The old ways of moving goods don’t cut it anymore. You feel the pain every day, whether it’s in a pulsing assembly line that grinds to a halt, a warehouse conveyor that sends boxes bumping off target, or your energy bill that keeps climbing because machines just won’t run smart. Maybe you hear the groan of gears, see dust clouding bearings, or find yourself wincing each time downtime hits. You’re not alone. Operations managers, engineers, and business owners everywhere face the same, stubborn hurdles. Conveyor systems are the heart of every modern factory, warehouse, and fulfillment center—yet when they break down, so do profits.
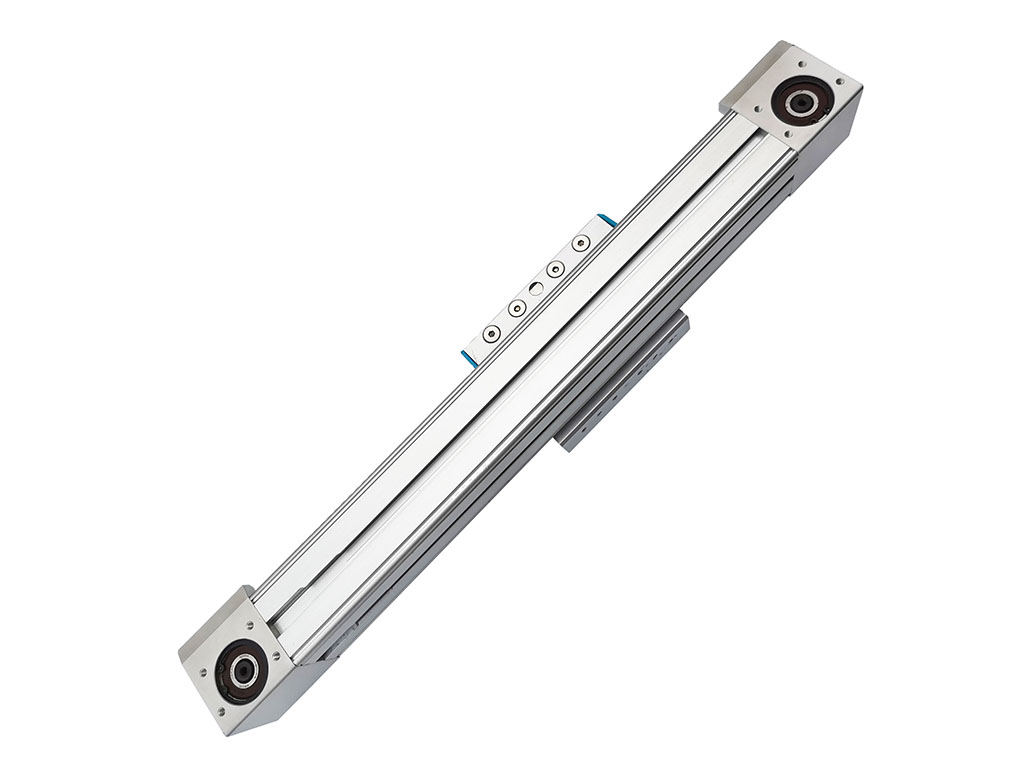
Think about it. Traditional conveyor tech has limits. Manual adjustments stop a line for minutes or hours. Belt slip and mechanical drag waste power. Even routine maintenance means more labor, more expense, more lost time. When a product’s knocked out of place or a shipment’s mis-sorted, you pay for it twice—once in wasted material, again in wasted trust with your customers. Maybe worst of all, when change comes—new products, bigger orders, faster turnaround—old lines just can’t keep up.
Every time you wait for a technician, worry over product quality, or face bottlenecks you can’t explain, you’re seeing the hidden cost of outdated conveyor systems. The market doesn’t wait. Neither should you.
Let’s dig into the root of this frustration. Why do so many conveyors fall short? The answer lies in old mechanisms: friction-heavy rollers, imprecise chains, and motors that don’t know how to use their power wisely. Each of them creates inefficiencies—the slow creep of wear and tear, the constant need for manual touch-ups, the friction that eats into your budget day after day. Energy leaks away. Product gets mishandled. Every stop-and-start saps throughput. And flexibility? Forget about it; most old lines handle just one product size or flow, so shifting gears is a headache.
There’s good news. A new breed of technology has thrown out those limits and given conveyor systems a fresh purpose: linear motion technology. We’re talking about electric linear actuators, precision linear guides, advanced bearings, and smart control systems that let your conveyor glide with the touch of a button. No more cranking by hand, no more guessing at alignment, no more crossing your fingers that a patch will hold. With linear motion, conveyor systems become agile, robust, and almost effortless.
Let’s spell it out. What exactly is linear motion technology (LMT)? Imagine a seamless movement along a straight track—no grinding, no jerks, no slip. Components like linear guides & rails provide a smooth platform for products, while electric linear actuators deliver push and pull with pinpoint control. We add in smart motors (servo and stepper types), ball screws for ultra-precise motion, and rugged brackets that handle heavy loads. Then tie everything together with brainy controllers for instant, repeatable action.
In simple terms, we’re trading old, clumsy mechanics for automated muscle that runs on pure efficiency. Why does this matter? Slide a product to a millimeter-precise stop every time. Sort at blazing speed. Keep the line running—day after day, year after year—with less grease, less trouble, less stress.
Now, what can this do for your operation? A lot, actually.
The Payoff: Why Optimization With Linear Motion Is A Game-Changer
- Higher Precision, Lower Waste: LMT lets products be sorted and positioned with up to 20x more accuracy (from ±1.0 mm down to ±0.05 mm). Gone are the days of misaligned packages or product jams. Precision conveyor movement means higher quality, less scrap, and fewer returns.
- Faster Throughput: Picture this: 30-50% more units per hour right out of the gate. That means lines that used to push 100 pieces an hour now sail past 130 or even 150. Why? Faster acceleration and deceleration, no drag, and perfect product placement.
- Much Less Maintenance: Components like sealed linear bearings and self-lubricating actuators run for years with barely a whisper of attention. Maintenance costs drop by 25-40%. Fewer breakdowns, less downtime, smaller repair bills.
- Energy-Efficient by Design: With friction almost gone, power savings add up fast. Some plants have slashed daily energy use by 15-25%. That isn’t just good for your wallet—it’s good for our world, too.
- Adapts On The Fly: Flexible, modular conveyor design means you handle any product, any job, any time. Changeovers that used to need hours now take minutes. No more limits, no more “that’s just the way it is.”
Don’t just take our word for it—the results are clear. Companies installing linear motion solutions report:
Benefit | Traditional Conveyor | With Linear Motion Tech |
---|---|---|
Throughput | 100 units/hour | 130-150 units/hour |
Energy Use | 50 kWh/day | 37.5-42.5 kWh/day |
Maintenance Cost | $10,000/year | $6,000-$7,500/year |
Downtime | 10 hours/month | 3-5 hours/month |
Scrap Rate | 2.5% | 0.5-1.0% |
Lifespan | 3-5 years | 7-10+ years |
Payback | N/A | 18-36 months |
Noise | 80-85 dB | 65-75 dB |
Take a packaging plant as an example. After switching to linear motors and automation actuators, they cut lost product by 80% and saw electricity bills take a nosedive. An automotive assembly line dropped unplanned downtime by more than half and doubled component lifespans. These aren’t exceptions—they’re the new rule when you use the right tools for the job.
So, how do you bring this power to your operation? Let’s break it down:
1. Assess Your Needs
Start with a deep look: Where are the bottlenecks? Where do parts jam, or is cleanliness critical (think food or pharma lines)? Do you want more speed, accuracy, or just to cut costs? Getting numbers—on throughput, maintenance, errors—sets the stage for real change.
2. Select The Right Components
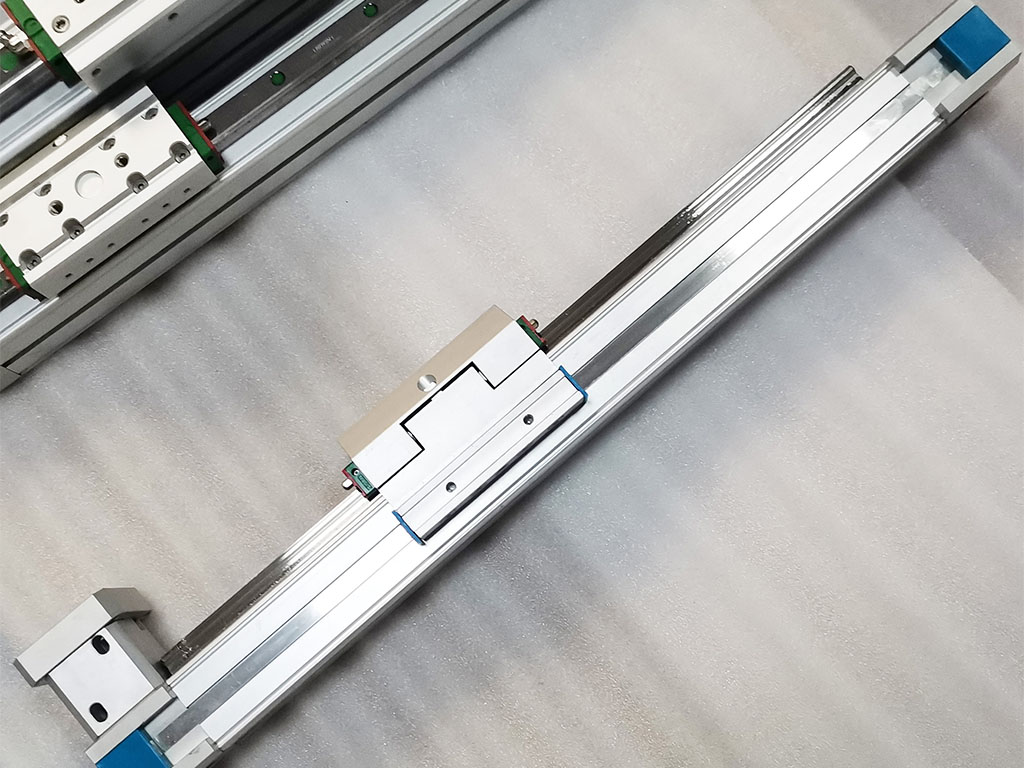
Choose from heavy-duty or light-duty options; electric or hydraulic linear actuators for different force needs; servo or stepper motor actuators for the control you crave. Modular pieces mean you build just what you need—nothing more, nothing less.
If you’re unsure, partner with a China Linear Actuator Manufacturer like Jimi. Our team helps you pick, size, and source each conveyor upgrade for your specs.
3. Integrate And Test
Good news—linear motion tech doesn’t mean gutting your old line. Most components retrofit right in. We help program the controls, run simulation tests, and make sure everything meets your goals before launch.
4. Maintain And Optimize
Set up regular checkups using IoT sensors and data dashboards to track performance. Most issues get flagged before they become headaches. Continuous improvement means your system gets smarter with every cycle.
Let’s not forget the future. Conveyor systems powered by linear motion are built for what’s next: automation, robotics, smart factories, and AI-powered diagnostics. Imagine lines that talk to robots, detect their own problems, and manage changeovers without stopping the flow. That’s not just a dream—that’s where Industry 4.0 is heading, and LMT is the backbone.
Why pick Jimi for this journey? Experience matters. We at Jimi Technology have delivered thousands of automation systems worldwide, working alongside leaders like Siemens, Mitsubishi Electric, and Universal Robots. We don’t just sell parts. We design solutions. Our electric cylinders, actuators, and linear guides pass strict ISO 9001 tests; our factory is built for speed and scale. Our customers trust us to deliver reliable upgrades and stay by their side for every project—big or small.
What sets Jimi apart? Simple:
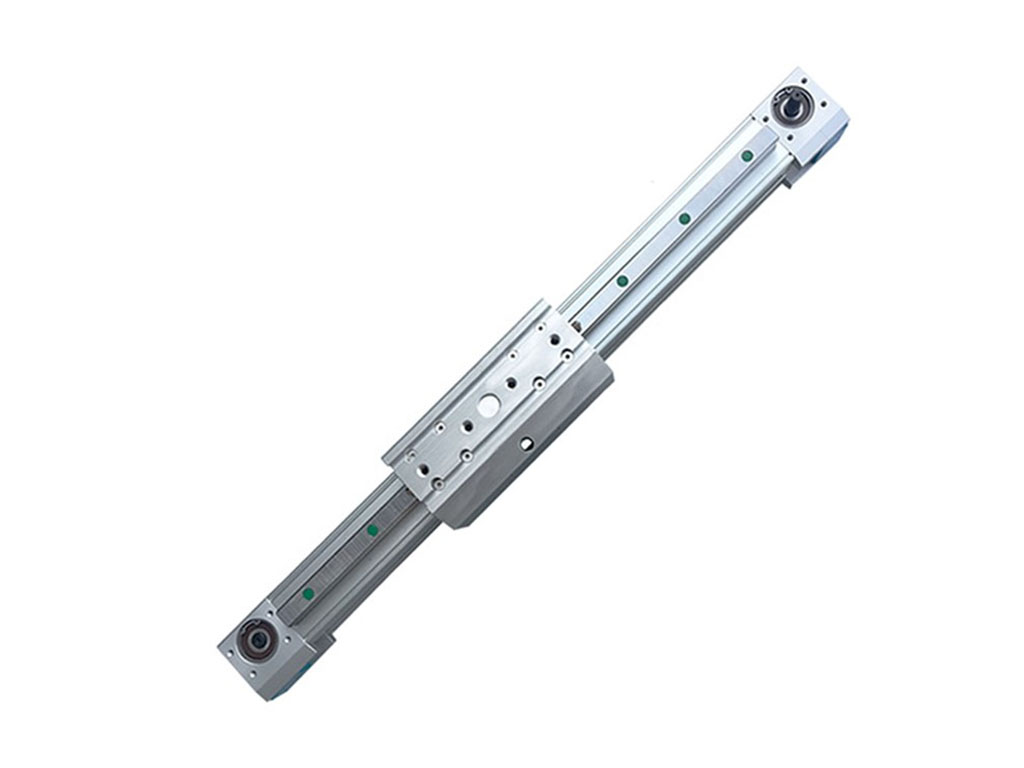
- Top-grade materials for long-lasting gear
- Custom linear actuator options for unique challenges
- Quick, expert support and advice
- One-stop shop for components, accessories, and controllers
Start your upgrade with confidence. Building a conveyor from the ground up? Start with China Electric Cylinder Factory for guidance. Need something rugged, like heavy duty actuators? We know how to deliver. Looking for speed or silent operation? Try high-speed or quiet linear actuators. It all starts when you reach out to our team.
Ready to transform how your factory moves? Set aside the frustration and take the first step toward a smoother, faster, and more flexible future. Go beyond the belt—choose linear motion technology and see your conveyor system evolve. Connect with the experts at Jimi Technology now. Together, we’ll build the backbone for your business to grow, adapt, and win.
Unlock precision. Cut costs. Increase uptime. The best conveyor you’ll ever own is the one that moves with Jimi at its core.
Your world runs better when your conveyor does, too. Make the smart move—make it with Jimi.