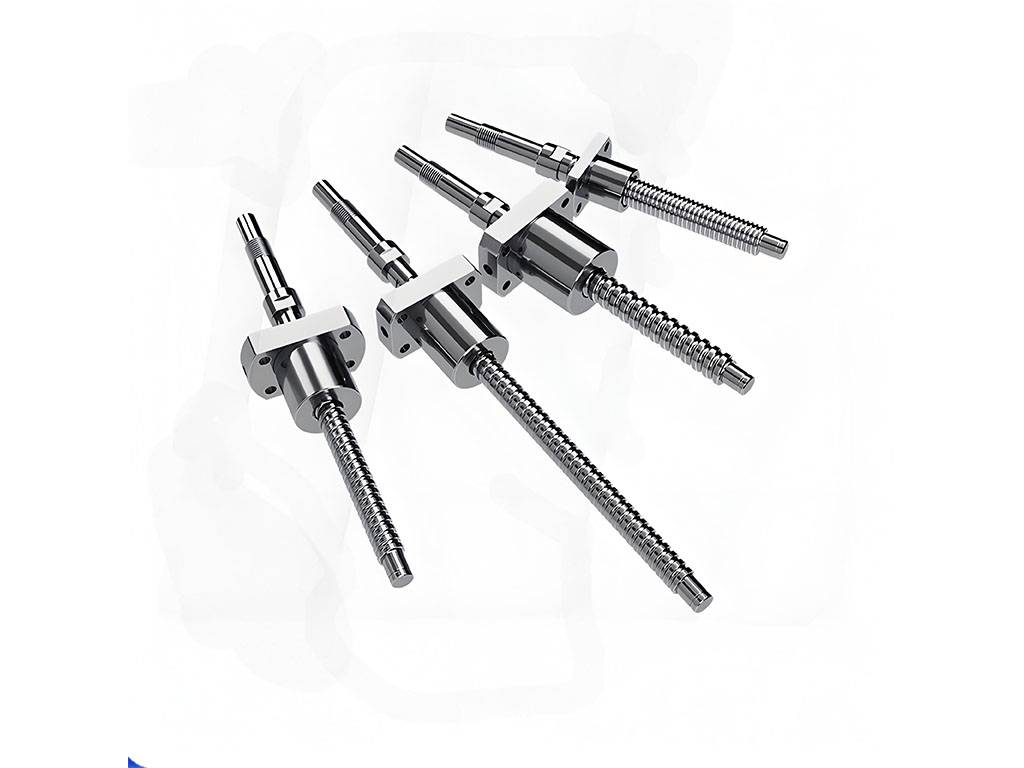
- Mechanical Design: Build rigidity and alignment into your gantry from day one. Use strong linear guides, tighten those cable runs, and pick brackets that hold their shape under stress.
- Control System Tuning: Spend time with PID loop tuning, take anti-windup seriously, and don’t ignore system resonance. It’s like tuning a guitar—finesse makes perfect harmony.
- Programming & Kinematics: Define your robot’s moves well. Plan for errors and recovery. Build in safety stops so a glitch won’t turn into a breakdown.
- Environmental Factors: Hot? Dusty? Vibrating? Design for those, too. Pick enclosures and protection ratings that match your real world.
- Rely on the Pros: Integration is tricky. Trust manufacturers and China Electric Cylinder Factroy partners that have “been there, done that.” Experience saves headaches.
For a closer look at rugged assembly options, see our Lifting Columns Actuators—they’re built to handle everything from ergonomic workstations to high-cycle factory robots.
Jimi Technology: Your Partner in Synchronized Success
At Jimi, we don’t just sell parts. We design, build, and fine-tune complete motion systems for global leaders in every industry. Our expertise in linear actuator synchronization, mechatronics, and real-time motion control makes us a trusted partner for anyone who depends on precision.
- Top Quality: Every actuator, guide, and control system passes tough tests. You get reliability you can trust, shift after shift.
- One-stop Solutions: From linear modules, servo drives, and encoders to smart controllers and rugged mounting options—we handle it all, including Actuator Controllers.
- Unmatched Support: Need help with startup, tuning, or troubleshooting? Our engineers are a call away, worldwide.
When it comes to gantry synchronization, tandem axis control, and high-accuracy gantries, no detail is too small for us. We offer not just components but insight, training, and troubleshooting, every step of the way.
The Future: Adaptive, Predictive, and Even Smarter
Don’t expect sync control technology to stand still. The latest trends are already shaping tomorrow’s factories:
- AI-driven adaptive sync: Systems learn and adjust in real time, adjusting force and speed to match new loads.
- Predictive maintenance and digital twins: Monitor system health, predict failures, and eliminate unplanned downtime.
- Connectivity with IIoT: Sync your gantry’s brain with every other system for even smarter automation.
Stay ahead with Jimi—the ones who know not just what’s coming, but how to put it to work for you.
Ready to Master Precision? Let’s Talk
You’ve worked hard to get your production running. Don’t let a simple sync error stall your whole operation or cut your product quality. We at Jimi have the hardware, experience, and know-how to take your gantry system to the next level of precision and reliability.
Visit us and discover the difference real expertise makes. Ready to build the perfect synchronized solution? Contact us today and let’s get moving in harmony.
Related Reading:
- China Linear Actuator Manufacturer
- Ball Screw Actuators
- Industrial Automation Actuators
- Servo Motor Actuators
- Lifting Columns Actuators
Table: Real-World Impact of Sync Control
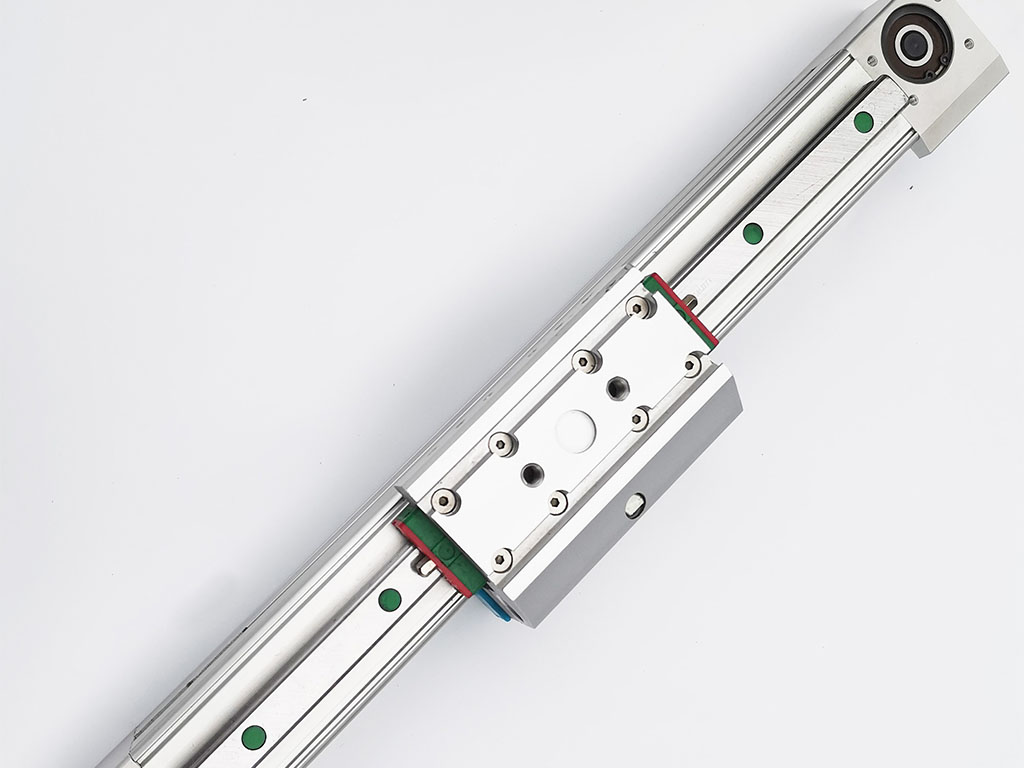
Industry/App | Main Benefit | Measured Improvement |
---|---|---|
Pick & Place | Precise placement, less skew | 90% skew reduction |
3D Printing | Smoother motion, saves energy | 10-12% lower power |
Laser Cutting | Fewer breakdowns, longer life | 20% longer motor life |
Automotive Weld | Faster setup, less downtime | 30% quicker launch |
Need help choosing the right actuator or controller? Check out our Actuator Controllers and let Jimi guide you from design to deployment—even for the toughest gantry robot jobs.
You're not alone. With Jimi Technology, your precision journey is in expert hands.