Linear guides: you barely notice them when things run smooth, but once they start acting up, your whole line grinds to a halt. Every seasoned machine operator or plant manager has faced it. Your CNC, robot, or conveyor starts making that odd grinding sound or a bearing block creeps along instead of gliding. Production slows, costs climb, and that so-called “simple fix” turns into a lengthy nightmare.
Let’s be honest. Nobody wants downtime or the cost that comes with a breakdown—especially when a bit of daily care can ward off most linear guide headaches. At Jimi Technology, we know linear guides inside out. We live and breathe linear motion—from electric linear actuators to robotic automation equipment. We’ve seen it all. That’s why we want you to have this easy list. Here’s how to keep your guides (and your sanity) intact.
Why Proactive Linear Guide Maintenance Matters
Catching a linear guide problem early beats the shock of a sudden breakdown every time.
Here’s what daily attention brings:
- Reduced Downtime: Quick visual checks help you spot issues before they snowball. Avoid stalled lines and stop losing money to production halts.
- Significant Cost Savings: Every $1 spent on basic preventative maintenance can save you $3–$5 in expensive repairs and lost output.
- Improved Machine Performance: Well-maintained guides mean your machines hit their marks—precision, repeatability, efficiency. No fighting with stubborn slides or ruined parts.
- Enhanced Safety: Equipment running at peak reduces the risk of accidents caused by a guide suddenly seizing or a bad misalignment flinging parts where they don’t belong.
Most failures can be caught early or prevented altogether following a linear guide maintenance schedule. Let’s dive right in.
The 5 Essential Daily Tips for Linear Guide Longevity
- Daily Visual Inspection for Contamination
Every morning, before you start your shift, give your linear guides a quick but focused look.
Why? Dust, metal shavings, coolant splashes, or even a bit of rust can act like hidden sandpaper. They grind away at the moving surfaces and shatter delicate wiper seals. Up to 80% of linear guide failures start with dirt or poor lubrication.
- Action: Use a clean, lint-free cloth to sweep away visible contaminants on both guide rails and bearing blocks.
- What to look for: Discolored lubricant, chips, built-up grime, or rust.
- Red flag: Grease that looks black or unusually runny signals trapped debris or excessive heat—this needs attention.
Even with quality seals, junk finds a way in. Removing it daily extends the service life of your system, keeping your linear guides running just as smooth as when you first installed them.
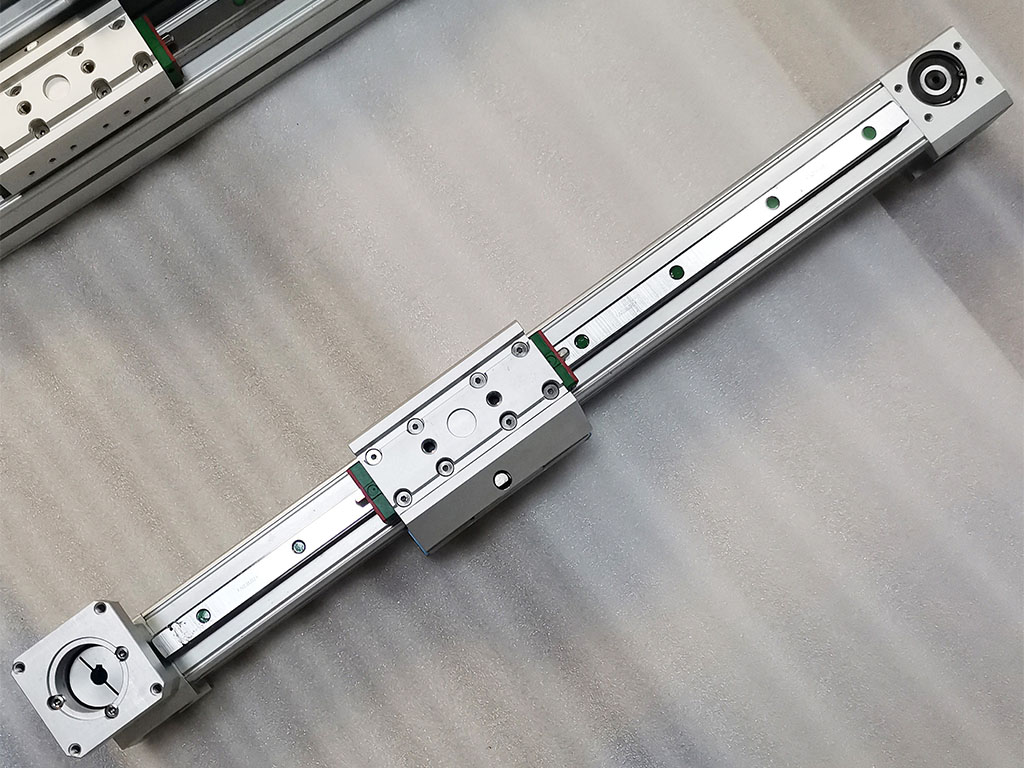
This practice lines up with the “5S” workplace method—smart, simple, and effective.
- Confirm Adequate Lubrication & Re-grease (If Needed)
You wouldn’t run your car without oil. Same goes for linear guides. A guide running dry wears out shockingly fast.
- Action: Check that a thin, even layer of grease or oil coats the rails.
- What to look for: Any sign of dryness or heavy buildup at the ends.
- If dry: Use a correct grease gun, or other recommended method, to reapply lubricant. Follow the instruction manual from the original equipment manufacturer (OEM); over-greasing can cause as much trouble as under-greasing.
Using the proper lubrication type for linear guides, as chosen by makers like THK, Bosch Rexroth, or NSK, prevents all sorts of nightmares—friction, corrosion, heat buildup, and even warranty issues.
Lubrication isn’t an afterthought. Skipping it slashes service life by up to 80%. Keeping up every day can boost linear guide fatigue life by 3 to 5 times. That’s not marketing fluff—that’s what the top industrial studies show.
- Listen & Feel for Abnormal Operation
Sometimes it’s not what you see, but what you hear—or feel.
Odd clicks, squeaks, or grinding sounds mean trouble brewing under the surface. So does any “hitch” or roughness in motion.
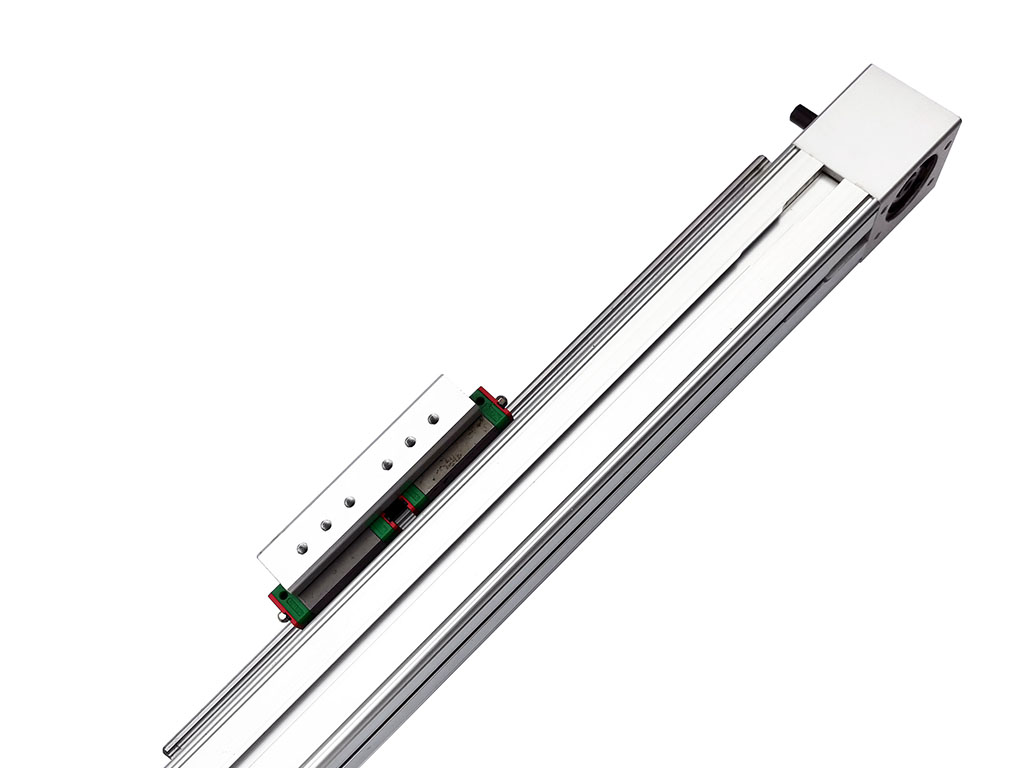
- Action: Move the axis (by hand or jog mode if safe), and listen up. Watch for sluggishness, binding, or too much vibration.
- Why this matters: Sensory cues, like a whine or jerky motion, signal trouble such as wear, misalignment, or a lurking object inside the raceway.
- If you detect an issue: Don’t shrug it off. Call in a qualified maintenance tech right away.
Many veteran operators swear by this tip. The best can spot a looming failure just by the feel of a handle or a faint off-key note in a machine’s song.
- Briefly Check Mounting Bolt Integrity (Visual)
Ever seen a linear guide flop around because a mounting bolt came loose? It’s not pretty.
Each bolt holds system rigidity. One gap, and the whole picture gets out of whack.
- Action: Scan for gaps under bolt heads, visible shifting, or metal dust rings.
- What to do: If you spot movement, alert maintenance to do a full torque verification with the correct wrench.
- Why it’s non-negotiable: Loose bolts lead to misalignment, increasing vibration and early wear. Even a small slip can slash the lifespan of your system in half.
While a torque check isn’t daily, this quick visual pass lets you catch problems early—before a minor issue becomes a disaster.
- Maintain a Clean Surrounding Work Environment
Your linear guides may have seals and bellows, but the factory dust, metal chips, and coolant still find cracks.
- Action: Sweep up dust, mop spills, and clear stray chips around machines every day.
- Bonus: Check that guards and covers are in place.
- Quick fix: Replace or adjust any damaged chip guards or seals right away.
A clean workspace protects your guides, reduces contamination, and lessens the need for emergency cleaning or repairs. Think of this step not as tidying up, but as the first barrier against downtime.
Tip: These five steps take only minutes a day, but they’ll save you endless headaches.
Beyond Daily: Building Holistic Machine Health
These daily tips are your shield, but long-term champions take it further.
- Monthly: Remove covers and perform deep cleaning. Inspect for corrosion, check alignment, and change seals if required.
- Quarterly/Annually: Analyze lubricant for contamination or breakdown. Run vibration dampening and thermal scans for predictive maintenance.
- Ongoing: Install automatic lubricators if your system allows. They keep things smooth even in tough industrial environments and help with uptime improvement in high-speed or heavy-duty settings.
Modern manufacturing relies on preventative, not reactive, action. Get tools like acoustic monitoring or thermal imaging if you’re running a high-value or sensitive line. Consider adopting elements of Total Productive Maintenance (TPM) programs, where even operators get involved in daily checks.
For specific linear motion needs, see our guides on Linear Guides & Rails or explore options like Industrial Linear Actuators if you want a complete automation upgrade.
The Tangible Return on Investment of Daily Care
When you build these small habits into your team’s routine, the rewards are easy to see and feel. Here’s what the data (and our decades of customer cases) prove:
Metric | Result With Daily Care | Without Daily Care |
---|---|---|
Expected Service Life | 5–10+ years | 1–3 years |
Downtime Events | Down by 15–25% | Frequent, costly |
Repair & Replacement Costs | 3x to 5x reduction | High, unpredictable |
Product Quality | Consistent high precision | Variable, at-risk |
Operator Safety | Fewer incidents, secure equipment | Greater risk, poor oversight |
- Companies who engaged operators in daily care reported 15–25% fewer breakdowns.
- Guides last 3–5 times longer when kept clean and lubricated.
- Every dollar of preventative maintenance buys $3–$5 in saved downtime and repairs.
This isn’t just theory. We’ve witnessed clients hit targets for production output, unlock major savings, and keep crews safe—all by mastering the art of the daily check.
Strength in Experience: Jimi Is Your Partner in Linear Motion
We at Jimi Technology believe in solutions, not just selling parts.
From top-end linear actuators and industrial automation gear to special options like High-Speed Linear Actuators or Actuators with Position Feedback, we’ve supplied factories, OEMs, and robotics labs worldwide.
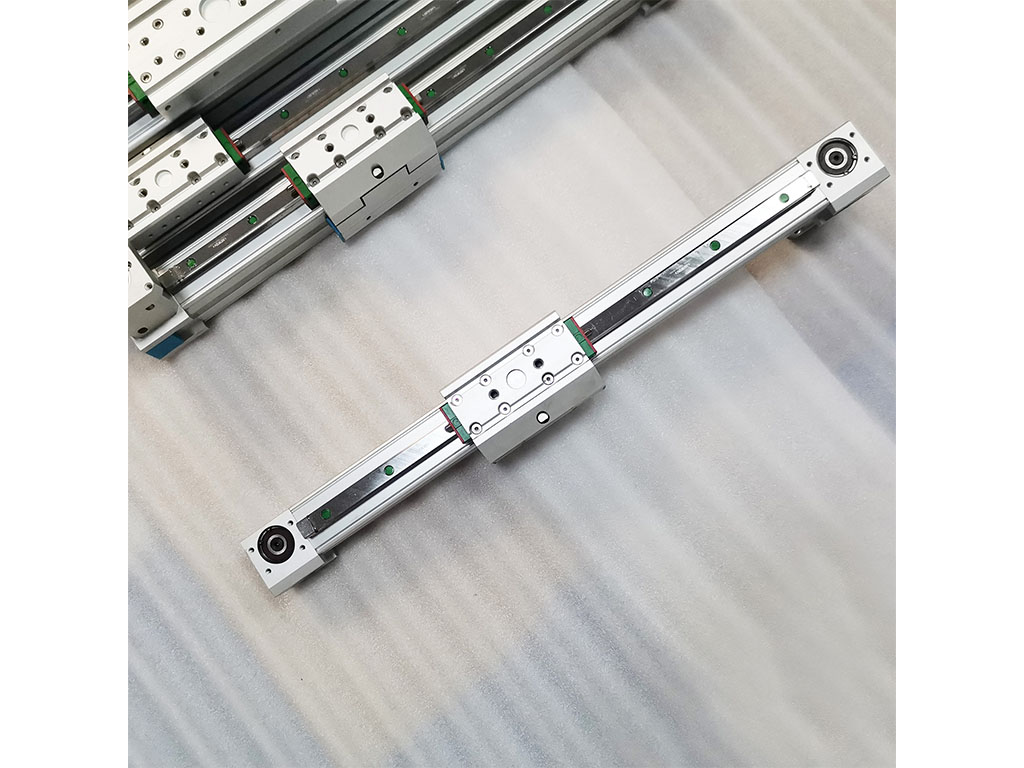
Why trust us?
- Decades of experience manufacturing and supporting precision motion components.
- Globally recognized quality and reliability, rivaling names like HIWIN or IKO.
- Experts available to answer the stickiest maintenance or troubleshooting questions.
- Fast supply for spare parts, from rails, blocks, seals, to mounting brackets.
You don’t have to go it alone. If you need guides for DIY upgrades, advanced Robotics Linear Actuators, or advice for next-gen CNC automation, we’re here.
We provide more than components—we supply knowledge, training tips, and trustworthy service.
Small Habits, Big Impact
At the end of the day, it’s the simple, daily tasks that make the biggest difference. Give your guides a clean sweep, a dab of grease, and a keen listen. Watch your uptime and machine precision soar, and watch those scary “machine down” calls become rare.
Be proactive, not reactive. Protect your investment, empower your team, and let every machine live up to its promise. If you encounter complex issues, don’t hesitate—let a seasoned tech or your OEM service team tackle it.
Now is the best time to transform your linear guides from wear-and-tear components into reliable, long-term assets. Want to upgrade, automate, or just get advice?
Visit our resources or connect with us at Jimi Technology. Let’s build your next level of uptime—one daily habit at a time.