The Critical Role of Sealing in Automotive Manufacturing: Why Perfection Matters
Picture this: a car speeds down the road during a rainstorm. Inside, it’s quiet and dry. That peace is thanks to perfect sealing. Seals keep water, noise, and dust out. They lock in heat or cold. They even keep important electronics safe. Sealing touches every part of a car—body, engine, transmission, and electric batteries.
When sealing goes wrong, the problems stack up quickly. One tiny leak can cause rust, electrical failures, or noise. These troubles hit your customers and brand hard. Recalls and unhappy buyers can cost millions. Quality is everything in car building. Good sealing is non-negotiable.
The Limitations of Legacy: Why Traditional Sealing Methods Fall Short
Let’s look at what’s been used for decades. Pneumatic systems use air to drive pistons. Hydraulic systems use oil. At first, these methods seem fine, but cracks show fast.
With pneumatic systems, air compresses. That makes motion less stiff. Sometimes it feels like slamming a hammer when you want to tap a nail. You get jerky movement, not smooth precision. Force control? Limited. Accuracy? Sometimes you only find out you’re off after it’s too late. Plus, air compressors run all day, wasting power and blowing up your energy bills.
Hydraulic systems can move big weights, but they leak oil, need tons of upkeep, and just don’t give fine control at low forces. Changing temperatures mess with oil, too. Both old-school methods often mean inconsistent bead lines, misplaced gaskets, and poor seals. You get more scrap, mistakes, and expensive rework. That’s not good for your bottom line or your customer’s trust.
Introducing the Game-Changer: How Servo Cylinders Revolutionize Sealing
Here’s where things get exciting. Servo cylinders—also called electric cylinders or electro-mechanical actuators—flip the script. Think of them as smart pistons. Instead of pushing with air or oil, they use an electric motor and a precision drive (such as a ball screw). You control them with a digital signal, not a pressure valve.
A servo cylinder knows exactly where it is. It uses a feedback system—imagine a smart tape measure and scale in one. You can set and change position, speed, or force instantly. Every button press moves the actuator smoothly and precisely. No more guesswork.
Digital beats analog. That’s the heart of it. Pneumatic and hydraulic systems are like painting with a broom. Servo cylinders are like drawing detailed lines with a fine tip marker.
Unlocking Superior Sealing Quality: Key Advantages of Servo Cylinders
Unparalleled Precision and Repeatability
Servo cylinders shine here. They reach positioning accuracy down to ±0.01 mm. Need to repeat the exact motion a thousand times? No problem. Each stroke matches the last. That’s the kind of accuracy you want for applying adhesive beads or seating gaskets.
Dynamic Force and Position Control
One big upgrade: you can change both force and position on the fly—even during a single stroke. Want gentle pressure at the start, then a hard press at the end? It’s easy. Great for materials that need special handling. For example, delicate seals that squish if you push too hard.
Enhanced Quality Control and Defect Reduction
With this accuracy, you get fewer leaks, voids, or uneven applications. Say goodbye to most rework and scrap. First-pass yield goes up. Customers notice the improvement. Warranty costs and complaints drop.
Increased Throughput and Cycle Time Optimization
Speed matters. Servo cylinders move in and out faster. Acceleration and deceleration are sharp and smooth, so cycle times go down. You can even reach several positions in one shot—no waiting or extra steps.
Energy Efficiency and Environmental Benefits
Here’s a win for the finance and green teams. Servo cylinders only use energy when they’re moving or holding a load. No wasted power. None of the “always-on” waste from compressors or hydraulic pumps. You lower your power bills, reduce noise, and say goodbye to messy oil leaks.
Fact: Electric cylinders (servo cylinders) can deliver up to 80% energy savings compared to pneumatic cylinders, especially when the machine must hold positions or run at changing loads. (Festo Energy Efficiency White Paper)
Transformative Applications: Where Servo Cylinders Excel in Automotive Sealing
Precision Adhesive and Sealant Dispensing
Servo cylinders give you perfect, consistent bead width and volume. Even on weird shapes or tight corners, there are no drips, stringing, or missed spots. This is crucial for bonding windshields, sealing body panels, and applying adhesives that keep cars safe and quiet.
Automated Gasket and O-Ring Placement
No one likes a pinched or misaligned gasket. Now you get exact placement and controlled compression every time. This reduces mistakes for engine, transmission, and drivetrain seals. Precision means less scrap and fewer leaks.
Battery Pack Sealing for Electric Vehicles (EVs)
In EVs, battery packs are mission-critical. Seals need to be perfect for safety, thermal management, and to keep out water. Servo cylinders can handle the tightest tolerances that new electric cars demand. As EVs take off, this precision becomes a must-have.
Sound Deadening Material Application
Tired of noisy rides? These actuators help place foam and patches right where they need to go. Getting this right means a quieter car and happier drivers.
Press-Fit Assembly with Integrated Sealing
Joining two pieces where a seal forms at the same time? Servo cylinders add just the right push. You get a strong fit and a perfect seal—think bearing installations or bushings that keep oil in and dirt out.
Implementing Servo Cylinder Solutions: Considerations and ROI
Integration Challenges and Solutions
Switching to servo cylinders is not magic—you need to plan. These actuators talk to control systems like PLCs or motion controllers. Sensors may get an upgrade, too. Staff will need training, but modern systems are easy to learn. Smooth integration means your line runs even better.
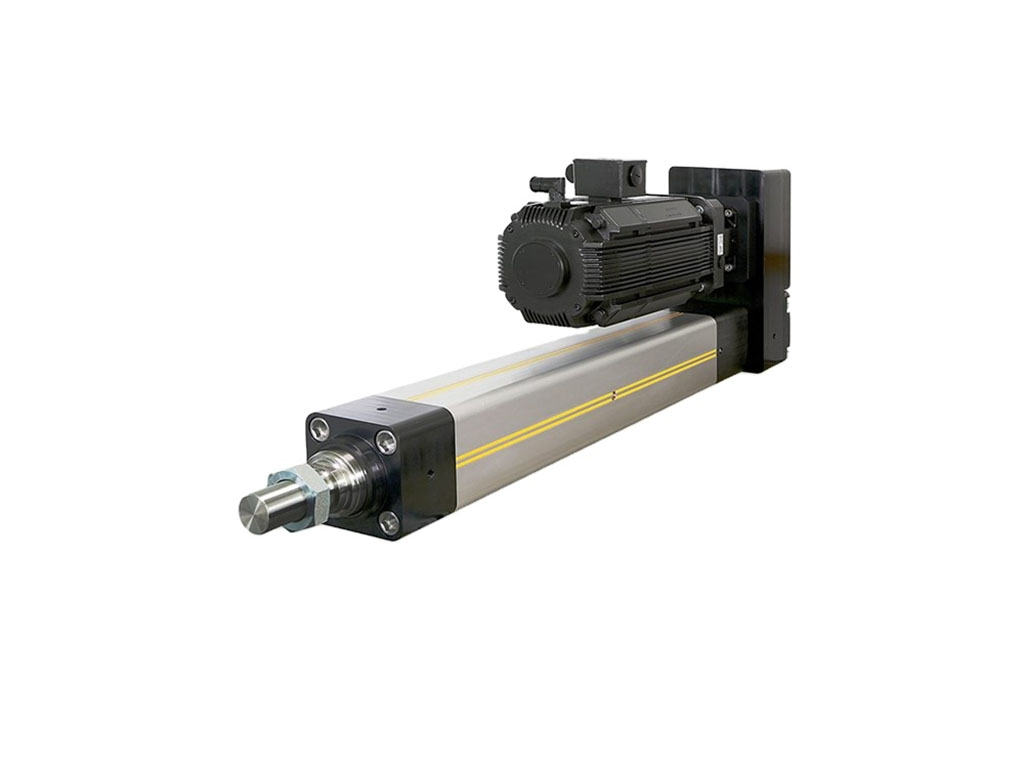
Cost-Benefit Analysis and Long-Term Value
Yes, the upfront cost is higher than that old pneumatic setup. Don’t let that scare you. The payoff comes fast. Lower energy bills, less waste, reduced rework, and fewer warranty claims all add up. Many factories see return on investment within a year or two. Calculate the savings—they’re real.
Maintenance and Lifecycle Management
Hydraulic leaks and worn-out air lines belong in the past. Servo cylinders have fewer moving parts and are easier to keep in shape. Many even support predictive maintenance—they tell you when something needs attention.
Case Study: One large automaker swapped out old-school fluid systems for servo-driven units. They cut adhesive waste by 15% and rework by 20% almost overnight. That’s real money back in the budget. (Read more about electric cylinder ROI)
Key Data Insights: The Impact of Servo Technology on Automotive Manufacturing
Benefit | Data Point | Source |
---|---|---|
Energy savings | Up to 80% vs. pneumatics | Festo |
Precision | ±0.01 mm, force within 1% | Bosch Rexroth |
Material reduction | 15% less waste, 20% less rework | Automation.com |
EV trend | Servo tech critical for battery packs | IndustryWeek |
Future Outlook: The Evolution of Automotive Sealing with Smart Automation
Smart factories are coming. Servo cylinders fit right in—with Industry 4.0, IoT, and AI. They make it easy to collect data, spot problems, and fix them before they slow your line. As cars change (think lightweight designs, composite bodies), only servo cylinders have the flexibility to keep up. EV growth just makes their value greater.
FAQ
What are the primary benefits of using servo cylinders in automotive manufacturing?
You get top accuracy, repeatability, and control, which boosts quality and cuts costs.
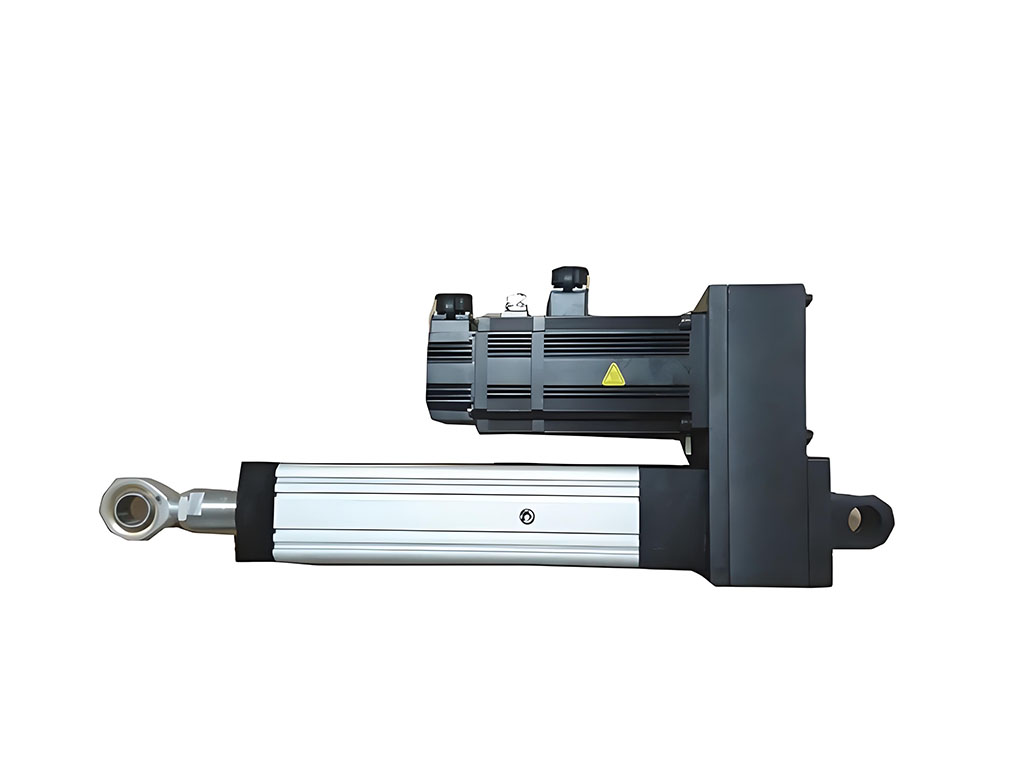
How do servo cylinders differ from traditional pneumatic or hydraulic cylinders for sealing?
They use electric motors (not fluids), giving you digital, precise control and real-time feedback.
Can servo cylinders improve the consistency of adhesive dispensing in automotive assembly?
Yes—they give you a steady, perfect bead every time.
What specific automotive components use servo cylinder-enhanced sealing processes?
Think windshields, body panels, engine gaskets, transmission seals, and EV battery packs.
Are servo cylinders more energy-efficient than other industrial actuators?
Absolutely. They only use power on demand, slashing energy use.
What is the typical ROI for implementing servo cylinders in an automotive sealing line?
Many see full payback in one to two years.
How precise are servo cylinders in force and position control for sensitive sealing tasks?
They reach ±0.01 mm and can control force within 1% of rated value.
What are the integration challenges when switching to servo cylinders?
You need to update controls and train operators, but it’s simpler than it sounds.
Which industries besides automotive can benefit from servo cylinder sealing?
Industries like aerospace, electronics, robotics, and medical manufacturing all find value.
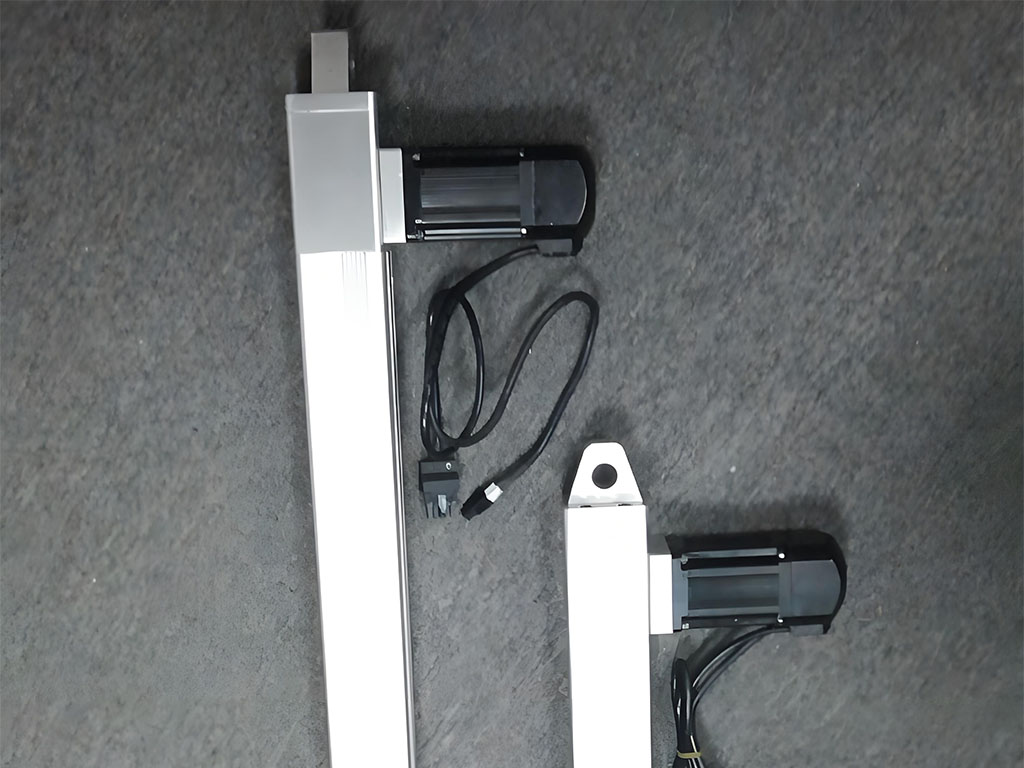
How do servo cylinders contribute to defect reduction in sealing processes?
Better control means fewer leaks, voids, and misaligned seals.
Conclusion & Next Steps
Servo cylinders are changing sealing in auto manufacturing. With superior precision, speed, energy efficiency, and reliability, they solve old problems and open new doors. Whether you want smaller footprints, perfect seals, or better ROI, there’s no smarter move.
We at Jimi Technology bring deep experience and top-notch electric cylinder solutions. Our products set new standards for quality and durability. Let us help you reimagine your line—choose servo technology and turn every sealing job into a win.
Ready to level up? Explore more about our electric linear actuators, see the cutting edge at our Servo Linear Actuator Factory, or compare industrial automation actuator options. Your next step starts here. We’re here for every question and project—let’s make your next car the best-sealed on the road.