Imagine you press a button and heavy machinery moves with perfect power and smoothness. Now, think about needing to lift a steel plate in a factory or push a heavy package along a conveyor faster than ever before. Do you need automation for higher accuracy, less manual labor, and better control? It all starts with knowing exactly how much force and speed you need—and how to calculate them. If you get this wrong, your production line can stall, parts can break, and you’ll waste energy and money. So, let's dig in and see just how easy it is to get these numbers right.
Understanding Electric Cylinders: The Foundation of Linear Motion Control
An electric cylinder changes electrical energy into straight-line movement. You might call it a push rod, actuator, or electric piston. Inside, it has simple but smart parts: a powerful motor (could be a servo or stepper motor), a lead screw (like a strong metal spiral), a nut, covers, and sometimes a gearbox to make movement even smoother or stronger.
Why do so many engineers and tech pros now use electric cylinders instead of old-style hydraulic or pneumatic systems? For starters, electric cylinders bring:
- Precise control of position, speed, and force
- Energy efficiency (they use only the power you need)
- Clean operation (no leaking oil or hissing air)
- Less maintenance
The secret? The motor spins the lead screw, like turning a bolt, and the nut rides up or down. This rotary motion turns into linear force—moving what you need, exactly where you need it.
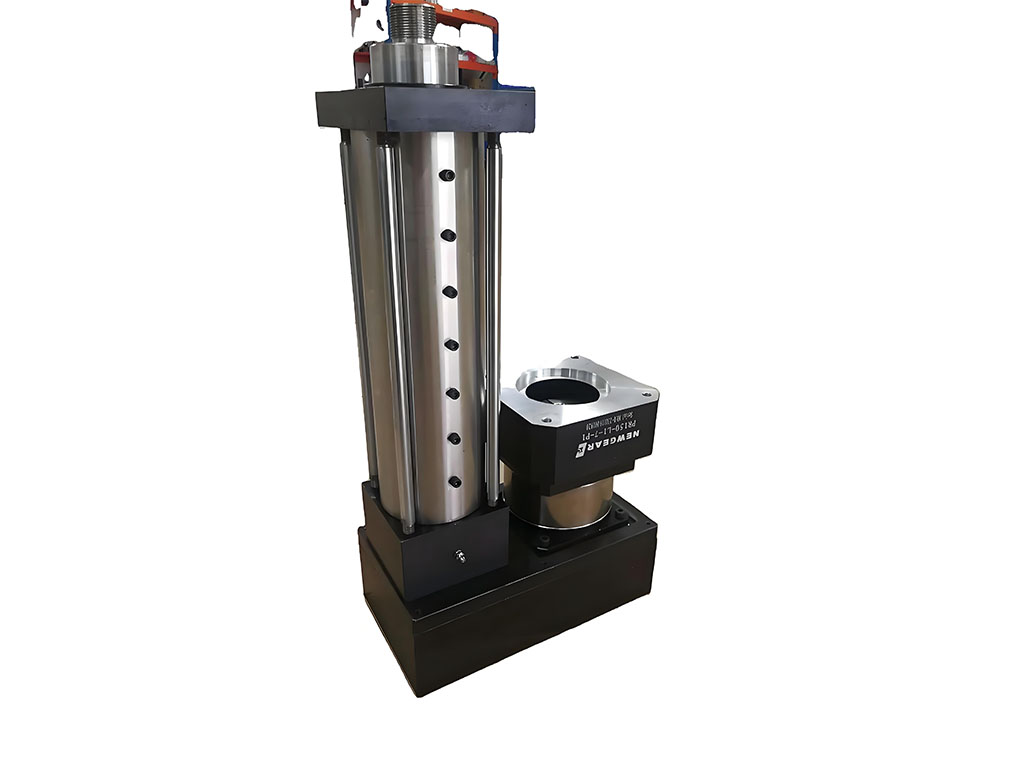
Deconstructing Electric Cylinder Force Calculation: Formulas and Factors
What is force here? Think “thrust”—how much push or pull the cylinder gives. But not all force is the same:
- Static force: The muscle needed to hold a load in place (like keeping a door open)
- Dynamic force: The muscle needed to move something (overcoming friction, speed, or lifting)
Identifying All Required Force Components
Before you size up an actuator or electric cylinder, add up all these bits:
- Load Force (F_load): This is just the weight or mass you’re moving. If you lift vertically, it’s the full weight. For sideways motion, it's less, but friction matters more.
- Friction Force (F_friction): Friction is like trying to slide a box over the floor. The formula is easy:
F_friction = µ × F_normal
Where µ is the friction number (static for starting or kinetic for moving) and F_normal is the normal force (usually the object’s weight).
- Acceleration Force (F_acceleration): Need a fast start or stop? You’ll need extra force:
F_acceleration = m × a
(m is mass, a is how fast you change speed)
- External Forces: Don’t forget springs, wind, or other pushes or pulls.
Essential Formulas for Total Required Force and Motor Torque
Add these up:
- F_total = F_load + F_friction + F_acceleration (+ F_external)
- To get from force to the motor’s needed muscle (torque):
F_thrust = (T_motor × 2 × π × η) ÷ P_screw
Where:
- T_motor: motor torque
- η: lead screw efficiency
- P_screw: lead screw pitch
If your setup uses a gearbox, adjust for the gear ratio so the motor and screw are speaking the same language.
The Critical Role of System Efficiency and Safety Factors
Nothing in the real world is 100% perfect. Ball screw efficiency (η) is a measure of wasted motion:
- Ball screws: usually 85–95% efficient
- Acme screws: often 20–50% efficient
Not sure about hidden loads or sudden shocks? Use a safety factor:
- Industry recommends at least 1.2–2.0× your calculated force
- This extends life and avoids surprises when things get tough (see source)
Mastering Electric Cylinder Speed Calculation: From RPM to Linear Velocity
Speed sets how quickly your automation system does its job. In other words, how fast does the actuator push or pull?
Key Variables for Precise Speed Determination
Speed depends on:
- Motor Rotational Speed (RPM): How fast the motor spins per minute
- Lead Screw Pitch (P_screw): How far the nut slides with one full turn
- Gearbox Ratio: If you use gears, it can slow down or speed up the output
Essential Formulas for Linear Speed Calculation
Here’s the simple math:
- Linear Speed (V_linear) = (Motor RPM × P_screw) ÷ 60
- With gears:
V_linear = ((Motor RPM ÷ Gear_ratio) × P_screw) ÷ 60
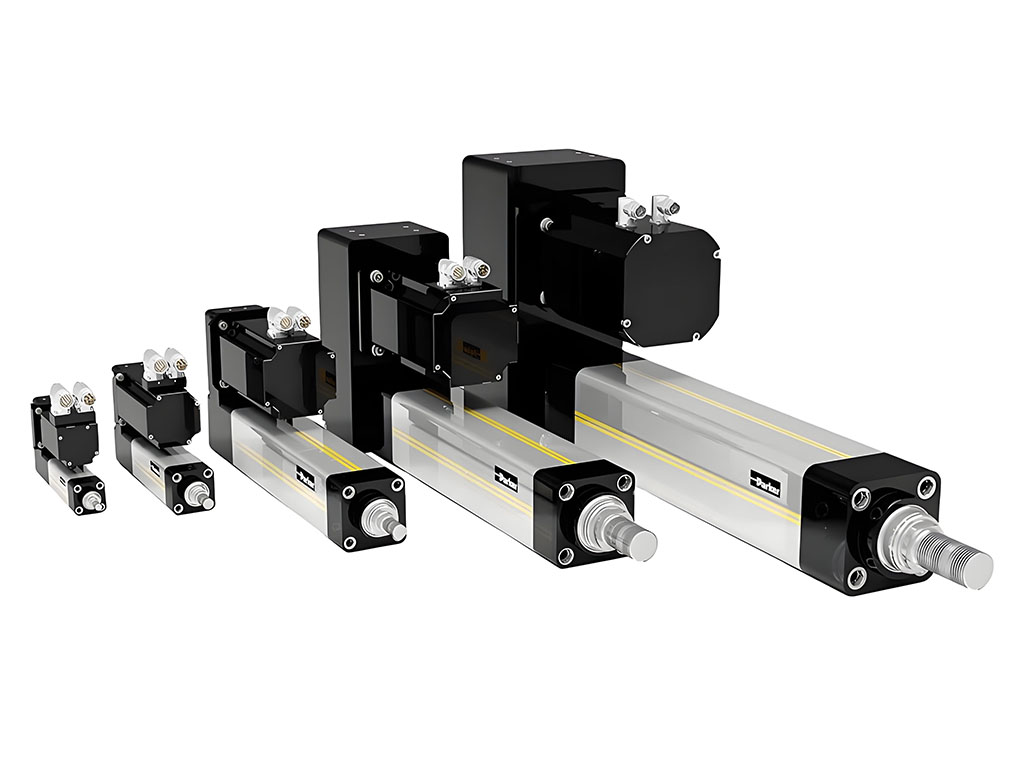
Remember: fast changes (acceleration and deceleration) change average speed, so leave room for that when sizing your system.
Practical Application: Step-by-Step Calculation Examples
Let’s put it all together.
Example 1: Vertical Lift
- Load: 200 kg (about 1962 N, since 1 kg = 9.81 N)
- Lead screw pitch: 5 mm per turn
- Motor RPM: 1200
- Ball screw efficiency: 90%
- Friction: 0.1 (lubricated)
- Acceleration to reach full speed in 2 seconds
Calculate Total Force:
- F_load = 200 kg × 9.81 m/s² = 1962 N
- F_friction = 0.1 × 1962 N = 196.2 N
- F_acceleration = 200 kg × (final speed ÷ 2 s). Say we want to move 100 mm in 2 s:
Final speed = 100 mm ÷ 2 = 50 mm/s = 0.05 m/s
Acceleration = 0.05 m/s²
F_acceleration = 200 × 0.05 = 10 N
- F_total = 1962 + 196.2 + 10 = 2168.2 N
Torque Needed:
- P_screw = 5 mm = 0.005 m
- T_motor = (F_thrust × P_screw) ÷ (2 × π × η)
T_motor = (2168.2 × 0.005) ÷ (2 × 3.14 × 0.9) ≈ 1.92 Nm
Linear Speed:
- V_linear = (1200 × 5) ÷ 60 = 100 mm/s
Example 2: Horizontal Push
- Load: 100 kg (981 N)
- Friction (dry steel): 0.7
- P_screw: 10 mm
- Motor RPM: 600
F_friction = 0.7 × 981 = 686.7 N
Total force = 981 + 686.7 = 1667.7 N
T_motor = (1667.7 × 0.01) ÷ (2 × 3.14 × 0.9) ≈ 2.95 Nm
Speed = (600 × 10) ÷ 60 = 100 mm/s
Need a deeper dive for your scenario? Tools like China Electric Cylinder Factory offer guides and calculators for all applications.
Crucial Considerations for Optimal Sizing and Performance
Duty cycle—the on/off time for your actuator—matters more than you think. A high duty cycle can cause the motor to overheat, shortening its life (read Bosch Rexroth’s take). You must always check the motor’s torque-speed curve, so it doesn’t lose power or cook itself at high speeds (find more here).
Other details:
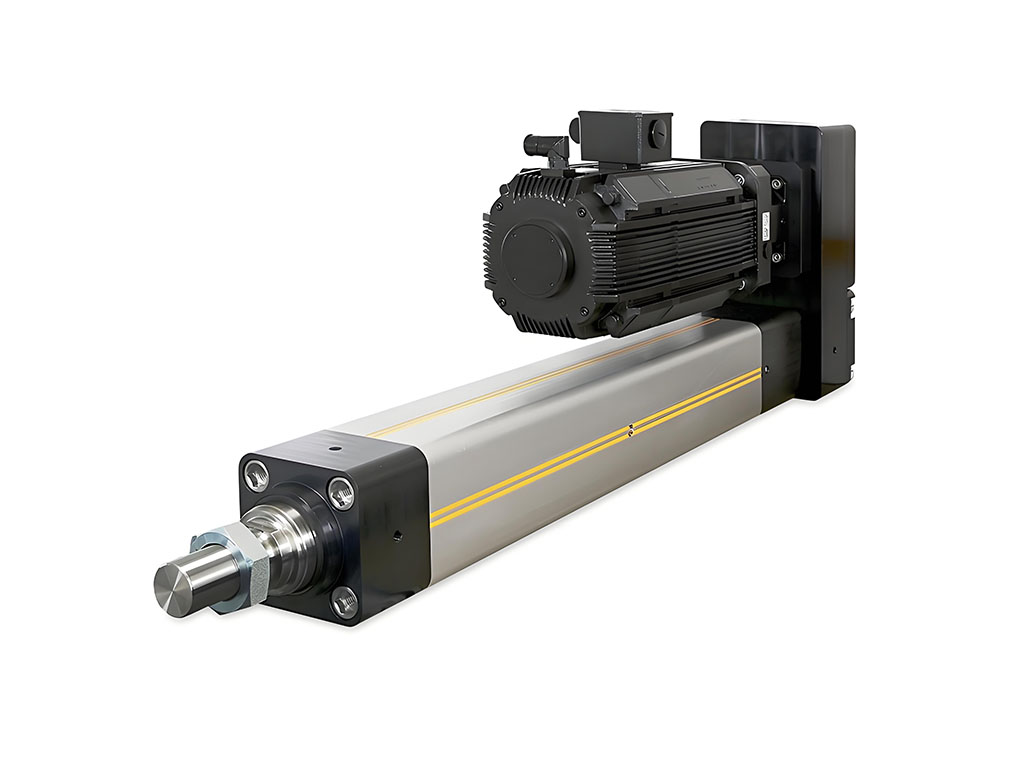
- Thermal management: Keep things cool, especially for heavy use.
- Accuracy: For robots or test equipment, repeatability is king.
- Lifetime: Loads and speed can wear out screws and bearings fast.
- Environment: Dust, rain, or heat all change what parts work best. Consider stainless steel or waterproof options.
Need even more details? For tough environments, check specialized models like Waterproof Linear Actuators or Stainless Steel Actuators.
Key Data Insights for Electric Cylinder Sizing
Parameter | Typical Values / Notes |
---|---|
Ball Screw Efficiency (η) | 85%–95% (source: Thomson Linear) |
Acme Screw Efficiency | 20%–50% |
Friction Coefficient Steel | 0.7 (dry), 0.1–0.2 (lubricated) (Engineering Toolbox) |
Safety Factor | 1.2–2.0 |
General Motor Sizing | Check load, speed, and especially duty cycle |
FAQ (Frequently Asked Questions)
How do you calculate the force of an electric actuator?
Add up load, friction, and acceleration forces. Use F_total = F_load + F_friction + F_acceleration.
What is the formula for electric cylinder force?
Use the formula above. For torque, F_thrust = (T_motor × 2 × π × η) ÷ P_screw.
How do you calculate electric actuator speed?
Multiply motor RPM by lead screw pitch; V_linear = (RPM × Pitch) ÷ 60.
What factors affect electric cylinder force and speed?
Load, friction, acceleration, lead screw type, motor torque, and pitch.
How to size an electric cylinder for an application?
List all forces, add a safety factor, check speed, and match them to the cylinder’s specs.
What is the difference between an electric cylinder and a pneumatic cylinder regarding force?
Electric cylinders control speed and force with precision. Pneumatic cylinders need air pressure and can be less accurate.
How much force can an electric linear actuator generate?
It depends on the design—some Jimi cylinders push over 30 tons!
What is screw lead (pitch) in electric cylinders and how does it affect calculations?
Pitch is the distance moved per turn—bigger pitch = faster speed, lower force.
How do you calculate motor torque required for a linear actuator?
T_motor = (F_thrust × P_screw) ÷ (2 × π × η).
What is the efficiency of a ball screw and why is it important?
Ball screws are 85–95% efficient, meaning more power goes to moving your load—not wasted as heat.
Conclusion & Next Steps
To get electric cylinders right, you need clear math and real-world wisdom. At Jimi, we combine decades of experience, top manufacturing, and detailed guides so you don’t make costly mistakes. For extra support, check our Electric Cylinders page, Servo Motor Actuators, or Ball Screw Actuators. Trust Jimi to help you turn tough motion control ideas into reliable results.
Not sure what you need? Contact us and let Jimi’s experts walk you through every step—because when you get force and speed right, your automation really moves.