Modern manufacturing is always on the move. You watch robots solder, weld, or sort with perfect focus – right up until they hit their limit. The robot’s arm stretches but can go no further. That unfinished seam. That pile of parts just out of reach. Frustration, right? Some factories try to solve this with extra robots, expensive new machines, or more workers. The result? A patchwork of costs and lost space.
Every day, you face the challenge of getting more work done with limited space and time. Operators run from machine to machine. Workpieces line up, waiting for their turn. The robots do their best but can only reach so far. You lose time moving, lifting, and loading. Cycle times creep up. Throughput suffers. It feels like you’re stuck, boxed in by the very machines that were supposed to set you free.
Now, let’s take a giant step out of that box.
The 7th Axis Changes Everything
What if you could make your robot glide from one end of the shop to the other? What if one robot could handle tasks in five, ten, or even twenty places without breaking a sweat? That’s where the robotic 7th axis—a linear module—comes in.
A linear module is a heavy-duty track with a powered carriage. You mount your existing robot on this carriage. At the press of a button (or a tap on your controller), your robot rides this axis, zooming along the rail. Suddenly, your robot’s workspace doesn’t just grow—it explodes.
With a 7th axis, your robot’s effective reach increases 200–500%. You can serve multiple stations, weld or cut along ten-meter seams, tend a row of CNCs, or work on massive assemblies. Instead of buying three robots, get one moving robot that does it all.
Simple idea, right? Yet the impact is enormous.
Why Add a 7th Axis Linear Module?
- Dramatic Workspace Expansion
- Your robot can now reach far past its fixed base.
- Work on several machines, conveyor positions, or huge parts without moving the robot by hand.
- Use the floor smarter—why fill the shop with seven robots when one smart robot on a rail gets it done?
- Flexibility and Versatility by Design
- Products change, stations move, part sizes increase or decrease – no problem.
- The linear track lets robots switch between jobs smoothly and keeps your shop future-proof.
- No need for complex cell redesign or new robots with every shift in demand.
- Real Productivity and Efficiency Gains
- Robots move fast—no more manual transfers or waiting for a second machine to start.
- With the robot covering more ground, you cut idle times and maximize use.
- Real-world stats show cycle times can drop 15–25% and hourly output can jump 20–40% when you use a 7th axis.
- Smart Investment—Better ROI
- Running a single, flexible robot on a linear module often costs 30–60% less up front than two or three fixed robots.
- You get more done but don’t have to buy more robots.
- Fast ROI: most see payback in 12–24 months.
Still not convinced? Here’s how it works.
How Do Linear Modules Give Robots a 7th Axis?
Think of your robot as a skilled worker with strong arms but stuck on a small island. The linear module is the bridge, letting your robot travel across the whole factory.
The Main Parts
- Linear Tracks/Rails: These precision-ground rails serve as the road, designed for loads big or small.
- Carriage (or Saddle): Heavy-duty, stable, this is the moving “platform” that carries the robot.
- Drive System: Options include rack-and-pinion, belt-driven, or high-precision ball screw drives—all with servo motors for smooth, accurate motion.
- Motors & Gearbox: These combine for controlled, fine-tuned moves even at high speeds.
How Do You Control It?
- The linear module connects to your robot controller as an external axis.
- Robot and module move together in perfect sync—like a dancer gliding while moving their arms.
- You program points and paths that let the robot work new areas. There’s less programming work than you’d think, and most major robots support these tracks out of the box.
Install it How You Need
- Tracks can go on the factory floor (floor-mounted), overhead (gantry systems), or even mounted to walls or platforms for unique tasks.
- Got limited floor space? Go vertical. Need maximum range? Go long and low.
Looking for high-precision ball screw linear modules? Need help with servo linear actuators or industrial robot tracks? We’ve seen it all and built it all—right here at China Linear Actuator Manufacturer.
Where Do 7th Axis Linear Modules Make the Biggest Impact?
Let’s get specific. Here are the real-world jobs transformed by a robotic 7th axis:
- Large-Scale Welding & Cutting
Welding a ten-meter steel beam in a single shot used to be a nightmare. Today, one robot on a linear track handles seams on automotive chassis or aircraft fuselage sections. Aerospace makers saw a 95% drop in manual welding hours after switching to this method. Weld quality improved by 20%. Fewer failed parts. Fewer tired welders.
- Material Handling & Palletizing
Robots move heavy parts or stack pallets across long distances. No longer does someone have to push a cart back and forth, risking bumps and strain. Robots on tracks feed and unload multiple machines, pick jobs from storage, and carry large or awkward loads—all in a single sweep.
- Machine Tending
Serving multiple CNCs used to mean operators darting from one spot to another. A modular robot on an eight-meter track now handles three CNCs, one inspection station, and keeps output climbing. One auto parts supplier ran an unmanned third shift and boosted output by 35%.
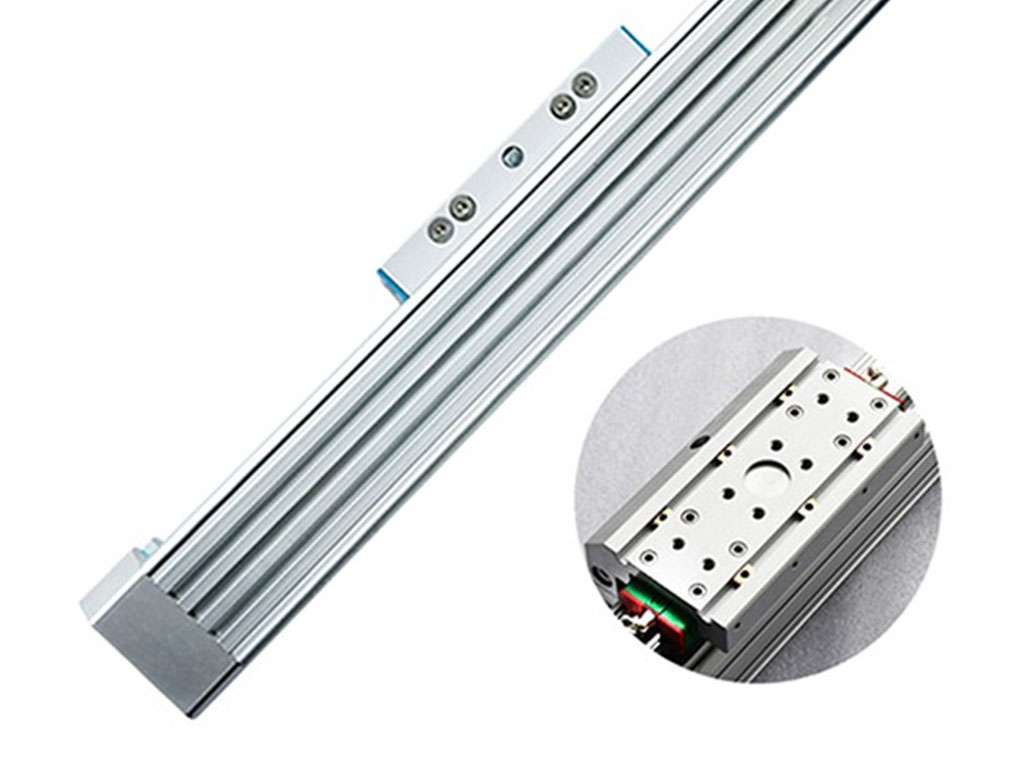
- Automated Assembly
Large frames, vehicles, or appliances demand flexibility. With a 7th axis, your robot can assemble complex structures without constant repositioning or manual handling.
- Painting & Dispensing
Apply coatings or sealants to oversized surfaces in one pass. No breaks, no missed spots, and no worker having to suit up for difficult jobs.
- Quality Inspection
Large components or many small parts spread across a wide area? No sweat. Robots on linear tracks check every corner, scan with laser accuracy, and spot issues right away.
- Additive Manufacturing (Large Format)
Robotic 3D printing expands to giant molds or parts. Instead of being trapped in a box, the robot’s print area grows to the job’s true size.
Want to see more? Check our detailed pages on track actuators or browse high-power servo linear actuator factories.
Technical Considerations: What Should You Look For?
Every shop and process is different. Here’s what experienced automation managers focus on:
- Payload Capacity: Can the track handle your robot, end effector, and workpiece together?
- Stroke Length: Choose rails long enough for your parts, but not so long you waste precious floor space.
- Accuracy & Repeatability: For tight-tolerance work, pick linear modules rated to ±0.05 mm or better. Reliable positioning keeps quality high.
- Speed & Acceleration: Match the track’s abilities to your process—some jobs need smooth, slow moves; others need speed.
- Operating Environment: Is your line hot, dusty, or needing frequent washdowns? Get tracks rated for tough environments (up to IP65 protection).
- Maintenance: Fewer breakdowns mean fewer headaches. Look for industrial linear actuators with built-in lubrication and simple service access.
- Safety: Integrate stops, sensors, and circuits to avoid accidents. Our kits support robot safety standards and collision avoidance.
If you want more tech details, check out our collection of linear guides & rails, or explore electric linear actuators for your next upgrade.
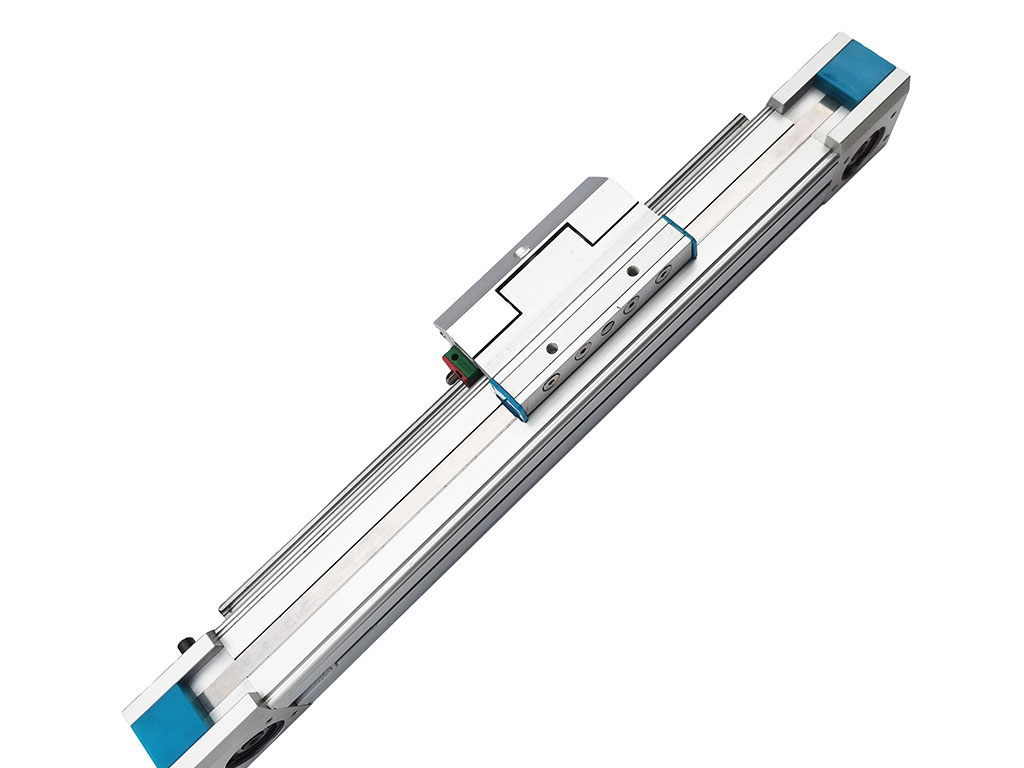
Why Trust Jimi Technology for Robotic Linear Modules?
At Jimi Technology, we do more than sell products. We build smarter movement and flexibility into your production. Our team marries real-world expertise with proven engineering and decades of manufacturing strength. Every linear module and actuator comes backed by strict quality, tested performance, and support that stands with you from start to finish.
Whether you need heavy-duty linear rails, quick-change tracks, or smart control kits, we help you unlock every inch of your workspace. We’ve helped aerospace, automotive, and general industry leaders achieve:
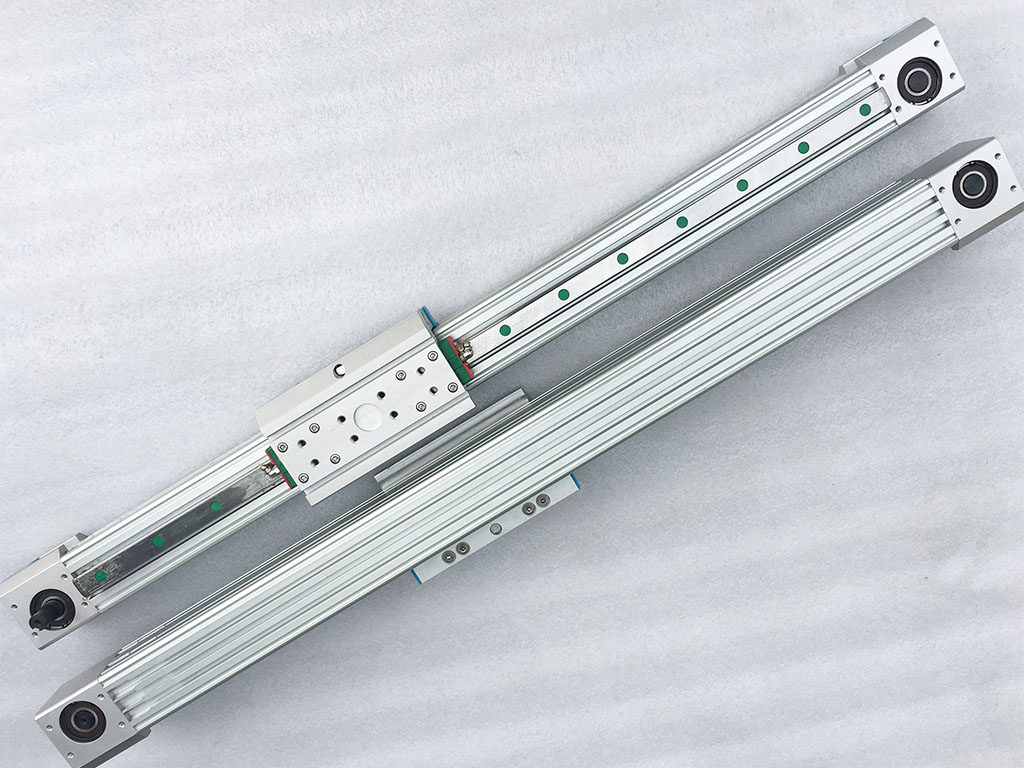
- Up to 50% reduction in floor space compared to older methods.
- Fast deployment for new parts or stations.
- Peace of mind, knowing their robots won’t get left behind when production changes.
Don’t let limits slow your robots, your people, or your growth. Extend your reach with Jimi’s automation solutions. Start building your flexible, future-ready automation line now.
The Next Step
Want to transform your robot’s workspace? It starts with a single, smart move. Visit China Linear Actuator Manufacturer for the best in linear modules, servo motor actuators, and more. See why leaders trust Jimi for solutions that grow with you.
Stop fighting for reach. Start working smarter. With a 7th axis linear module, your robots do more, your floor shrinks, and your output grows—every single shift. The future of manufacturing isn’t about more machines. It’s about smarter, longer, and wider movement. And it’s ready for you, today.