Maximize Uptime: Comprehensive Guide to Protecting Linear Guides in Harsh Industrial Conditions
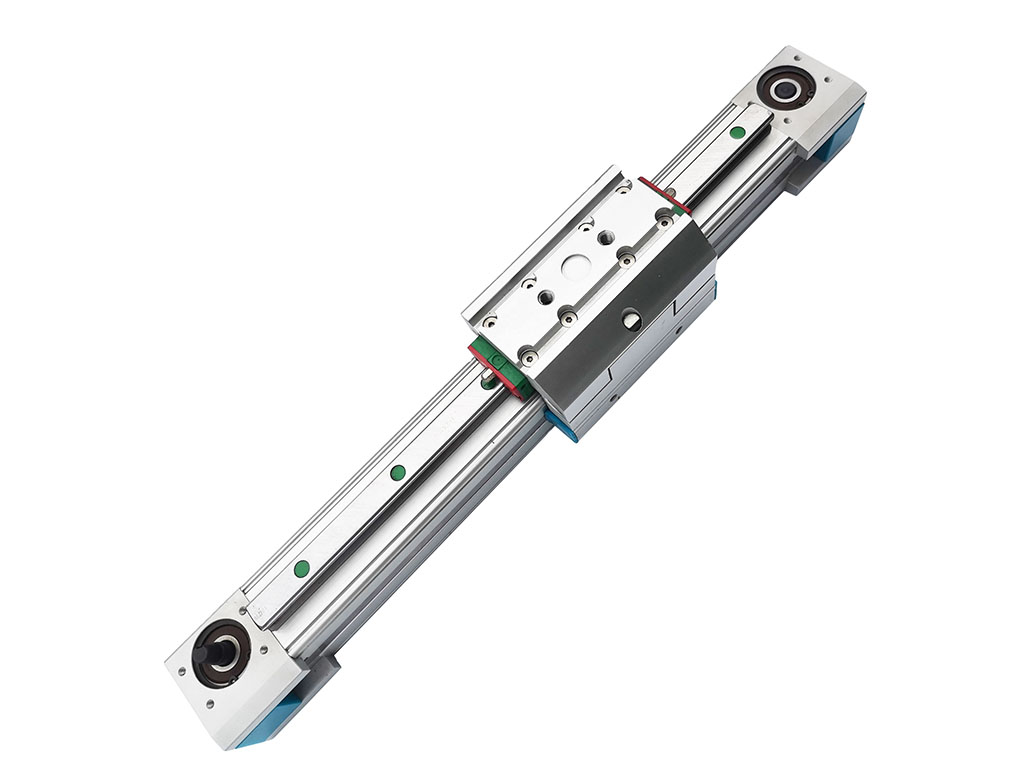
When machines go down, production slows, costs shoot up, and headaches multiply. If you’ve ever waited for a crucial system repair or seen profits leak away as a dust-clogged guide rail halts your line, you know what’s at stake. Harsh industrial conditions turn strong equipment into fragile bottlenecks. But it doesn’t have to be this way. Protecting linear guides is your first step to keeping things running smoothly—no matter what your environment throws at you.
Why Linear Guides Matter in Industrial Operations
Linear guides are the backbone of smooth motion in almost every machine. They help move heavy loads with precision, speed, and minimal friction. From robot arms to cutting tables and conveyor belts, if something slides in your factory, linear guides are at work. These small but mighty components are everywhere: machine tool builders, mining operations, pharmaceutical manufacturing, and even the food and beverage processing industries rely on them every day.
When these guides fail, the numbers tell the real story:
- 20-30% of all machine downtime in manufacturing links back to bearing failures—linear guides are a type of bearing system.
- It’s not just production you’re losing. You’re also paying for repairs, parts, and the hours your maintenance crew spends babysitting tired equipment.
Neglected linear guides in extreme environments don’t just cost you money; they can cost you your reputation, too. Downtime means missed deadlines, unhappy customers, and a business that’s always playing catch-up.
What Harsh Industrial Conditions Do to Linear Guides
Particulate Contamination
Dust. Metal chips. Wood shavings. Abrasive particles. If you grind, saw, mill, or cut, you’re already fighting this battle. Dust works its way into grooves and balls in your linear rails. Abrasives cut into the surfaces, making the ride rough and loud. Over time, the guide wears out early—think five years lost in just one.
Industries at risk? Machining, woodworking, mining, and steel production plants face these threats every day. The solution isn’t to stop producing dust but to stop it from getting in where it hurts.
Moisture and Liquid Ingress
Water and other liquids are troublemakers. In food & beverage, pharmaceutical, and chemical processing facilities, frequent wash-downs, coolants, and high humidity eat away at metals and ruin lubricants. Corrosion sneaks in, joints seize, and pretty soon you’re calling for parts.
Did you know a 10°C rise above optimum temperature in your lubrication halves its service life? Imagine what constant washdowns or condenser leaks do.
Chemical Exposure
Factories run on much more than elbow grease. Chemical processing plants, plating facilities, and galvanizing operations expose equipment to aggressive acids, alkalis, and solvents. The wrong material choice soon shows: seals fail, metal pits and flakes, lubricants break down, and motion gets sticky. You lose precision fast.
Extreme Temperatures
From hot foundries to freezing cold storage, wild swings in temperature wear linear guides down. High heat changes how lubricants flow and makes metals expand. In the cold, lubricants thicken up, and materials crack or get brittle. If your guides can’t handle the swings, expect early breakdowns and loss of accuracy.
Mechanical Stress
Heavy loads, rapid speeds, vibrations, and sudden shocks stress linear guides day-in and day-out. If you run robotics, material handling equipment, or automated assembly lines, your linear guides carry the weight of production. When stressed, these guides can misalign or break. Small misalignments lead to big headaches later.
Proven Strategies and Solutions for Rock-Solid Linear Guide Protection
You don’t just need band-aids. You need a solution that matches your exact challenge. Let’s talk about the tools and techniques that keep your guides running—no matter how tough the environment.
Physical Barriers: Your First Defense
Wiper Seals and Scrapers
Think of wipers and scrapers as the windshield wipers of your machine. They push away dust, chips, and grime before it can slip inside. Made from tough materials like NBR (nitrile rubber), Viton (FKM), and polyurethane (PU), wipers can handle sharp chips or aggressive chemicals. Go for dual-lip wipers if you need the tightest seal or single-lip for less drag.
Bellows and Folded Covers
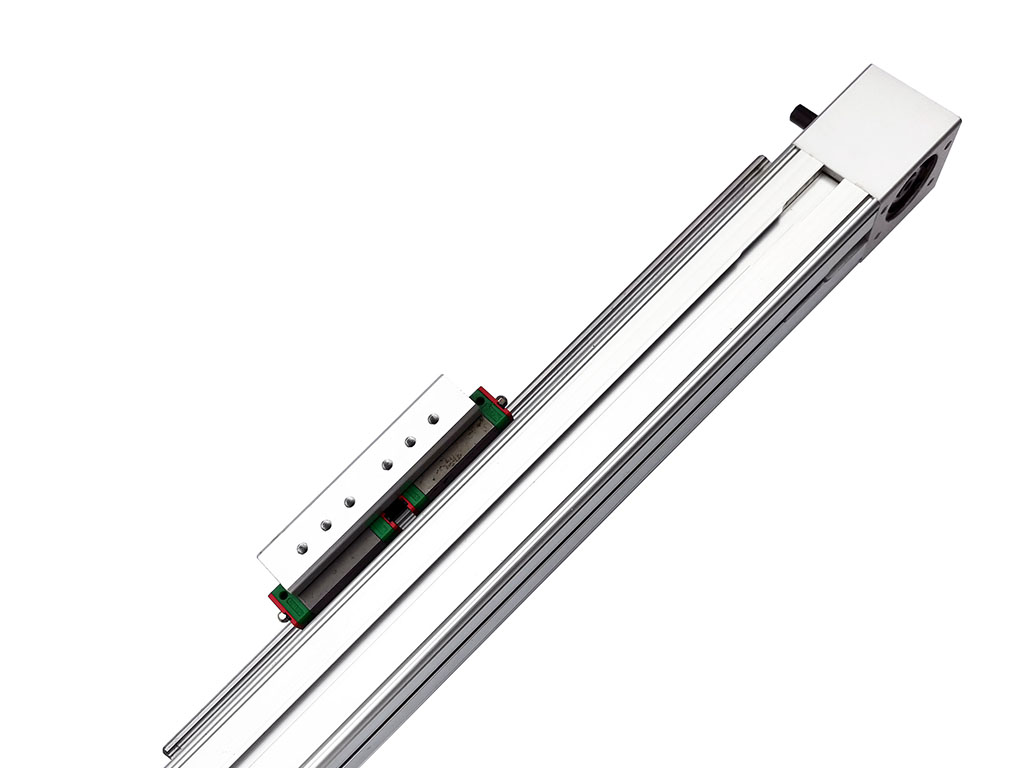
These accordion-style shields flex and stretch as your machine operates. They’re perfect for stopping large debris or water splashes cold. You’ll find fabric or elastomer-coated options for different environments. They’re a must in woodworking or stone cutting, where big chunks fly.
Telescopic Steel Covers
Nothing matches the brute strength of telescopic steel covers in high chip, high-heat industries. Millwork, steel factories, and heavy machinery swear by them. They shrug off hot, sharp debris while enclosing your most critical parts. Less mess means less downtime.
Enclosed Linear Modules and Integrated Protection
For the ultimate shield, pick fully enclosed modules. Some are IP-rated (look for IP69K if you handle washdowns or caustic cleaners). Integrated systems seal every entry point and offer peace of mind where contamination is constant.
Guide Rail Plugs and End Seals
Don’t let the small stuff trip you up. Plugs and end seals fit into mounting holes—places particles love to sneak in. Seal these and you’ll prevent silent, slow buildup that leads to sudden failure.
Lubrication Management: The Lifeblood of Linear Guides
Picking the Right Lubricant
Grease or oil? It depends. Grease stays put and works for upright, open guides. Oil flows and suits faster, enclosed systems. But don’t stop there. You’ll need specialized lubricants for high-temperature, water, or even food applications. If it’s got to be safe for a salad, go food grade.
Automated and Centralized Lubrication Systems
Manual greasing is hit or miss. Automated systems deliver just the right amount where and when it’s needed—even inside hard-to-reach modules. That means less friction, longer life, and fewer sticky problems.
Lubrication Schedules and Monitoring
More isn’t always better. Over-lubrication creates sludge. Too little and things overheat or seize. Smart schedules, paired with monitoring (like predictive maintenance sensors), help you hit the sweet spot.
Material Selection and Surface Treatments for Better Durability
Corrosion-Resistant Materials
Stainless steel guides (304 or 440C) thrive where moisture is everywhere. For surfaces that shrug off rust or acids, chrome plating, black oxide, or tough ceramic coatings are your friends. Every upgrade you make means fewer future replacements and repairs.
Hardened Surfaces
Wear resistance isn’t just for show. Specialty-hardened surfaces or coatings lock out abrasion and chemical attack. They’re a smart investment in factories with lots of grit or harsh sprays.
Environmental Controls and System Design
Positive Air Pressure Systems
A little air goes a long way. Blow filtered air around your guides to drive away dust in cleanrooms or electronics production.
Strategic Machine Enclosures
Put your linear motion components behind enclosures. Barriers isolate them from outside threats and can also reduce vibration.
Drainage and Smart Sealing
Water will always find a way. Smart design drains off pooling liquids and seals vulnerable spots. A little extra thought prevents a world of problems.
Maintenance Best Practices for Longevity
Don’t wait for disaster. Make these habits part of your maintenance playbook:
- Inspect Regularly: Catch issues before they cost you. Look for wear on wipers, seals, or any sign of sticky movement.
- Clean for the Contaminant: Use dry brushes and compressed air for dust. Wipe with approved solvents for chemicals or oil.
- Prompt Repairs: Replace worn seals, damaged covers, or misaligned guides at the first sign of trouble.
- Train Your Team: Make sure everyone understands the basics—from cleanliness to proper lubrication. A little know-how goes a long way.
Fact: In many factories, up to 40% of maintenance time goes to chasing problems from under-protected guides. If you’d rather fix issues once than forever, prioritize protection.
The ROI of Proactive Linear Guide Protection
Let’s run the numbers. With the right protection:
- You can extend guide lifespan up to five times in dusty places. That’s fewer purchases, swaps, and calls for emergency help.
- You’ll cut downtime and surprise repairs.
- Your team can focus on fine-tuning production, not firefighting breakdowns.
- And here’s the kicker—a 150-300% return on investment within two years is standard after installing advanced protection systems.
If you work in food or pharma, you’ve got no wiggle room. Only fully protected, IP69K-rated, food-grade guides keep you compliant. For everyone else, less contamination means less waste, more uptime, and a reputation as a reliable supplier.
Why Industry Leaders Trust Jimi for Linear Guide Solutions
We’ve seen it all at Jimi Technology Co., Ltd.. Our years building high-performance automation systems, from Electric Linear Actuators to Linear Guides & Rails, have taught us this: The right mix of protection, care, and expertise turns a trouble magnet into your productivity powerhouse.
We don’t just ship parts. We help you design, build, and maintain complete solutions:
- Custom guide rail protection for every condition—from wet washdowns to hot, gritty steel shops
- A full line of Waterproof Linear Actuators, sealed modules, and specialized accessories for extreme duty
- Industrial Linear Actuators and Ball Screw Actuators that stand up to relentless cycles
- Knowledge, support, and training that help your team do more, worry less, and sleep better at night
Our global clients—from automotive industry giants to small-batch makers—count on us for every project. If you’re stuck with downtime, tired of endless fixes, or want to boost efficiency, we’re the partners who get it done. We have the know-how, the track record, and a relentless drive to help you succeed.
Ready to Move from Crisis Mode to Control?
You don’t want to spend your next maintenance window unplugging jammed guides or explaining late shipments to your boss. You want stable production, a safe and reliable workspace, and numbers that trend up, not down. You want resilience, not risk.
Reach out to our expert team for advice. Explore our range of durable, sealed, and smart actuator and guide solutions, like Stainless Steel Actuators for corrosion resistance or Actuators with Position Feedback for extra precision.
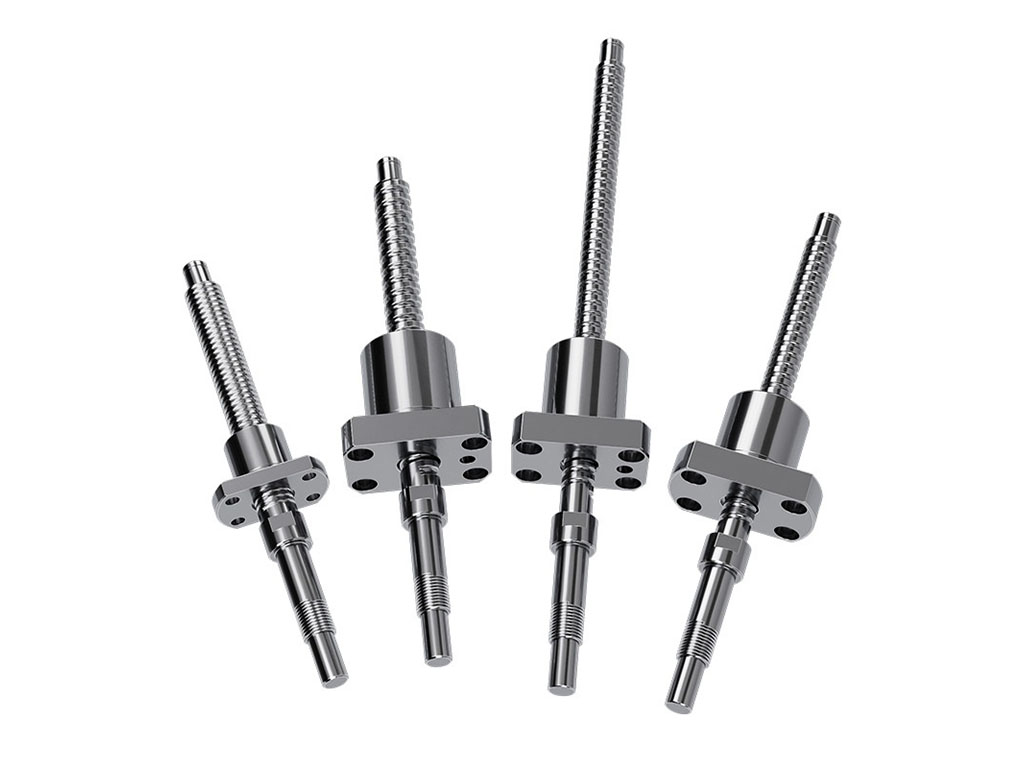
In a Nutshell
Protecting linear guides pays off faster than you think. It means less downtime, fewer headaches, longer equipment life, and better profits. Stop fighting the same battles and start winning with smarter protection. Trust Jimi, the experts who care as much about your uptime as you do.
Get started now. Let’s build something that lasts—together.